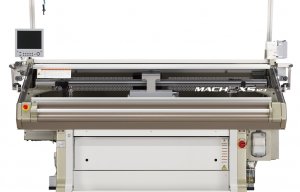
Uniqlo to scale up on-demand Wholegarment production
This article, one of a WHOLEGARMENT series, looks at the impact of the technology on Italy’s knitwear industry and its leading advocates.
9th December 2015
Knitting Industry
|
Reggio, Italy
This year ITMA 2015, the world’s most influential textile machinery exhibition, was held in Milan, Italy, where leading textile machinery manufacturer Shima Seiki celebrated in style. The occasion was the 20th anniversary of the launch of the Japanese company’s WHOLEGARMENT knitting, a revolutionary flat knitting technology that allows the production of ‘seam-free’ knitwear. Following on from the celebrations at the show, this article, one of a WHOLEGARMENT series, looks at the impact of the technology on Italy’s knitwear industry and its leading advocates.
Earlier this autumn I visited Reggio Emilia, a city in northern Italy in the Emilia-Romagna region with a population of around 170,000 people. The region is famous for foods such as Parmigiano-Reggiano cheese and wines like Lambrusco, as the economy of the province was for a long time based on agriculture. In the twentieth century however, Reggio Emilia saw the rapid development of its light industry and it also became known as the home of a number of leading fashion houses, including the prestigious Max Mara clothing line which is headquartered in the city.
Zanni Maglieria is a family business with 21 employees based in Reggio, which is owned and managed by father and son team Mauro and Marco Zanni.
Taking pride of place in the company’s reception area is an old but impeccably refurbished Simonini hand flat knitting machine which Mauro Zanni learned to knit on. When Mauro was a young boy his mother taught him to use the machine and as he grew, he would knit and she would link garments. Then Mauro would get on his bicycle to go and sell the knitwear to local customers.
You could say therefore that knitwear is ‘in the blood’ for Mauro Zanni. Its still very much a family affair at Zanni Maglieria, with Mauro’s parents still living in the house behind the factory. During our meeting Marco gets a number of calls on his mobile phone and then leaves to attend to his ageing grandparents needs.
On the surface it is good old fashioned Italian ‘family first’ artisanal knitwear manufacturing here, but poignantly the Zanni’s are producing exquisite knitwear for some of the world’s top brands. Amongst its customers are Armani, Escada and Max Mara – luxury brands that sell knitwear for hundreds of Euros per piece.
99% of the knitwear which Zanni produces is made on Shima Seiki WHOLEGARMENT knitting machines. As well as a number of NewSWG-V and NewSES machines the company has 10 sets of MACH2X machines in 15 gauge, 12 sets of MACH2X in 18 gauge, 2 sets MACH2XS 15 gauge and 2 sets MACH2XS 8 gauge.
MACH2X is a fairly recent addition to Shima Seiki's line of WHOLEGARMENT specialty machines that features 4 needlebeds and the company’s original SlideNeedle. It knits beautifully shaped, high-quality WHOLEGARMENT products which conform to the body for improved comfort and a more elegant silhouette. As the ‘MACH’ name suggests, speed and productivity are key, with MACH2X achieving a maximum knitting speed of 1.6 metres per second.
The machine’s R2CARRIAGE System additionally permits quicker carriage returns for higher efficiency per knitted course and Split Stitch technique also allows efficient knitting by eliminating empty courses. New to the line-up is 18L gauge capability whereby a special large-hook version of the SlideNeedle is used for knitting 15 gauge fabrics at 18-gauge needle pitch for very high productivity when knitting ultrafine gauge garments. The tighter needle pitch also allows for a tighter fabric especially for ribs, contributing to higher-quality WHOLEGARMENT items.
According to Shima Seiki, dramatic improvements in both quality and productivity make the new MACH2X the ideal machine for high-quality ultrafine gauge WHOLEGARMENT production.
Zanni Maglieria was an early adopter of WHOLEGARMENT knitting technology, being very aware of the importance of ‘first mover advantage’ – the advantage gained over competitors by adopting new technologies early in their development. The company was also the first producer anywhere to make WHOLEGARMENT knitwear for the globally respected fashion house Armani, which has a design and development centre in nearby Modena.
Mauro Zanni started his own company in 1985 and was programming Shima Seiki SEC202FF machines – the leading flat knitting machine of the day. He recalls those days and says: “Let me show you my first Shima computer.” He emerges laughing from a cupboard with a manual tape puncher – a device used to punch paper tape for controlling the machines at the time. Today his technicians use the very latest Shima Seiki APEX 3 Design System to programme their knitting machines.
