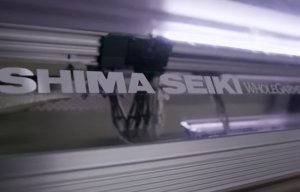
High-end knitwear, made in California
This is the second in a series of articles that sets out to investigate the impact of the technology on the knitwear industry and its leading exponents.
22nd June 2015
Knitting Industry
|
Montefano (MC)
This year is the 20th anniversary of the launch of Shima Seiki’s WHOLEGARMENT knitting, a revolutionary flat knitting technology that allows the production of ‘seam-free’ knitwear. This is the second in a series of articles that sets out to investigate the impact of the technology on the knitwear industry and its leading exponents.
Last month I visited the province of Macerata in Italy’s sunny Marche region to meet some of the country’s leading knitwear producers who are using Shima Seiki WHOLEGARMENT knitting technology to produce top quality seam-free knitwear.
Marche is one of the 20 regions of Italy and is located in the Central area of the country, bordered by Emilia-Romagna and the republic of San Marino to the north and the Adriatic Sea to the east. Except for river valleys and the narrow coastal strip, the land is hilly and it is in these beautiful hills that some of the finest knitwear producers in Italy can be found.
Take for example Sabry Maglieria, a family owned knitwear manufacturer based in the small town of Montefano about thirteen kilometres north of the town of Macerata, the county town of the province of Macerata.
Sabry’s history spans 45 years from 1970 to the present day and the ‘Sabry’ in Sabry Maglieria comes from the name Sabrina Storani, daughter of founders Nello and Antonietta Storani, the company’s current Direttore Generale or CEO. The company employs around 60 people and makes top quality knitwear for the luxury market including some of the top French and Italian fashion houses.
In the 1980s, as Sabry’s customer base expanded and its turnover grew, the Storani’s small original workshop became a small factory and in 1994 the company moved to new headquarters with improved and expanded workspace. Today’s stylish and modern factory covers more than 2000 square metres.
The company makes a wide range of fully-fashioned and WHOLEGARMENT knitwear for women, men and children from the very best cashmere, viscose, silk, wool, linen, cotton and luxury blended yarns from Italy’s finest spinners including Zegna Baruffa, Cariaggi, Botto Poala, and Line More.
Sabry makes thousands of samples every year, many of which are paid for by customers, and knits on Shima Seiki machines in the full range of gauges from 3 to 18. Family member Maurizio Storani runs the knitting department and one of the company’s specialties is intarsia. It has ten Shima Seiki high-speed intarsia machines in 18 gauge for this purpose.
Sabry's recent purchases, following a visit to Shima Seiki in Wakayama, Japan, include the MACH2SIR for intarsia and Shima’s SRY123LP ‘inlay’ machine for weft insertion flat knits which have some of the properties of wovens.
Sabry’s plant is a varied one to cater for the diverse range of knitwear the company’s top end customers require. It consists of a mix of SES122CS, SES122S, SES124S, SSG122SV models for fully-fashioned production, NEW SES123SI, MACH2 SIG, MACH2 SIR, SIR 123SC and SIG123SV models for fully fashioned and Intarsia production and a range of WHOLEGARMENT knitting machines including NEW SES183SW, SWG-V and SWG-X173 models. The fully-fashioned machines cover 3-12 gauge, the intarsia group covers 14-18 gauges and the WHOLEGARMENT group covers gauges 7, 12 and 15.
Sabry Maglieria really is a dynamic knitter, which has the capability to make a wide range of knitwear styles but I’m interested to know why the company has now started to invest in WHOLEGARMENT knitting. I put the question to Sabrina Storani.
“We want to be prepared for our customers and so we want to have the very latest technology in a range of gauges. We want to be able to meet all of our customers’ requirements and we want to be able to propose new solutions to our customers. We need to propose new things in order to work,” she said.
