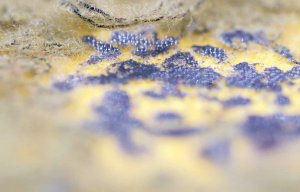
Disruption and recycling at SPINEXPO
Editor’s View
Looop is a system for recycling knitwear combining proven textile technologies, including Shima Seiki’s WHOLEGARMENT knitting technology.
12th October 2020
Billy Hunter
|
Stockholm, Sweden
Fashion retail giant H&M has announced the launch of its Looop garment-to-garment recycling system at one of its Drottninggatan stores in Stockholm. Looop is a system for recycling knitwear and combines a number of proven textile technologies, including Shima Seiki’s benchmark MACH2XS WHOLEGARMENT knitting technology, to demonstrate to retail customers how they can recycle their used sweaters. Looop opens to the Swedish public in the capital today.
“We are thrilled to soon offer customers in Sweden the possibility to transform unwanted garments into new fashion favourites with the help from our new garment-to-garment recycling system Looop. We are committed to closing the loop on fashion and this machine visualizes to customers that old textiles hold a value and should never go to waste,” H&M said in a press statement on Thursday.
“Looop opens to the public in one of our Drottninggatan stores in Stockholm on October 12. This is the first time this garment-to-garment recycling system is shown in store by a fashion retailer and H&M is proud to soon offer customers the opportunity to watch this container-sized machine recycle their old textiles into something new. This is part of a bigger plan - our ambition is to become fully circular and climate positive and we are working with many exciting projects to reach this goal. We must innovate materials and processes while inspiring customers to keep their garments in use for as long as possible,” H&M added.
Looop: Garment-to-garment recycling system
The ‘container sized machine’ H&M refers to, actually comprises of a number of textile machines which clean, shred, filter, card, draw, spin, twist and knit to deconstruct unwanted knitwear items and produce new seam free WHOLEGARMENT knitwear, which requires no sewing. The technologies are mainly known technologies used in textiles recycling, fibre processing and spinning, with Shima’s ‘seam free’ knitting technology representing the state-of-the-art in knitted garment manufacture.
Here’s a run-through of the eight steps that take place to turn old garments into new ones. First, your old garment is sprayed with ozone to remove any microorganisms. The garment is then shredded down into small ‘chunks’ of fabric fibres and the shredded chunks are filtered to remove dirt - and additional virgin material is added for strength. The clean fibre mix is then straightened into a fibre web and then pulled into slivers by carding and then multiple fibre slivers are combined to create even stronger, thicker slivers. The thick fibre slivers are then spun to create a single yarn and single yarns are doubled and twisted together to increase their strength. The yarn is then knitted into a new, ready-to-wear design.
Towards a sustainable fashion industry
“H&M wants to lead the change towards a sustainable fashion industry,” the leading retailer, known for its green initiatives, said. “In 2013 we became the first fashion retailer with a global garment collecting program. Now, we are taking the next step with our garment-to-garment recycling system Looop. For 100 Swedish kronor, members of our loyalty club can use Looop to transform their old garment into a new favourite. For non-members the fee is 150 Swedish kronor. All proceeds go to projects related to research on materials. By 2030 we aim for all our materials to be either recycled or sourced in a more sustainable way, a figure that for 2019 was at 57%,” H&M explained.
“We are constantly exploring new technology and innovations to help transform the fashion industry as we are working to reduce the dependency on virgin resources. Getting customers on board is key to achieve real change and we are so excited to see what Looop will inspire,” said Pascal Brun, Head of Sustainability at H&M.
Laboratory scale: Garment-to-Garment Recycle System (G2G)
Installing textile machinery in retail environments to draw the public’s attention is not new. Over the years we have seen a number of ‘factory boutique’ concepts rolled out in leading department stores. Flat knitting machine builders have partnered with both retailers and knitwear manufacturers to help get new concepts across to the fashion buying public – think Stoll and UNMADE in London’s Selfridges department store, and Shima Seiki with Japanese retailer UNIQLO, for example.
H&M’s Looop project is about ‘getting customers onboard’ to help it achieve ‘real change’ in its sustainability goals. However, it takes skilled textiles people to set up and run something like Looop and programming a Shima Seiki WHOLEGARMENT knitting machine, for example requires the services a highly skilled technician. So, there is a bit more to the project than setting up some machines in a store. H&M’s Looop system is very interesting and if we dig deeper, we find out that this is actually far more than just a concept - it’s actually the tip of a growing technological recycling iceberg.
The technology behind Looop has been developed by The Hong Kong Research Institute of Textiles and Apparel (HKRITA) in collaboration with the non-profit H&M Foundation. HKRITA will license the technology widely to help the entire industry become more circular, H&M says. This is important, because to create real change, all brands need access to technologies like Looop, the company adds.
