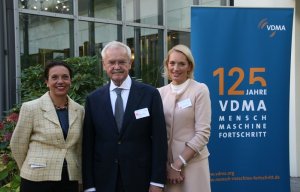
Regina Brückner elected new chairperson of VDMA
Viyellatex Ltd is making savings on utilities such as water, gas and electricity as well as savings in dye stuffs and chemicals, following the installation of a new Thies iMaster H2O dyeing range.
31st May 2012
Knitting Industry
|
Dhaka
Bangladesh’s Viyellatex Ltd has installed a Thies iMaster H2O as part of its growth strategy and is reporting substantial savings in water, electricity and gas, in addition to increased production rates. The installation was handled by Thies’s sales and service partner for Bangladesh, HOService, which is based in Dhaka.
Viyellatex, which was founded in 1996 as a knit apparel and textile manufacturing company, has in recent years evolved into a vertically integrated organisation where production begins with the import of raw cotton and proceeds through the processes of the processes of knitting, dyeing, washing, cutting, sewing and finishing.
A 100% export-oriented company, Viyellatex produces brand-name goods for clients that include Marks & Spencer, Hugo Boss, Calvin Klein, Puma, Timberland, Esprit, Tommy Hilfiger, and Hawes & Curtis.
“We have for some years now operated our own dye house, using a mix of Thies and Chinese-built equipment,” says Kazi Monjurul Islam, Viyellatex’s chief operating officer.
“The capacity was 30 tonnes per day, and as we are planning future growth in dyeing and garments, we decided to expand upon this.
“We looked very closely at the performance of our existing equipment, and at the specifications of the new iMaster H2O, and we concluded that the Thies iMaster H2O represented the new generation of dyeing machines.
“The new equipment was ordered from Germany late in 2011, we built a new extension to our factory to accommodate it, and our new dye house came into production early this year.”
The iMaster H2O have various capacities and been usually loaded to about 95% capacity.
Mr Monjurul says that the dyeing cycle varies according to the depth of the colour. “The light colours are of course taking less time than the deeper colours,” he says. “We work on the basis of an average of 3 to 4 batches per day.”
“The very low liquor ratio which is varying between 1:4 to 1:5 is providing us with cost-effective dyeing,” says Mr Monjurul. There is of course some tolerance, but the overall water consumption comes to 35-40 litres/kg of dyed fabric.”
“With the iMaster H2O our water, electricity and gas usage has decreased.”
“At the same time the fabric quality has increased due to the low shrinkage factor caused by the small degree of rope lifting. The very low nozzle pressure helps us to achieve the best quality fabric surface.”
Viyellatex’s dye house is working 24 hours a day, seven days a week.
Business intelligence for the fibre, textiles and apparel industries: technologies, innovations, markets, investments, trade policy, sourcing, strategy...
Find out more