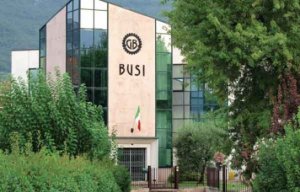
Busi participates in Italy-Mongolia project
This is one of a series of articles that investigates the impact of Shima Seiki's WHOLEGARMENT technology on Italy’s knitwear industry and its leading advocates.
14th October 2015
Knitting Industry
|
Albizzate (VA)
This year is the 20th anniversary of the launch of Shima Seiki’s WHOLEGARMENT knitting, a revolutionary flat knitting technology that allows the production of ‘seam-free’ knitwear. This is one of a series of articles that sets out to investigate the impact of the technology on Italy’s knitwear industry and its leading advocates.
In July this year I travelled to Albizzate, a small town and community located in Varese, one of twelve provinces in the Lombardy region of northern Italy. It is the most north westerly province in the region and its northern border forms the international boundary with Switzerland. Lake Maggiore is to the west and the city of Milan lies to the south.
I am here to visit the small privately owned knitwear manufacturer Martignoni Paola, which is owned by Mario Puricelli and his partner. The company has been going since the 1970s and has just 10 employees making 2000 pieces per week of very high quality knitwear for some of Italy’s top brands.
Martignoni Paola’s knitting plant of 35 machines is made up of a wide range of Shima Seiki models in almost every available gauge - 3,5,7,12,14,18 and 21 gauges. Models include Shima Seiki SES122FF, SES122RT, SSG, NSSG, SIG, FIRST124, MACH2X and SRY183LP. The company also has a number of Shima Seiki design systems including SDS ONE APEX3.
Martignoni Paola is what the Italian knitwear industry calls a ‘sub-worker’, a company which generally manufactures knitwear under contract to a bigger company which in turn supplies the leading brands and fashion houses. But sub-worker is not a completely accurate description for a company like Martignoni Paola as it makes exquisite products and sometimes supplies the top brands directly too.
This factory is all about top quality and it supplies the legendary Missoni and Gucci brands directly. Other end customers include the prestigious Ermenegildo Zegna and ETRO. Only the best raw materials are used including yarns from the top Italian spinners such as Zegna Baruffa and Botto Poala.
Recently, the company has embarked on a couple of new technology upgrade projects including one involving Shima Seiki’s MACH2X high speed four needlebed WHOLEGARMENT technology. The first tranche of investment is in Shima’s MACH2X153 18L model, which is busy producing seam free knitwear during my visit.
I asked Mario Puricelli why he had recently invested in Shima Seiki’s WHOLEGARMENT technology. Mario fully understands the cost savings benefits that the technology offers, but for him it is more about having something new to offer his customers.
“Our customers understand the benefits,” he explains. “When we present to our customers it is imperative to have our ‘own range’ in there. It is vital to have something new to show the customers. It is also important to be an all-rounder so that you can tell the customer you can do everything for them.”
“Having a wide range of gauges is also essential in that respect,” Mario adds.
“Being able to knit the most difficult garments is also critical. Everyone else can make fully fashioned garments. WHOLEGARMENT is significant. It is something we need to have - a ‘must have’ technology,” he says.
Martignoni Paola started working with 18 gauge WHOLEGARMENT technology, the finest and most difficult gauge of machine to produce on. “We started with the most difficult gauge because fewer companies have 18 gauge WHOLEGARMENT machines and there is very strong market demand for the product. We also need to have the latest technologies – and 18 gauge WHOLEGARMENT falls in to that category,” Mario explains. He also adds that the company can command better prices for such garments.
MACH2X is a recent addition to Shima Seiki's line of WHOLEGARMENT specialty machines that features 4 needle beds and the company’s original SlideNeedle.
It can knit beautifully shaped, high-quality WHOLEGARMENT products which conform to the body for improved comfort and a more elegant silhouette. As the ‘MACH’ name suggests, speed and productivity are key, with MACH2X achieving a maximum knitting speed of 1.6 metres per second.
The R2CARRIAGE System additionally permits quicker carriage returns for higher efficiency per knitted course. Split Stitch technique also allows efficient knitting by eliminating empty courses.
