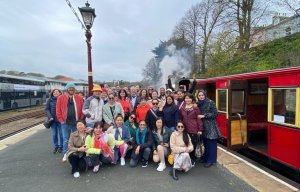
The Albion Knitting Company moves to the Isle of Man
Company aims to become the city’s first ever high-end fully-fashioned knitwear manufacturer that will cater to luxury brands and designers.
15th April 2015
Knitting Industry
|
London
A new state of the art fully-fashioned knitwear manufacturing facility has opened in the North London borough of Haringey, which is thought to be the first knitwear factory of any significant proportions to open in the capital since the 1940s.
The Albion Knitting Company Limited, which opened its doors just a couple of months ago, aims to take a step further however, and become the city’s first ever high-end fully-fashioned knitwear manufacturer that will cater to luxury brands and designers.
For those who don’t know, London is not a knitwear-manufacturing destination. It’s a celebrated centre of creativity and home to many world-renowned fashion designers and brands, but it is definitely not a knitwear-manufacturing centre.
Normally, if you were going to set up a knitwear manufacturing operation in the UK, the obvious thing to do would be to head to Leicestershire, Nottinghamshire or Derbyshire where a small industry still remains where once hundreds of quality manufacturers existed. Or you might go to the Scottish Borders where knitwear manufacturers are steeped in the traditions of high quality fine woollens and cashmere. The UK still has knitwear-manufacturing skills.
Albion has chosen not to follow the traditional path though and has decided to do things differently and ‘take the road less travelled.’
The project is the brainchild of two courageous entrepreneurs Chris Murphy and Jamie O’Neill- Murphy handles sales and marketing and O’Neill takes care of production. Both are former employees of the now defunct 140-year-old Dawson International, which once owned a number of iconic luxury knitwear brands including Pringle and Barrie Knitwear, and was part of the first wave of British manufacturers to move its production to China some years ago.
Murphy, who is well connected with the leading fashion houses in London and elsewhere, studied Chinese in London and was a graduate trainee at Dawson. O’Neill joined one of Dawson’s Scottish companies as a teenage apprentice before winning a promotion to help to set up a factory in China. The two gained considerable experience manufacturing in the UK and then spent a number of years working in China.
Now the two entrepreneurs have come back home and whereas before, the quest was to take British know-how offshore in search of cheap labour, this time the pair are bringing Chinese know how back to the UK to help set up the new production unit and train local labour to make £250 sweaters.
Yes, Albion is bringing in key skilled labour from China to help train local unskilled labour in London.
According to a recent article about the entrepreneurs in The Times, the decision was down, in part, to a simple yearning for home after years away, but there was also a feeling that the days of relatively easy pickings in the Far East were over.
Chris Murphy told the newspaper: “The first thing you need in business is timing, and it had to be time to reshore to Britain because buyers of luxury brands — especially the Chinese — don’t want ‘made in China’ on the label.” According to Murphy they want ‘made in England’ or ‘made in Italy’ on the label.
“Also, the English knitting industry is at such a low ebb — apart from John Smedley, we don’t have any high-end knitwear in England — that there has to be an opportunity,” Murphy said.
Murphy went on to tell Knitting Industry: "There was European funding available to go to economically depressed areas but I thought it was important to set up a new benchmark and demonstrate that a modern, skilled and flexible flat knitter could thrive in the heart of London close to our customers."
From the outside, The Albion Knitting Company looks like a typical factory in a typical industrial estate that you can find in any British town or city. But once inside the factory a story starts to unfold that reveals a very daring project planned and executed by forward thinking management with significant industry experience.
Chris Murphy founded and still manages a high-end fashion forward knitwear manufacturing business in Beijing, China called Alphatex, which manufactures for some of the world’s leading luxury brands including Givenchy, Nicole Farhi, Jaeger, Chloé and Marc by Marc Jacobs.
Albion is targeting the higher echelons of this type of clientele using European yarns, whereas Alphatex uses Chinese yarns to meet the needs of high-end fashion companies with higher volumes.
The company, which is currently running at about 50% of capacity whilst training takes place, aims to produce in the region of 50,000 pieces per year or 1000 pieces per week. Minimum order sizes for it complex knitwear are as low as 120 pieces per style.
The Albion Knitting Company is noticeably different to most knitwear factories and clearly significant effort and expenditure has gone in to making it attractive to the company’s designer clientele. The route from the factory floor to the showroom and production office for example is via an extravagantly sculpted metal staircase where every step incorporates an up-cycled needle bed from a redundant hand flat knitting machine.
The Times described the factory’s £200,000 fit out costs as “part of its policy of not running a sweatshop behind a showroom for the fashion-house clients. Instead, it’s the manufacturing equivalent of the open kitchen at a three-star restaurant cooking steak from an organic farm in Leicestershire.”
