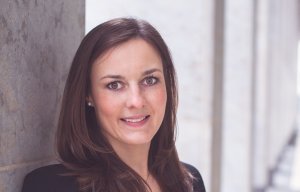
New Karl Mayer company to offer digital solutions
The company is working on collecting and bundling machine- and quality-relevant process data.
15th April 2019
Knitting Industry
|
Albstadt
Sebastian Mayer is in charge of corporate development at the circular knitting machine company, so taking digitisation forward at the family-owned firm is one of his core responsibilities. © Mayer & Cie.
The experts are agreed that every company, regardless of its size, must deal with the subject of digitisation and find its own approach to it. Mayer & Cie. (MCT), a leading international manufacturer of circular knitting machines, sees in smart solutions an opportunity to continue to be a step ahead of the competition. The company is working on collecting and bundling machine- and quality-relevant process data. At the same time, a continuous data flow must be ensured across all interfaces. Initial measures are already being implemented.
Sebastian Mayer, a member of the Mayer & Cie. management, is in charge of corporate development at the circular knitting machine company. Digitisation is an important part of his remit, but Mayer is reluctant to leave it at that. “There is no such thing as digitisation per se,” he said. “There are different areas in which it can be of relevance for us as an engineering company. They include, for example, digitisation of production and the value chain, better known as Industry 4.0, digitisation of the organisation and of collaboration, and digitisation of the product itself. Each angle has different challenges and benefits. Within this framework every company must decide for itself what makes sense and when.”
A key concern at Mayer & Cie. is to take a closer look at existing processes and see how they can be mapped more efficiently and at less expense. There is nothing new about this approach as such, Mr Mayer explains. Regularly undertaking a critical appraisal and improving existing processes has always been firmly embedded in Mayer & Cie.’s DNA. “We would otherwise not be where we are today,” he added.
Until now, Mayer & Cie. feels, the need for digitisation in manufacturing has not been as urgent as in other industries, especially the media. But that is no reason to take it easy, says Sebastian Mayer. Technical and mechanical leads are not infinite. He sees in digitisation the potential to continue to set Mayer & Cie. apart from the competition.
Mayer & Cie. has already taken the first step: identifying approaches that are meaningful and relevant for the company. They consist mainly of ensuring data quality and continuity on the basis of sustainable future-oriented technologies. Specifically, that means, for example, systematically collecting circular knitting machine data.
Data continuity and the seamless automated flow of collected data to its destination without perceptible interruptions play a special role. “The classic example of discontinuity is the Excel spreadsheet that one employee feeds with data he has collected from an existing database in order to send it to a colleague who then inputs it by hand into another system,” said Mr Mayer.
Mayer & Cie. has laid the technical groundwork for change by introducing a new ERP system. It is a basis for all other services that the company would like to provide. Sebastian Mayer describes it as the company’s “digital spinal cord,” the central hub for all data and information flows.
Mayer & Cie.’s next target is specific measures to improve customer satisfaction. They include ways to provide remote technical support, better known as Remote Services. “We are working inter alia on solutions that involve Mixed-Reality glasses,” explained Mr Mayer. “They enable us to see what the customer sees without the need for protracted explanations. Everyone who has ever described a technical problem over the telephone knows just how arduous that can be.” Using these glasses, customers can be shown remotely how to carry out regular maintenance work and even simple repairs. A Web shop is also about to be launched.
In future, all these measures will lead to a comprehensive customer portal where customers can access centrally anything they need to know about their machines and communicate with Mayer & Cie. or its representatives.
Business intelligence for the fibre, textiles and apparel industries: technologies, innovations, markets, investments, trade policy, sourcing, strategy...
Find out more