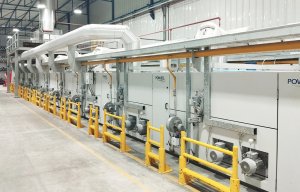
Third Brückner finishing line for Texfina
Leading fabric finishing machinery manufacturer Brückner, will show a novel direct coating system for knitted fabrics amongst its latest innovations at ITM 2009 in Istanbul in June. The company’s Opti-Coat coating unit is designed to coat functional fabrics and especially stretch fabrics. The market for functional textiles for sports and outdoor wear has grown considerably in recent years and breathable garments in particular have been in demand. These
7th May 2009
Knitting Industry
|
Leonberg, Germany
Leading fabric finishing machinery manufacturer Brückner, will show a novel direct coating system for knitted fabrics amongst its latest innovations at ITM 2009 in Istanbul in June. The company’s Opti-Coat coating unit is designed to coat functional fabrics and especially stretch fabrics.
The market for functional textiles for sports and outdoor wear has grown considerably in recent years and breathable garments in particular have been in demand. These fabrics are characteristically water-tight, windproof, breathable, thermoregulating, dirt-repellent, flame-resistant, UV resistant, and warming in cold weather and antimicrobial. It is against this backdrop that Bruckner and its partner for this development, Stork Prints, partnered in a project which has now come to fruition.
Coating fabrics have always in the past been the domain of woven or non-woven substrates but Bruckner’s new system aims to change that. Wovens and some nonwovens are characterized by their good dimensional stability, whereas knitted fabrics have comparatively poor dimensional stability properties.
Bruckner says: “We were willing to face to this challenge and together with Messrs. Stork Prints we have developed an innovative technology for the direct coating of elastic knitted fabric and applied for a patent.”
· Integration of a rotary printing screen in the entry zone of the stenter
· centring of the fabric in front of the introduction to the coating unit
· extremely short fabric path between the coating unit and the pin-on point at the stenter
· tension-controlled fabric transport of the elastic knitted fabric through the complete process of coating and drying
· selective width and length heat-setting of the fabric with a stenter with optionally available fabric support belt
· flexible foam processor by Stork Prints, which can be used also for paste processing
“This innovative technology opens completely new possibilities for coating and functionalising of elastic knitted fabric” Bruckner says, adding: “The rotary printing screen allows applying pastes as well as stabling and instable foams in a direct coating process”.
Business intelligence for the fibre, textiles and apparel industries: technologies, innovations, markets, investments, trade policy, sourcing, strategy...
Find out more