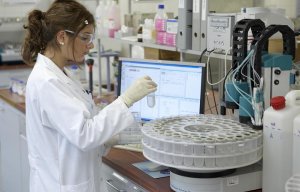
Oeko-Tex releases new regulations for 2017
The new version of the STeP standard includes updates and improvements in different areas, sayd David Pircher, a Business Development Manager at Oeko-Tex.
1st April 2015
Knitting Industry
|
Zurich
The International Oeko-Tex Association headquartered in Zurich, Switzerland, was founded in 1992 by the Austrian Textile Research Institute and the German Hohenstein Research Institutes. Currently, its membership includes 16 independent textile research and testing institutes with 51 offices in 62 countries.
To date, 32 production facilities around the world have successfully received STeP certification. Some of the latest companies include Rivolta Carmignani S.p.A. and Besani SRL in Italy, PT. Idaman Eramandiri as the first Indonesian company, Hermann Koller AG in Switzerland, Elvy Weaving SAE in Egypt, and Mondol-Knit-Tex as the first company to receive STeP certification in Bangladesh.
“Very satisfied. The number of STeP certifications issued has risen substantially over the last few months. Importantly, the overall number of inquiries has dramatically increased which illustrates the desire companies in the textile supply chain have for improving their sustainable practices specifically focused on the environmental, chemical and social fronts.”
“The interest in STeP goes well beyond the penetration we saw in what was known as the Oeko-Tex Standard 1000, which was the precursor to STeP. We expect the acceptance of STeP to rise, particularly as we include many suggestions from our customers in the new edition of the STeP standard, which will be published on 1 April 2015.”
“It varies. We have customers from Europe, Asia, Africa and South America. To date, companies from a total of 22 countries from around the world have received STeP certification, e.g. Germany, Switzerland, Italy, China, India, Bangladesh, Indonesia, Brazil etc. In addition, production sites at all production levels along the value-creation chain, from fibre manufacturing to textile logistics centres, have successfully received certification.”
“Apart from the certificates that have already been issued, roughly a dozen companies are waiting to be audited. There are about 40 production sites which are currently completing the online assessment as well as 60 incremental companies which have declared their interest and registered for STeP certification.”
“The certifications of Mondol Knit-Tex Ltd. and Danys Knitwear Ltd. in Bangladesh are certainly worth mentioning as these show that, even though certain production countries receive a lot of criticism and we often hear about bad practices, there are companies in these countries which are willing to accept responsibility for the environment and, in particular, for their employees.”
“The STeP certificates for the Brazilian silk mill Fiação de Seda Bratac S.A. and the Estonian leasing company Seegers Eesti OY are also worth mentioning because they highlight the variety of production companies along the textile chain. In spite of the differences in the individual companies, STeP is flexible enough and has been adapted to the textile industry in such a way that we can provide equal support to all customers.”
“STeP is the most comprehensive certification in the textile industry. In contrast to other certifications and management systems, which often only concentrate on narrowly defined areas such as social responsibility or occupational health and safety, STeP analyses all relevant parts of the company to gain as meaningful an assessment as possible with regard to the achieved level of sustainability.”
“The three-stage scoring system for STeP also offers companies an optimum basis for effective benchmarking. Our evaluation of the online assessment and the subsequent company audit clearly show where there is still the potential for improvement. In addition, the assessment tool clearly shows how the sustainability assessment for the individual modules, as well as the overall assessment, have been reached. The continual performance improvement achieved in the six areas of Chemicals Management, Environmental Performance, Environmental Management, Social Responsibility, Quality Management and Safety in the Workplace is the basic principle on which STeP certification is based.”
“However, what our customers also value about the STeP system is the specific customisation to suit their situation within the textile value-creation chain. Our 16 member institutes are very familiar with the products and business procedures of the respective processing levels. Oeko-Tex is thus able to define feasible requirements for what must be assessed for sustainable production while competently reviewing whether the specified criteria have been met on site with the companies.”
“Broadly speaking, STeP improves a corporation’s image. Companies can communicate their services in a believable way as a result of independent third-party certification. Importantly, with STeP, the scoring related to individual processes within the company as well as the overall assessment of the company, displays the number of quantifiable environmental and social criteria in the form of a simple assessment scale which can be compared with regard to changes over time.”
“The detailed consideration of the individual production processes in collaboration with the Oeko-Tex Auditor means that the companies benefit from not only the certification, but the process of certification as well. Dye works and textile finishers can, for example, save large quantities of fresh water through technically optimized recycling and reuse of waste water. If carried out with vision and know-how, fresh water consumption can be reduced by up to 70% or 80%. The same also applies for other manufacturing processes and all types of machines used. Innovative ideas and the use of the best available technologies generally enable enormous savings in primary resources, from waste heat utilisation to the recycling of production waste to lighting the production halls with energy-saving light bulbs.”
“Regardless of location, companies tend to have the most challenges around Chemicals Management. Many companies have a chemicals warehouse and have, in one way or another, organised appropriate administration of the substances used. However, many companies lack awareness for the proper registration of all chemical auxiliary agents used as well as the definition of responsibilities and precise knowledge of substances used. This type of discipline is needed to successfully assess and minimise the risks of handling. For this reason, STeP requires mandatory systematic documentation and responsible handling of all chemicals required for production.”
“The other STeP modules do not tend to show a pattern and the scoring results vary from company to company. If you look at the Best Practice examples from companies, we have often seen that some companies in Europe sometimes only meet the minimum requirements prescribed by law. In contrast, in Asia, there are definitely individual companies which are ahead of European companies as they have a high level of motivation and an understanding of the importance of sustainable technologies, safety in the workplace and a good working environment. This may, of course, be due to the fact that production locations in Asia are under much closer scrutiny with regard to bad practices than companies in Europe. However, it is in fact not always the case that European companies are automatically ahead with regard to sustainability.”
“The new version of the STeP standard includes updates and improvements in different areas. For example, we have introduced an additional passage to the topic of "Ethics and Compliance" and expanded the existing requirements in the "Social Responsibility" module. Two additional banned processes have been added and we have tightened the limit values for PFOS and PFOA as well as for nonylphenol, octylphenol and its ethoxylates. We have also modified our MRSL, the list of restricted-use chemicals for textile manufacture.”
“As a supplement to STeP certification, we presented our MySTeP database last year. This is a tool with which companies can analyse and manage their whole supply chain from a sustainable point of view, and not just the individual production facilities. This ability is particularly important for larger companies such as brands or retailers but can also be helpful for smaller or medium-sized manufacturers if they have not yet established their own analysis systems. MySTeP is a separate Oeko-Tex service and can be used by companies who do not have any Oeko-Tex certification themselves. However, data from all STeP certified companies is available in the database for registered users so that key performance indicators (KPIs) from the STeP assessments can be used to optimise or reorganise their supplier relationships.”
“An incremental addition to our product portfolio is the recently launched Made in Green by Oeko-Tex label. This displays the services provided by textile companies along the supply chain with regard to human-ecological safety and responsible manufacturing conditions directly on the product and thus enables transparent communication throughout the supply chain, all the way to the end consumer.”
“And with regard to the STeP standard itself, we are constantly improving. Thanks to the input of our customers, several ideas are already in the pipeline. For example, it is planned to further develop the audit report so that, in the future, the assessments can be displayed in an even clearer and more informative way.”
Business intelligence for the fibre, textiles and apparel industries: technologies, innovations, markets, investments, trade policy, sourcing, strategy...
Find out more