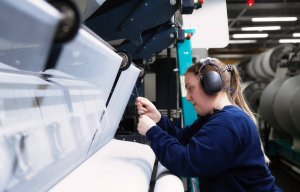
Eurojersey invests in corporate welfare
Alfonso Bonaffini, Head of Quality Management at Mayer & Cie., talks about courage and tough challenges.
27th January 2025
Knitting Industry
|
Albstadt, Germany
Alfonso Bonaffini, together with a team of 15 colleagues, including one in each of the company’s plants in the Czech Republic and China, oversees quality assurance at leading German circular knitting machine manufacturer Mayer & Cie.
Alfonso sees standards and guidelines as “tools to help achieve the core goals of any business”, succeeding in the market and generating profits through consistent quality, satisfied customers, and efficient processes. He sees future opportunities in digitisation, AI tools, and machine learning to enable real-time process monitoring. Mayer & Cie. recently sat down with Mr Bonaffini to discuss his role and the challenges he faces.
Mayer & Cie. (M&C): How long have you been with Mayer & Cie., and what are your responsibilities?
Alfonso Bonaffini (AB): I have been with Mayer & Cie. since 2014. My main responsibilities include strategic leadership and operational implementation in quality management and quality assurance. I also oversee the teams in our Czech and Chinese plants and serve as the CE compliance officer.
I manage the ISO 9001 certification while my colleague Heiko Hämmerle is responsible for ISO 50001. My work also includes process development, risk analyses such as APQP and FMEA, quality planning, as well as overseeing quality management tasks, including inspection equipment management and monitoring incoming and outgoing goods inspections.
These are extensive responsibilities that we handle as a team of 15 colleagues: 13 are based here, and one specialist in each of our subsidiaries is assigned to our department.
M&C: Can you explain what “strategic leadership in quality management” involves?
AB: When the management wants to optimize processes or new technologies become available, I get involved. For example, consider needle bed inspections: so far, this has been a manual 100% inspection - very time-consuming and demanding. Thanks to modern measuring technology with AI and image recognition, automated solutions are now available that are faster, more precise, and less reliant on personnel availability.
The cam box process can also be automated. Parts are measured, inspected, assembled, and labelled in a cell using robots, advanced sensors, and AI-enabled cameras.
Both systems are custom designed for Mayer & Cie. and ready for implementation.
M&C: You mentioned audits earlier. What’s your role there?
AB: I handle both internal and external audits. Technically, an internal audit is only required every three years in the recertification cycle, but conducting one annually is more effective. This allows us to initiate improvements within a manageable timeframe, keeping unresolved issues visible and actionable.
M&C: Aren’t these frequent audits very time-consuming?
AB: They are, but audits are not an end in themselves. Their purpose is to continuously improve quality and make processes more efficient. That is the core drive of any company. A business wants a product manufactured as well as possible, one that satisfies the customer and avoids complaints. We aim to prevent wasting money on rework, scrap, or miscommunication among colleagues.
Standards act as guidelines for this: they provide a framework that each company can adapt to its unique needs. Moreover, standards offer an additional benefit: as a partner or supplier of a certified company, you automatically gain insight into its setup, documentation, and expertise.
M&C: Are you involved in selecting new suppliers?
AB: It depends. For instance, we recently relocated our Chinese plant and are gradually establishing knitting head production there. This required building a local supply chain for key components, a project we implemented in collaboration with materials management. The critical starting point was ensuring our specifications for potential suppliers were clear and unambiguous.
As a circular knitting machine manufacturer, we have unique requirements - large parts, tight tolerances - that many suppliers cannot meet.
M&C: How has the quality management field evolved over time?
AB: The focus in quality management is increasingly shifting toward digitization and automation. As I mentioned earlier, instead of traditional manual inspections, we now have access to modern digital tools.
M&C: What challenges do you face?
AB: The ever-changing reality we encounter everyday as a company is a major challenge. Compliance issues, such as the CSRD directive, carbon footprint tracking, and supply chain laws, are relatively predictable.
But we also have to contend with fluctuating energy prices, supply chain disruptions, and geopolitical tensions. For example, if ships must bypass the Suez Canal and take the route around Cape Horn, shipping takes longer and costs more.
Climate change also impacts our business. Are our suppliers affected by natural disasters like floods? Do we have alternative solutions?
These situations present unique challenges for quality officers. We value structure, clear processes, and meticulous documentation, but these come at the cost of speed - something often required. So, we must learn to be bold, which I believe will influence our work culture in the future.
M&C: Which project are you particularly proud of?
AB: The needle bed hardening project stands out. We were using outdated induction hardening machines in a largely manual process. Procuring spare parts became increasingly difficult, the energy efficiency was poor, and there were customer complaints.
Together with production, we opted for an automated solution using state-of-the-art control and laser technology. This improved quality, the overall process, and energy efficiency. I was heavily involved in this project, and I am proud of the outcome.
M&C: What drives you personally?
AB: I enjoy tackling tough challenges, especially when no one seems to have a clear solution. Solving hard problems is what excites me.
M&C: What do you wish for Mayer & Cie.’s future? Where do you see opportunities?
AB: I hope the market stabilizes so we can return to operating at our usual level. Technologically, we are highly advanced, but there’s always room for improvement, as I’ve mentioned with specific examples.
Overall, I believe we can automate routine tasks to boost efficiency. Data-driven decision-making holds great potential, and I’m convinced that AI assistants can significantly ease our daily work.
Business intelligence for the fibre, textiles and apparel industries: technologies, innovations, markets, investments, trade policy, sourcing, strategy...
Find out more