In the mid nineties, Mauro attended a textile machinery exhibition in Milan where something new caught his eye. “It was the very first Shima WHOLEGARMENT machine – the SWG-V,” he recalls. “I remember it well and I could see that this was something different and it motivated me to do something,” Mauro enthuses.
Subsequently, he bought his first SWG-V 5 gauge WHOLEGARMENT machine in 1998. “This was a new world with many secrets and I understood it,” Mauro says. “It was a new direction and I could see the potential,” he gushes. “Linking is ugly on 5-gauge knitwear and I could see that if I could take out linking by using WHOLEGARMENT technology, I could make something better – improve 5-gauge knitwear.” The project was successful and the company gradually grew its WHOLEGARMENT production in the following years.
Mauro says he can see a future with lots of potential where he can make good business with WHOLEGARMENT technology. With this in mind, Zanni has just completed a new building adjacent to its current factory which will be used to expand the company’s production facilities. The idea here is to improve efficiency and maintain quality as well as increase quantity. “Quality and not quantity is most important here,” Mauro Zanni says.
Mauro says he makes good profits and is very satisfied with the return on investment with WHOLEGARMENT technology. “Passion plus profit is WHOLEGARMENT,” he states.
I ask Mauro if he can charge a higher price for WHOLEGARMENT knitwear than fully-fashioned but he tells me he cannot. He says the WHOLEGARMENT knitwear is superior in his view, but he cannot charge more for it.
Mauro thinks that most consumers do not understand the benefits of WHOLEGARMENT knitwear because nobody explains the benefits to them. He thinks this is a mistake and that consumers must be educated about the benefits.
Mauro Zanni has a very positive attitude and even has a rule which his technicians must adhere to when discussing developments with customers – they cannot say no, this cannot be done. He challenges them to come up with technical solutions.
Technical challenge is the motivator for Mauro Zanni. In fact, he thrives on new challenges.
These days Mauro doesn’t programme Shima machines himself – he employs technicians to do that. He does help his technicians resolve major problems though and also invents new stitch constructions which he passes to his technicians to programme. Of course he knows the structures will work.
Mauro Zanni says that the company needs limited support from his supplier Shima Seiki Italia. “We do need training from time to time not much in the way of technical help,” he explains.
As would be expected with the high-end brands and fashion houses, design is provided by Zanni’s customers. But Mauro sees it as his job to help guide the designers and often proposes new techniques which he says they accept.
Mauro says that the market requirement for WHOLEGARMENT knitwear is generally steadily increasing and the same applies for his company. He aims to keep improving his product offer to meet the growing demand.
He shows me a wide range of WHOLEGARMENT samples but it is clear which one of his developments he is most proud of. It takes pride of place on a mannequin in the company’s showroom and is a yoked WHOLEGARMENT style developed a few years ago for the venerated Armani brand. The brief was to come with a style with a transparent zone in the yoke area. Mauro used his inventiveness to create the stitch structured yoke which achieves the objective.
“To have a good company, there are three essential things – capacity, hard work and persistence,” Mauro says. By capacity, he means knowledge, know-how and inventiveness. “WHOLEGARMENT gives me every day motivation. It has lots of scope for invention,” Mauro adds.
Mauro Zanni is clearly a man of vision with boundless passion for WHOLEGARMENT knitting technology. Like many of the companies and entrepreneurs we have interviewed this year about the technology, Mauro could see the potential as far back as 1995 when it was launched. He and his contemporaries who are now producing profitably for some of the world’s leading fashion houses have proved the technology works from aesthetic, technical and commercial viewpoints.
With ITMA2015 returning to Milan this year, 20 years after the launch of WHOLEGARMENT technology, maybe this really is, in the words of Shima Seiki itself – ‘Innovation Coming of Age’.
Lunigiane – A pioneering 21st century WHOLEGARMENT knitwear manufacturer for MAX MARA
Max Mara: A champion of Shima Seiki WHOLEGARMENT technology
New Twins set to become leading player in theatre of WHOLEGARMENT knitwear
MIND Srl – A WHOLEGARMENT Success Story from Italy’s Veneto Region
WHOLEGARMENT knitting technology helps set New Esse Maglieria apart from its competitors
WHOLEGARMENT investment cuts labour costs and creates new opportunities for Sabry Maglieria
La Trama: A WHOLEGARMENT Powerhouse in Italy’s Marche Region
Business intelligence for the fibre, textiles and apparel industries: technologies, innovations, markets, investments, trade policy, sourcing, strategy...
Find out more