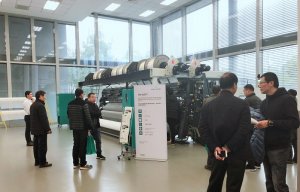
Karl Mayer launches TM Weft in China
The machine processes carbon, glass, basalt, aramid and high-strength polyester fibres, whilst making maximum use of the yarns, with no waste.
28th October 2014
Knitting Industry
|
Obertshausen
The machine can process carbon, glass, basalt, aramid and high-strength polyester fibres, amongst others, whilst making maximum use of the yarns, since the weft is inserted with no waste, the German company reports.
The weft is inserted in line with the stitches without any waste being produced and from both sides of the machine. Working from a creel on both sides of the portal weft-insertion machine avoids the laying device from making empty runs, thus increasing the productivity of the weft system, Karl Mayer LIBA says.
The laying device, which is always fully drawn-in with 20 weft yarns on 20", grips the 20 weft yarns of the creel on one side of the machine during the laying cycle and pulls them in a continuous movement over the working width.
The laying device is then synchronised with the transport chain. Once they are running synchronously, the weft yarns are laid into the transport chain to match the gauge, fixed with yarn clamps, and cut from the bobbins on the creel by means of a circular blade. The laying device then grips the weft yarns on the creel on the other side of the machine and repeats this sequence on the other side.
The two synchronised and fully loaded transport chains then move the weft yarns to the stitch-bonding point and insert every weft yarn directly into a stitch, without the edge having to be cut again. To assist weft insertion in line with the stitches, additional weft yarn feeders insert the yarns into the stitches.
The portal weft-insertion machine is said to enable textiles ranging from coarse grids to fine constructions to be produced. This flexibility allows it to be equipped with the MultiSpeed function.
The special computerised configuration of the entire machine platform enables the values for feeding in the knitting and 0º reinforcing yarns, the take-off values, and the movement of the transport chains to be adjusted to suit the requirements of the pattern.
This enables the distance between the weft yarns, i.e. the number of stitch courses with and without weft yarns, to be altered flexibly right up to full wefts. The sequence of the distance between the weft yarns is therefore freely programmable. The entire machine, from delivery of the warp yarn to take-off, can also be adjusted flexibly to different stitch sizes or lengths.
Compared to the conventional version, which operates with continuous weft insertion, the zero-waste weft insertion facility on the new portal weft-insertion machine is said to reduce production costs.
The conventional system moves continuously and at the same speed, thus laying a weft yarn into every stitch course. Patterning is only possible via the weft yarn drawing-in arrangement in the laying carriage.
In comparison, the weft laying device with the new zero-waste system always works with a full drawing-in arrangement. Pattering is effected via the transport chain which, depending on the programming, moves forwards and lays a weft yarn into a stitch course, or else is stationary.
The new portal weft-insertion machine is available in gauges E 3 and E 6. As standard, the machine operates with the tried-and-tested touchscreen operator console and a servo-controlled take-off system.
Other features include a facility for adjusting the width from 138" (3.51 m) to 71" (1.80 m), up to two guide bars currently, and a 0º yarn feed system. The 0º reinforcing yarns are delivered by one or optionally two zero inlay roller delivery units and can be processed to match the needle gauge or not to match the needle gauge.
The possible applications of the warp-knitted technical textiles produced on the portal weft-insertion machine include advertising and coating substrates, printing grounds, grinding-wheel carriers, tarpaulins, awnings, safety textiles, plaster grids, geotextiles and reinforcing textiles for the construction industry.
According to Karl Mayer LIBA, a prototype machine is successfully producing certified reinforcing structures from carbon fibre for use in textile-reinforced concrete building materials at V. Fraas Solutions in Textile, a technical textiles producer based in Wüstenselbitz in Upper Franconia.
Business intelligence for the fibre, textiles and apparel industries: technologies, innovations, markets, investments, trade policy, sourcing, strategy...
Find out more