HKRITA’s Garment-to-Garment Recycle System (G2G) is described as a mini-scale garment-to-garment production line that recycles post-consumer garments so that they become clean and useful. It involves integral and closed-loop textile recycling processes - from sanitising a garment, removing hard trims, cutting fabric into smaller pieces, opening and mixing fibre, carding, spinning, through to garment knitting. The system is viable as a pop-up retail concept and presents an exciting new approach to inspiring a positive approach to garment recycling among consumers and industry players alike, HKRITA says.
This video shows how the RED DOT award winning G2G system works. The environmentally friendly system is housed in a sound proofed standard 40-foot container, so that it can be integrated into community spaces such as shopping malls, without disturbing the public or other businesses…
Industrial scale: The Billie Upcycling Factory
Taking garment-to-garment recycling to industrial scale is Hong Kong based yarn spinner Novetex Textiles Limited. Novetex’ The Billie System is designed to provide an innovative way for brands and companies looking to revive excess inventory, unused raw materials, or textile waste.
While most recycling processes require high volumes of water and chemicals to make useable yarns, Novetex explains, The Billie System combines new and existing technologies to create a waterless solution for recycling textile waste, lowering harmful effects to the environment. This mechanical recycling system does not consume water or produce chemical waste.
Developed by Novetex, the patented system is almost entirely automated, thereby reducing the high labour costs associated with textile recycling. The machines can process up to three tonnes of recycled fibres per day, which can be blended with virgin materials to produce yarn for various products and garments in its Zhuhai facilities.
The Billie System comprises six key stages:
Step 1: Textile waste sanitisation. Garments are purified via an ozone sanitisation system. The ozone is produced onsite, then disposed as oxygen into the air.
Step 2: Hardware Removal. Non-fibre objects and trims from the clothing are removed manually.
Step 3: Automatic colour sorting. Trimmed fabrics are sent to the camera to be sorted into nine colour ranges by reading colour reflections from the swatches.
Step 4: Fibre processing. The colour-sorted swatches are transferred automatically by the Automated Guide Vehicle (AGV) into Novetex’ mechanical recycling process, which breaks down the fabrics into fibres.
Step 5: UV light sanitisation. The fibres go through two stages of UV light sanitisation.
Step 6: Sliver processing. The 100% recycled fibres are processed into slivers.
On completion of the ‘6 Steps’, Novetex’ recycled slivers are then ready to be spun into yarns which will then be further processed to create new fabrics and garments.
The Billie System has been recognised in numerous innovation awards globally and has earned a Gold Medal in the International Exhibition of Inventions of Geneva and a Bronze prize in the 2019 Hong Kong Green Innovations Awards (HKGIA).
Established in 1976 and part of the Novel Group, Novetex Textiles Limited is recognised as a leader and pioneer in the textile industry. Founded by renowned Hong Kong entrepreneur and textile industry pioneer, Mr. Kuang Piu Chao, the Hong Kong-based company has over 500 employees and extensive operations in multiple cities across China and Asia. Its clients include high-profile global brands. The group is currently led by Chairman and third-generation family member, Ms. Ronna Chao.
Treating all clothes as a resource
The global textiles and apparel industries have already begun to scale-up garment recycling to an industrial level. Last week, German company imat-uve announced it is working with a German-Dutch consortium on an industrial solution for the recycling of old clothes made from mixed fibres. The recycled yarns and woven fabrics made from them, are primarily intended for use in the automotive industry. In another announcement Finnish innovator Spinnova, known for having developed breakthrough technology for making textile fibre from wood and waste, without harmful chemicals, said it is partnering with Danish company Bestseller to incorporate its fibres into Bestsellers leading clothing brands.
It will be interesting to see how Looop is received by the fashion buying public and whether H&M rolls it out to more international stores – at the moment the company has declined to comment on this.
“The launch of Looop isn’t just a glimpse of fashion’s future. It’s a reminder to treat all clothes as a resource. Nothing’s too tattered or torn to be recycled — and no clothes should ever end up in the trash. Recycling is also super-important for circular fashion to work. Unless people bring their old garments back into the system, there’d be no clothes to make new ones out of,” says Pascal Brun, Head of Sustainability at H&M.
“At H&M, we’ve had a global garment collecting programme since 2013. You can recycle any clothes or textiles from any brand in any of our stores. With Looop, we’re taking the next step. It’s the start of a recycling revolution, and we hope you’ll join us.”
The Hong Kong Research Institute of Textiles and Apparel (HKRITA)
Business intelligence for the fibre, textiles and apparel industries: technologies, innovations, markets, investments, trade policy, sourcing, strategy...
Find out more