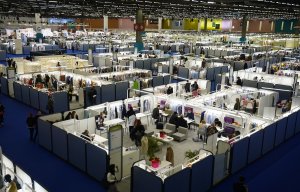
Première Vision Paris: Another step towards normality
'Transforming Fashion in the Digital Age', introduced the latest innovations, providing solutions to remote working that promote visual communication
27th August 2020
Knitting Industry
|
Webinar
Beth Ranson reports
For designers, clear communication of design intentions to manufacturers is essential. Achieving clarity can be time consuming and create waste, involving ‘back and forth’ discussions over technical specifications.
Within a design team, communication of knitted fabric concepts to non-knitters can be challenging. Inspired ideas are often dropped pre production to avoid perceived risk from buyers or designers who cannot envisage the design proposal.
Shima Seiki’s 3D virtual sampling capabilities, through their new remotely accessible ‘APEX FIZ’ https://www.shimaseiki.com software combined with their new ‘Yarn Bank’ could provide a solution to these problems. Miscommunications between designer and programmer could be reduced, and knitwear visions could be presented to buyers in yarn specific 3D detail. This could drastically reduce material wastage from failed proto samples whilst opening the door to new sustainable concepts.
Combining their digital platforms with their machinery innovations, Shima Seiki aims to create strong connections between design and production. On Tuesday 25th August, they hosted a webinar Transforming Fashion in the Digital Age, to introduce their latest innovations, providing solutions to remote working that promote visual communication and reduce material waste.
Initially introduced over 25 years ago, Shima Seiki’s ‘Total Fashion System’ did not become relied upon for virtual sampling in the way originally envisioned. Many designers continue to rely heavily on physical sampling. Noting their adaptation to new industry demands, Mr Shima explained,
“Previously, actual product samples were considered important in communication of design. Now there is world-wide interest in SDGs and sustainability, and with Covid, more emphasis given to finding alternatives to sample making…The new services we introduce digitally enhance the ‘Total Fashion System’ to provide solutions to offer even better support for customers over these times.”
New anouncements
YARN BANK: Shima Seiki’s new digital access to industry spun yarns for 3D simulation
Shima Seiki’s ‘Yarn Bank’ launches in September 2020. Sharing digital yarn data, designers can search through yarns from industry spinners, download them directly to APEX FIZ, and simulate the yarns within their designs. Although yarn orders cannot be placed through the Yarn Bank, spinner contact details are provided, as well as yarn counts, gauges, fibre content and accurate wash/ production instructions.
Before risking placing an order for yarns and juggling minimum quantities or stock services, designers can produce virtual samples in the shades and counts they require. With travel to yarn fairs restricted and events cancelled, this resource holds particular value at this immediate time.
Verbally describing the textural qualities of a yarn winding during design meetings to convince investment in new yarns is difficult. The Yarn Bank yarns accurately convey texture in stitches, alleviating this problem as fibres are depicted in impressive definition. Designers can present fabric options without wasting materials, as stitches can be trialled in a variety of yarns for direct comparisons (as below images).
New functions
‘Search Similar Patterns’ is a new tool. By uploading an image and adjusting an area around a particular structure or pattern, it will search for the most similar stitch structure in the 1500 options of the stitch database. Regularly inspired by structures, patterns and textures within visual inspiration, this is a tool with a true textiles focus. Generating stitch inspiration and suggesting stitches that designers may never have considered bridges connections between visual research narratives and the textiles.
Released in October 2020, APEX FIZ adapts APEX to diversified remote working styles whilst maintaining the strength of the conventional APEX software.
3D visualisation in itself is a brilliant feature for remote working, but combined with the fact that APEX FIZ automatically produces technical data for samples, this means designers with no programming knowledge can immediately bridge the gap in their knowledge. Along with their design visuals, designers can share their technical programming information directly with manufactures and programmers.
What is a virtual sample in Apex Fiz?
Without scanning in fabrics or yarns, designers can create virtual samples using the APEX FIZ software, which can be visualised as 3D garments. By selecting stitch structures from the stitch library, a fabric layout appears on the left side of the screen, whilst a 3D garment rendering of the fabric in a chosen silhouette appears on the right. Technical information is automatically generated and yarn visualisations can be inputted from ‘Yarn Bank’ to accurately portray fabric handle.
Patterns can be created from scratch, or the vast library of pre made garments can be utilised, inputting specific measurements where needed. Crucially, APEX FIZ software works to accurate stitch numbers, meaning simulations are accurate stitch for stitch- essential for realistic outcomes.
Shima Seiki were delighted to also announce their industry collaboration with Alvanon too. Alvanon’s database of 6000 virtual bodies will be accessible for download directly to APEX FIZ. This encourages diversity of body types within the design and fitting process, allowing virtual garments to be visualised in a whole variety of poses and body types.
SHIMANAVI: Shima Seiki’s new online training programmes
Shima Seiki also revealed their new online teaching courses launching alongside APEX FIZ in October 2020. Initially available in 3 languages (English, Chinese and Japanese), there are several new courses lead by specialist instructors and most crucially- these can be accessed anywhere. Designers can train remotely, enabling them to make the most of this software and in doing so, reduce waste effectively through learning to accurately sample virtually.
How can designers utilise these new offerings to encourage sustainable design?
An inclination for fast fashion brands to utilise this software to reduce their lead times even further is a concern. Case studies have shown reductions from 3 months to 2-3 weeks by using virtual sampling processes. Shima Seiki’s intention is to promote sustainability by reducing material waste during production, but if more clothes are made and contribute to fast fashion consumption, waste may be reduced in production but increased in landfill. Therefore, responsible use of this software by brands and designers dedicated to improving their sustainable processes is essential.
Innovative application of these tools could thrive within the contexts of whole garment technology and ‘slow design’. Although lead times speed up, development in responsible, traceable and sustainable design could receive more attention. With less time dedicated to amending miscommunications and re sampling prototypes, more time could be invested in studying garment life cycles, developing garment longevity and care for the whole lifecycle of the garment.
Developed in tandem with their machine capabilities, the ability to develop WHOLEGARMENT designs is also made ‘user friendly’ for designers in APEX FIZ. Utilising this minimal waste production method would be another sustainable step facilitated by these developments.
In reality, for designers with a textile focus, actual sampling would still often be necessary, but it could be introduced less frequently and at later stages. With confidence in the desired outcome being achieved, less material waste could indeed be a realistic outcome.
There is plenty of space for innovation within these new developments. As the Fashion Industry adapts to post-pandemic market demands and strives towards more sustainable futures, it will be interesting to see how Shima Seiki’s ‘Total Fashion System’ is utilised by designers now they can access it wherever they are in the world.
Further information
https://online-services.shimaseiki.com/en
About the author
Beth Ranson is a knitwear designer, textile researcher and lecturer in Textiles. As a skilled knitter, she designs and produces fabrics for a variety of design contexts. Motivated by problem solving in sustainable design contexts, Beth occupies the space between knitted textile design and sustainability theory: an interesting space to be. With a strong focus on the preservation of creativity in design, Beth believes that sustainability need not be perceived as a limitation in design. Inspired by her on going research into what ‘sustainable practice’ can mean, Beth takes note of academic theories within the realms of aspirational goals and applies this to the actual making process, working from ‘the bottom up’. She intervenes in current systems for textile product life cycles and seeks to inspire and facilitate educated and responsible change.
Business intelligence for the fibre, textiles and apparel industries: technologies, innovations, markets, investments, trade policy, sourcing, strategy...
Find out more