So far Albion has taken on three apprentices via a Fashion Capital initiative. O’Neill says he needs three more for the linking department.
The idea is to train staff to a particular level and then introduce piece rates. Staff had been working days only but a night shift has just been introduced to meet production demands.
On the subject of recruitment O’Neill says: “There are lots of people with wovens skills around London but no knitted fabrics experience – especially on the make-up side.”
In the factory I meet Amanda, one of the key supervisory staff drafted in from Alphatex in Beijing, who is teaching locally recruited sewers to link knitwear. Mio, a Japanese knitwear designer who has been working in London for a number of years, is ably assisting her. At a near by sewing machine Elena, who used to make woven garments for Dolce & Gabbana in Milan is applying an intricate trim to a garment.
This is a young, multi cultural, seemingly happy and enthusiastic work force, which Jamie O’Neill plans to shape into a flexible multi-skilled manufacturing team, avoiding the rigid hierarchical systems of traditional knitwear manufacturing. The company says it pays above the London Living Wage.
As well as recruiting local labour on apprenticeship schemes Albion has also gone to the Universities to recruit talented graduates, which it is putting into key supervisory positions. The knitting department alone has four graduates.
As we walk towards the knitting area to view the new company’s new knitting machines, Jamie O’Neill shouts out instructions in Mandarin to Eddie, an experienced programmer from Beijing. O’Neill is currently trying to recruit another technician and will be sending some of his graduates to Germany for training.
Albion has made a significant investment in the very latest flat knitting technology from German machine builder H. Stoll GmbH & Co KG, one of the world’s renowned knitting machine manufacturers. When I visited the company there were fifteen Stoll machines running including three of the very latest Stoll CMS ADF-3 models. The plant consists of:
3 – Stoll CMS ADF-3 in 7.2 gauge
2 – Stoll CMS530HP in 16 gauge
6 – Stoll CMS530HP in 7.2 gauge
2 – Stoll CMS530HP in 2,5.2 gauge
2 – Stoll CMS502 in 16 gauge
Stoll aims to set new standards in the knitting world with its ADF-3 technology. Due to its unique yarn carrier technology, the Stoll CMS ADF-3 knitting machine offers many features for innovative knitting when it comes to structural technique and colour combinations.
Jamie O’Neill is keen to emphasise the important part that knitting machine builder Stoll and its UK distributor Stoll GB have played in the project: “None of this would have been possible without Stoll’s input. The project just would not have happened,” O’Neill said. “We know we can call on the services of Stoll GB if we need extra product development capacity. They have very good sampling capability.”
We spoke to Joerg Hartmann, Head of Fashion & Technology at Stoll, who has played a pivotal role in the project.
“We met with Chris and Jamie at Albion a long time ago at an expo in Paris. In this context we spoke about Stoll's positive experience with sampling services in New York City and other places. In this concern we spoke about fashion hubs and the potential of such endeavours. We also spoke about the existing infrastructure in big fashion capitals when it comes to sample and small lot making,” Hartmann said.
“NYC has the Garment district, Paris has the Sentier and so on. It was very obvious to me that London would be an ideal place for such services as most of the renowned design colleges are clustered in London. So many well-educated and highly creative designers graduate yearly from there. Many of them call to life their own labels afterwards and desperately look for sampling support and production of small lots,” he continued.
“History tells us that some of them have the potential to grow big and become good clients of knitting mills. Stoll was always a major supporter of young talents and has proved with its own endeavours in Leicester and New York how much the market responds to it. We promoted this idea already for a long time among our clients and Chris and Jamie were the ones who understood the potential and were committed to take the risk.”
“This is entrepreneurship at its finest. I'm glad that the young and the established talents in London have a place now to go,” Hartmann concluded.
There is clearly a very good working relationship with Stoll here. Chris Murphy is currently working with Joerg Hartmann at Stoll to put on a workshop in London for some of his designer contacts in order to showcase Stoll’s ADF knitting technology.
We visit the company’s showroom where we look at a wide range of beautifully made knitwear, some made in Beijing and some made in the new London factory.
This really is high-end knitwear, the sort of thing you might expect to find at the top Italian manufacturers. Its not just good finishing in nice yarns with linked necks. This is very complex knitwear where all the seams are linked, where knit is combined with woven and zips, plackets, pockets and all manner of trims are exquisitely applied.
The Albion Knitting Company project is one of the boldest projects we have seen in this industry for a very long time. There are others, but this is extra special because of where it is located and because the company has set its sights so high in terms of the quality standards it wants to achieve. In the words of Jamie O’Neill, life over the next few years for the two intrepid entrepreneurs will be “scary, daunting and very exciting all at the same time.”
Business intelligence for the fibre, textiles and apparel industries: technologies, innovations, markets, investments, trade policy, sourcing, strategy...
Find out more