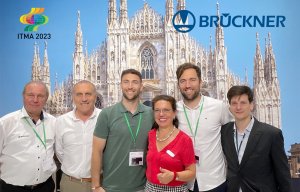
Campos chooses Brückner Power-Frame stenter
The project comprises several stages, which will be realised within the next years and has far-reaching and multi-purpose aims.
16th January 2018
Knitting Industry
|
Leonberg
A joint venture between the state-owned Algerian companies Groupe C&H, TEXALG, SNTA and the Turkish Group TAY, with more than forty years of experience in textiles, has been founded to build one of the biggest textile mills in the world. German textile machinery producer Brückner Textile Technologies has been awarded the contract for the supply, installation and commissioning of machines for dry finishing.
“The coordination team for the project was selected very carefully. The result was a highly experienced and competent crew, compiled with the aim to select the suppliers according to many different criteria and always striving for the highest standards,” Brückner reports.
The project comprises several stages, which will be realised within the next years and has far-reaching and multi-purpose aims: Algeria will become as independent as possible of textiles imports in the medium term and the project will create a large number of jobs.
On a site of around 2,500.000 sqm and with an investment of US$ 800 million, several vertically structured textile plants will be built in the next few years, specialising in various categories of textile end products. The new company will also have an internal service and training centre for new workers.
Many meetings and a comprehensive exchange of opinions took place in order to outline and optimise the individual specifications of the required machines. On the one hand, the machines should allow an easy operation, and on the other hand, they have to be able to offer many possibilities for automation, quality control and remote maintenance.
The family-run company Brückner was selected based on its ability to meet the three main criteria, which included productivity, quality of the products and highest possible energy efficiency. In addition, the team focused on the available local service, as well as on fast and flexible after sales services.
The first step of the project has been divided into a denim, a non-denim and a knits section. The machinery in question are complete, fully integrated production lines for the production of 12 million pairs of trousers, six million shirts and 12 million T-shirts each year. The scope of supply comprises several stenters, sanforising ranges, thermosol dyeing and highly flexible denim finishing lines. All these machines are custom-made and are provided with various options.
The preparations to realise the next stage, which comprises the production of home textiles, are also already under way.
Business intelligence for the fibre, textiles and apparel industries: technologies, innovations, markets, investments, trade policy, sourcing, strategy...
Find out more