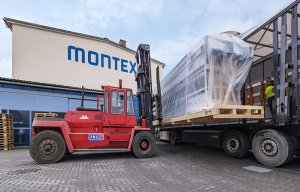
Passing on the know-how at Monforts production site
Automotive fabrics specialist Aunde, which is based in Durban, South Africa, has completed commissioning trials for a new Montex 6500 from Monforts, to ensure improved and faster finishing for both knitted and woven fabrics.
4th June 2013
Knitting Industry
|
Durban
Automotive fabrics specialist Aunde, which is based in Durban, South Africa, has completed commissioning trials for a new Montex 6500 from Monforts, to ensure improved and faster finishing for both knitted and woven fabrics.
Aunde, which designs and develops yarns and technical fabrics, as well as textile and leather seat covers, is currently commissioning a Montex 6500 machine for its finishing line, replacing an older competitive brand stenter.
Sean Kennedy, Aunde’s general manager, said: “Even during the initial trials we were able to see significant improvements thanks to the introduction of new technology with the Montex.”
He added: “lt is so easy to adjust the new stenter. Thanks to the automation and control systems with, for example, weft straightening, the previous manual operation to control ‘bows and squews’ are eliminated.”
“Reproducibility is another key factor in ordering the Montex through the local representative Texmaco. Once set up, the system will run exactly the same, for whatever is required, guaranteeing accurate and exact reproducibility.”
The stenter has been installed in a building purposely set aside for the new unit, together with a flame lamination line.
“Following delivery of the Montex, we have taken the opportunity to streamline the facilities into a more continuous and efficient flow line,” Sean added.
Aunde, the market leader in South Africa for quality automotive interior fabrics, is constantly striving to upgrade its Rossburgh, Durban facility with the latest technology and equipment to further enhance the quality of its production.
The present site started business in 1946 under the name Silknit, later changing to South African Fabrics and then Courtaulds Textiles S.A and finally MBO in 1992. Aunde invested in the company in 1997 acquiring a 51% share and changing the name to Aunde TAP. Until 2002, the factory was producing ladies intermit apparel, swimwear and furnishing plus automotive fabrics.
By 2002 the site was 100% owned by Aunde. That’s when the company was restructured to totally serve the local automotive industries including Volkswagen, Nissan, Ford, GM, Toyota and later BMW.
Aunde operates as a fully vertical operation from texturising to laminating finished fabrics. Using 100% polyester, production features flat woven dobby and jacquard, as well as brushed or pol warp knit fabrics.
According to Stuart Maysmith, Aunde’s production/key accounts manager, in four years this trend will move further towards woven fabrics. He recognised that the new 6-chamber Montex 6500 is a highly versatile machine, designed to finish both warp knits and woven fabrics.
Dictated by the OEMs, production is currently about 40% knits and 60% wovens.” But,” added Stewart, “Several manufacturers are still specifying knitted fabrics.”
Featuring a small Goller washing unit in line with the stenter, woven fabrics are washed and fed directly in to the Montex infeed for drying and finishing.
Knitted fabrics are initially preset and passed through the stenter in a first pass, dyed and again passed through the Montex in a second pass for finishing.
During the initial trials, Aunde has been running 250 - 350 gm/m ² knitted fabrics at 18 m /min but Stuart anticipates increasing the speed up to 30 m/min when the unit is fully operational by February this year.
This compares with just 15 m/min with the old competitive stenter.
“For woven fabrics, with weights of 350 – 500 gm/m², we hope to run the heavier fabrics at 20 m/min and lighter ones at 25 m/min; depending on the moisture content,” he added.
Aunde anticipates increasing production by 20 per cent within 12 months led by the new Montex stenter.
Sean Kenney explained that the South African market for cars, comparing to the past, is now allowing higher production more cost effectively for the export market.
He commented: “As a result demand for fabrics with a higher specification is being required. We therefore need to embrace the new technology and not only meet the increased specs but exceed them in order to move ahead of the competition.”
Aunde Group has specified its production facilities must meet stringent automotive regulations. Key characteristics include:
Business intelligence for the fibre, textiles and apparel industries: technologies, innovations, markets, investments, trade policy, sourcing, strategy...
Find out more