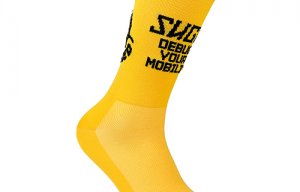
Kingly introduces sustainable performance socks
Rob Armour, CEO of Kingly Ltd., a socks manufacturer-based Sofia, Bulgaria, on his company’s approach to responsible production.
20th September 2022
Knitting Industry
|
Sofia, Bulgaria
As we become more aware of these catastrophic negative impacts, we all have to look for more ways to reduce pollution, minimise carbon footprints and cut the waste this sector produces. Impossible? Not at all. Competitively priced fashion does not have to mean poor quality or irresponsible methods of production.
We’ve already started - Kingly’s socks are made in a zero-waste knitting facility.
Production produces waste
During the manufacture of socks, small factory offcuts are produced. They’re a mixture of cotton, nylon, Lycra, elastane, and materials like polyester, polypropylene, and other fibres.
It is impossible for these offcuts to be recycled as there is no way one can separate the different fibres. For this reason, they would normally go to landfill.
Offcut waste is now retained and re-used
However, based on our commitment to a better, cleaner environment, and in line with our ISO 14001 Environmental Policy, at Kingly, waste fibres are now retained. The leftover fibres find a new life as stuffing for printed pillowcases, furniture, and so on. This is upcycling - taking something already in existence and transferring it into something of a higher value. Finding a second life is a lovely thing!
And in fact, this is not new to Kingly. It’s directly inspired by the Promotional Gift Award we received in 2020 for our upcycled socks in compostable bags. The socks were made from fibres mechanically recovered from recycled clothing, and the bags were made of potato starch. Environmental responsibility informs everything we do.
Eliminate waste, re-use or re-purpose
Kingly’s commitment to Zero-waste promotes a more focused way of producing and living. We have adopted this approach to eliminate textile waste in every aspect of production. We reduce the environmental impact of our processes and products in ways that have genuine meaning and provoke real change.
There are other elements that we consider too. For our facility to call itself truly zero waste, we:
- Factor in longevity when designing and knitting socks, ensuring they will last as long as possible for the wearer
- Use eco-friendly cleaner yarns for socks manufacturing, many of which are certified by the Global Recycle Standard (GRS)
- Use GOTS certified machine oil in our socks knitting machines
-Yarn bobbins are made of card; these are recycled responsibly
Delivering against the Global Organic Textile Standard (GOTS)
Our organic yarns need to meet the exacting criteria for the GOTS. For a textile to call itself organic cotton, production must have been without any chemical pesticides, GMO seeds, or artificial fertilizers. There are further requirements in terms of employment conditions and production methods including the use of water. Achieving the combination is a challenge.
We are delighted, then, that we have been approved for GOTS certification, one of only 52 socks manufacturers worldwide to meet the standards. On top of that, our GOTS-certified cotton socks have been awarded the 2022 Promotional Gift Award. You can read more about these stories on our website.
Our responsibility is social too
For us, the social element is as important as the rest of the processes involved. We are Sedex Pillar 4 Approved which means our working practices, and those in our supply chains, are assessed as to working conditions and meet demanding minimum criteria.
For Kingly, it’s not just about eliminating waste – it’s also about the people behind the company. Values are important.
Our machinery also runs on a central vacuum system, which reduces the amount of kW used and thus drops the electrical bill. Noise is reduced, which is a direct benefit for our socks technicians. Kingly operates a plant of socks knitting machines built and supplied by Italian company Busi Giovanni.
Setting an industry benchmark
Kingly’s Zero Waste Facility is a benchmark that other manufacturers should aim to match. Crucially, we have been able to introduce these changes and meet these standards and remain profitable. Our initiatives have a positive effect on making sustainability achievable in an industry notorious for its waste. If we can do it, others can too.
Business intelligence for the fibre, textiles and apparel industries: technologies, innovations, markets, investments, trade policy, sourcing, strategy...
Find out more