Sabry first invested in ‘capo completo’ manufacturing via WHOLEGARMENT technology in 2006. “WHOLEGARMENT is a very important technology. We propose complex garments to our customers and it is obligatory to propose something new with luxury customers. We cannot wait for our customers to ask for something we do not have. We must be proactive’” Sabrina Storani adds.
Sabry makes around 90,000 knitted pieces per year or approximately 1800-2000 pieces per week. Currently just over 10% of its output is from WHOLEGARMENT machines but according to Sabrina Storani this will grow and the company will invest further in the technology. In fact, when I visited, the company was preparing to visit the Shima Seiki Italia Open House show in Milan the following week where Shima’s latest WHOLEGARMENT offering, the high speed MACH2XS with moveable spring-loaded sinkers was to go on show.
I asked Sabrina what the benefits of investing in WHOLEGARMENT technology have been for Sabry.
“One of the benefits is that we can reduce the number of people we employ. But it’s not just about labour,” she offers, adding that: “For women WHOLEGARMENT knitwear offers the perfect fit. Because there are no seams it is very comfortable and it is form fitting which is a real benefit.”
“It is important to offer upgrades to our customers. We will not invest just to save labour. There has to be more than that,” she adds.
However, the shortage of skilled labour that Shima Seiki cites as one of the foremost drivers for WHOLEGARMENT knitting become apparent as we continue our conversation.
Sabrina Storani has strong views about the training of labour in Italy’s knitwear industry. “It is difficult to find people who want to do manual labour these days. Young people don’t want to enter our industry to work and so something must change,” she says.
Recruiting skilled knitting technicians is another issue for Sabry as it expands its production capacity. The company already has five Shima Seiki programmers but Sabrina calculates that she needs two more.
I asked if the company had needed much in the way of support from Shima Seiki when it started to build WHOLEGARMENT capacity. “Of course we did, especially in the beginning and Shima was well prepared. We always need Shima with us as a partner,” she said.
We discuss taking textile technology students or design graduates from universities and training them to programme Shima Seiki machines, but the pressing issue for Sabrina seems to be the up-skilling of skilled knitting technicians.
“We have requested a training school for our staff from Shima Seiki. This is currently under discussion and I know that Shima supports this.”
In fact, the latest word is that Shima Seiki Italia plans to open such a training school for its customers later this year.
I asked if she could command a better price for WHOLEGARMENT knitwear than for say fully-fashioned knitwear. “Sometimes yes, sometimes no,’” she says.
“Generally rich patterns or styles command higher prices with customers. Although, price does depend on the investment in the machinery required to produce the garment.”
When I asked Sabrina whether customers understand the benefits of WHOLEGARMENT manufacturing she says that both her customers and their customers do understand the benefits but to some extent it depends on the particular sweater design.
Design inspiration for Sabry seam free knitwear comes from both customers and from in-house design capability. Designs are usually initiated by customers and then jointly developed. So for example if a customer is looking for a cable pattern look but is not exactly sure what they want, Sabry develops a range of swatches for evaluation and further development.
Investing in WHOLEGARMENT knitting has had additional benefits for the company. “We have gained some new customers since we invested in WHOLEGARMENT knitting. Some customers actually come looking for WHOLEGARMENT development and production. Also, some of our existing customers did not know about the technology and since we introduced it to them they have been placing orders.”
“The secret with textiles is to keep proposing something new to your customers,” she says.
I asked Sabrina if she was concerned that the luxury brands were benefitting from her company’s skills and know-how without her company gaining any of the recognition it deserves. She retorts: “In a particular sweater there may not be my name, but there is my mind.”
Further reading
New Twins set to become leading player in theatre of WHOLEGARMENT knitwear
MIND Srl – A WHOLEGARMENT Success Story from Italy’s Veneto Region
WHOLEGARMENT knitting technology helps set New Esse Maglieria apart from its competitors
La Trama: A WHOLEGARMENT Powerhouse In Italy’s Marche Region
Business intelligence for the fibre, textiles and apparel industries: technologies, innovations, markets, investments, trade policy, sourcing, strategy...
Find out more