New to the line-up is 18L gauge capability whereby a special large-hook version of the SlideNeedle is used for knitting 15 gauge fabrics at 18-gauge needle pitch for very high productivity when knitting ultrafine gauge garments. The tighter needle pitch also allows for a tighter fabric especially for ribs, contributing to higher-quality WHOLEGARMENT items.
According to Shima Seiki, dramatic improvements in both quality and productivity make the new MACH2X the ideal machine for high-quality ultrafine gauge WHOLEGARMENT production.
I ask Mario about the technical support the company needs for its WHOLEGARMENT technology and he tells me that they manage quite well on their own with their 4 technicians. The factory produces 2 or 3 new samples every day and works 24 hours per day, six and a half days per week.
He explains that there is increasing demand from some of his customers but he has no room to expand. The plan here instead is to upgrade the company’s technology which is exactly what it is doing with WHOLEGARMENT.
Martignoni Paola’s designs are provided by its customers and it prefers to work in this way. I ask if he has gained new customers by investing in WHOLEGARMENT, but Mario tells me the plan is to work with existing customers and to offer them something new. He is currently working with two of his customers on WHOLEGARMENT projects.
Another ‘must have’ technology that Martignoni Paola has recently invested in is Shima Seiki’s SRY technology for so called ‘knit-weave’ fabrics – knitted fabrics which look like and have some of the properties of woven fabrics, which Shima Seiki calls ‘KNEAVE.’ The company recently took delivery of its first SRY183LP machine in 14 gauge and is busy producing samples for some of Italy’s leading fashion houses.
Shima Seiki's new SRY123LP and SRY183LP computerized flat knitting machines inherit its highly advanced mechatronics know-how based on the company's unique experience with four-bed knitting, beginning with SES122RT, and continuing with SWG-FIRST and MACH2X.
Two loop presser beds improve on the stitch presser by controlling press down of individual loops. This, Shima says, presents unprecedented capability in knitwear, especially with flechage and inlay patterns.
New fabrics with woven effects offer great opportunities in expanding into other markets. Specialty yarns such as metallic and monofilament yarns can be knit as well, opening new doors to areas other than fashion.
A high level of productivity typical of Shima Seiki is carried over, with a maximum knitting speed of 1.4 metres per second combined with quick carriage returns realized with the proven R2CARRIAGE system. Shima Seiki's original DSCS Digital Stitch Control System, yarn gripper and cutter, and takedown comb all contribute to high quality and productivity as well.
I’m shown a range of samples the company has produced on the SRY183LP and they are fabulous. There’s a very attractive padded gilet with a solid colour on one side and a jacquard pattern on the other side. Mario, understandably will not say whom it has been made for. He is very discreet, controlling what can be photographed in his factory and what is out of bounds. He does have some of the world’s top designers as his clients after all.
I ask Mario about the market for knitwear produced on the SRY and he elaborates: “SRY has very good possibilities for us. It offers something new and is more with the market.”
We return to the MACH2X machine to observe a technician making machine adjustments to a sample for one of the company’s top customers. Mario says that he can see an interesting future for WHOLEGARMENT technology in his company and like the SRY ‘knit-weave’ technology, it is a must ‘have technology’ in his knitwear manufacturing portfolio.
Many of Italy’s, and in fact the world’s leading brands and fashion houses, now carry WHOLEGARMENT knitwear in their collections. It seems that the technology is now becoming established as a ‘must have’ for them, as well as for the WHOLEGARMENT producers.
New Twins set to become leading player in theatre of WHOLEGARMENT knitwear
MIND Srl – A WHOLEGARMENT Success Story from Italy’s Veneto Region
WHOLEGARMENT knitting technology helps set New Esse Maglieria apart from its competitors
WHOLEGARMENT investment cuts labour costs and creates new opportunities for Sabry Maglieria
La Trama: A WHOLEGARMENT Powerhouse In Italy’s Marche Region
Business intelligence for the fibre, textiles and apparel industries: technologies, innovations, markets, investments, trade policy, sourcing, strategy...
Find out more