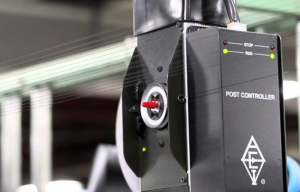
Karl Mayer acquires YTC yarn tensioner technology
Leading builder of warp knitting machines, Karl Mayer has invested heavily in China, not only in production facilities but also in a first class technical service organization. Here, we take a close look at the company’s service operations in China. China has the largest garment manufacturing capacity in the world and its operations are highly centralised. More than 70% of all China’s production comes from just six provinces, i.e. Zhejiang, Jiangsu, Shanghai,
26th March 2009
Knitting Industry
|
Shanghai
Leading builder of warp knitting machines, Karl Mayer has invested heavily in China, not only in production facilities but also in a first class technical service organization. Here, we take a close look at the company’s service operations in China.
China has the largest garment manufacturing capacity in the world and its operations are highly centralised. More than 70% of all China’s production comes from just six provinces, i.e. Zhejiang, Jiangsu, Shanghai, Shandong, Guangdong and Fujian. Another feature of the textile and clothing industry in China is that there is a high prevalence of small to medium-sized companies. Large companies and huge corporate groups are the exception, a factor which successful textile machinery producers like Karl Mayer have taken into account. The specialist manufacturer of warp knitting and warp preparation machines, thinks of itself as a dependable partner to all of its customers, and as well as offering an extensive range of products, can also provide customised technical support.
The Karl Mayer Group has reorganised its entire service structure and tailored it to suit the specific nature of the Chinese market, so that the company can respond quickly and professionally in the right place and at the right time. In order to cater for the different industrial areas, the country was divided up into regions and a service network was set up to support all the Karl Mayer Group’s customers. The number of service stations depends on the number of companies in a specific area. Service managers and assistants, regional experts and service technicians are responsible for operating this network of service stations and they all work for the service company, Karl Mayer Technical Service Ltd, an organisation that is dedicated to providing technical support and which is closely linked to the new Chinese production centre, Karl Mayer (China) Ltd. As soon as a customer needs help in his factory, all the experience, professionalism and modern facilities of the entire group are activated.
Karl Mayer operates its own service offices in the south, where there is a high density of textile companies. These technical support stations undertake repair work in their workshops and have a limited number of spare parts available in case of emergency. The activities of the regional service stations concentrate on the specific requirements of the local customers. The regional experts support customers directly from here.
In addition to having a strong regional base, all the technical support operations are focused on the machines and the textiles produced on them. For example, the service and spare parts operations cover lace and net curtains and specials, plain warp-knitted textiles, weaving and warp knitting preparatory processes, and technical textiles. The electrical section covers all of these areas. Every service section has a full service team, consisting of a service manager, an assistant, a spare parts specialist, regional experts and technicians, who all have very specific roles. Whereas the service manager is responsible for managing and coordinating the entire operation, the assistant handles all the queries, from the moment an enquiry is received until the problem has been solved.
Roughly 70 service technicians are employed to do the actual work in customer’s factories and the regional experts are the direct point of contact for the customers. They visit the areas for which they are responsible, check the machines, provide a preventive service, help to solve small problems, and give advice if further help is required. These active technical support experts thus give advice on obtaining spares, help to put the service technicians in place, and also work closely with the Karl Mayer Academy in China to close up any gaps in knowledge. With their strong emphasis on practice, the courses offered by the company’s own training centre play an important role in helping its customers to operate and handle the machines.
The service personnel on site are in close contact with the sales managers, so that they not only provide technical support, but they can also ensure that the needs of the market are met by supplying the right type of machines.
As well as carrying out the more extensive repair and maintenance work, the service technicians also install new machines. To ensure that they can meet these responsibilities, their knowledge must always be completely up-to-date and the service technicians as well as the regional experts therefore have to take part in regular training sessions.
As well as managing the service operations, Karl Mayer Technical Service Ltd is also responsible for providing all the spare parts for Karl Mayer’s machines in China, from storage to dispatch. These two activities go hand in hand and ensure that spare parts can be supplied very quickly. An efficient warehousing system also guarantees rapid delivery times where the average is just one to two days for important parts and the use of a K3 module enables all the orders to be processed quickly. The appropriate quality checks also guarantee that only parts that are perfect leave the warehouse. A testing laboratory, equipped with the latest equipment for testing the electrical components in particular, is available for carefully checking the operational reliability and condition of the machine components. A detailed initial inspection and close cooperation with regional colleagues who are responsible for the repair work, speed up the replacement of components.
With its regionally organised, highly specialised service network, the Karl Mayer Group offers the type of technical support in China that gives the company a real competitive edge in hotly contested markets in times of economic crisis. The company provides support to its clients quickly and professionally, and ensures that all the performance potential of its machines can be fully exploited at all times. This level of technical support, which is up to European standards, is achieved by having modern equipment available and by the highly motivated, highly qualified specialist teams. The service technicians and regional experts undergo regular training in the Karl Mayer Academy and take part in workshops to provide them with job training. Every employee also takes part in an individual training programme to optimise his competence and skills. Last but not least, a black and grey company uniform creates a feeling of identity and an image that represents a level of cooperation that customers can depend on. ‘We care about your future’ is not just an empty advertising slogan but an every-day reality for Karl Mayer.
Business intelligence for the fibre, textiles and apparel industries: technologies, innovations, markets, investments, trade policy, sourcing, strategy...
Find out more