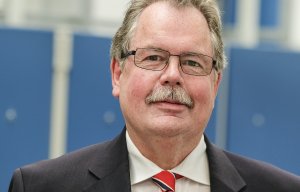
Monforts says goodbye to Klaus Heinrichs
Monforts’ Klaus A. Heinrichs talks about his company’s participation in the VDMA’s Blue Competence sustainability initiative. Blue Competence is an initiative launched by the German Engineering Federation (VDMA) to demonstrate the know-how and experience of its members for sustainable solutions. Key points of the campaign are technologies and products that conserve raw materials, reduce emissions and sustainably improve the living conditions of people.
9th October 2012
Knitting Industry
|
Mönchengladbach
Blue Competence is an initiative launched by the German Engineering Federation (VDMA) to demonstrate the know-how and experience of its members for sustainable solutions. Key points of the campaign are technologies and products that conserve raw materials, reduce emissions and sustainably improve the living conditions of people.
According to Monforts Klaus A. Heinrichs, the Mönchengladbach based company can demonstrate three examples of innovative solutions for how the future can look.
“We had no hesitation in participating in the VDMA’s Blue Competence initiative. Energy management has been one of our primary goals for many years, driving us to develop energy-efficient and resource-conserving solutions,” Heinrichs says.
“For many years textile finishing has operated with chemical and thermal processes which, by present-day standards, can have a very severe impact on the environment.”
“The energy costs are high, and the use of chemicals absolutely essential. But with innovative ranges and intelligent ancillaries, Monforts has succeeded in optimising these processes. The savings benefits that we have achieved in recent years are in some cases, quite considerable.”
Heinrichs goes on to explain his company’s Econtrol process for cotton fabrics:
“During textile dyeing, chemicals are used to fix the dyestuffs on the textiles. Classic processes for the dyeing of cotton textiles, for example, includes 250 grams of salt per litre of treatment fluid. When calculated for three-shift operation, up to 500 tonnes of salt is required annually.”
“For the dyeing and cleaning process with subsequent washing, a total of around 1545 kg of chemicals are required for dyeing processes. An immense amount of energy is also required for the subsequent drying process.”
Together with Dystar, one of the leading producers of dyestuffs, Monforts has developed the Econtrol process for pure cotton textiles. In the process the dyestuff is fixed during and not after drying using a controlled chamber climate with 25% v/v steam; eliminating a complete steaming process. Now, only 20 grams of salt are required per litre. Furthermore, the dyeing result is available after just two minutes and not only after 12 to 24 hours.
For fibre blends (polyester/cotton), Monforts has developed the Econtrol TCA process together with Dystar. It enables polyester and cotton to be dyed simultaneously and not in two process steps as is the norm.
This is made possible by an innovative dispersion dyestuff that is alkaline-resistant and can be applied at the same time as reactive dyestuffs. When dyeing mixed fabrics, the use of chemicals can be reduced by around 86%, the use of water by 63% and the energy consumption by roughly 50%.
The ECO Applicator is a unit which significantly reduces the initial moisture content before the drying process.
As a rule, the fabric is transported through a trough containing the finishing and dyeing liquor. The term ‘liquor’ is generally used to refer to an aqueous liquid in which textiles are washed, bleached, dyed and impregnated.
The ‘wet’ fabric is then dried by means of a stenter. The drying energy is a major cost factor.
In the ECO Applicator, the liquor is applied very thinly by steel rollers. As a result the new unit achieves a maximum energy yield - because moisture that is not applied to the textile fabric does not later have to be dried.
According to Heinrichs, savings in heating and electrical energy of up to 65% are possible if the initial moisture content in the textile is reduced from 70 to 40%.
The ‘Energy Tower’ is a stand-alone air/air heat exchanger for heat recovery. Thanks to its design it is a versatile and flexible retrofit module that enables even older ranges to benefit from the principle of heat recovery.
The module draws in the exhaust air from the drying process and returns it via heat exchangers to the range so that the air is preheated to around 90°C and only has to be heated to 150°C. The high drying temperature is therefore reached more quickly and energy costs are reduced.
The Eco Booster HRC can also help to minimise the energy costs when using stenters. By contrast with purely static heat exchanger modules, the new module actually cleans the stenter during operation; eliminating standstill times for maintenance. Only 100 litres of water are used for cleaning.
The Eco Booster permits a computer-controlled adaptation of the heat exchanger performance to the prevailing waste air stream. This optimised efficiency further reduces the process costs.
The Eco Booster runs fully automatically so that the operator has no additional duties to carry out.
“The trendsetting Monforts technology continues to prove itself and recently left a long lasting impression at ITMA Asia. Asian producers have also recognised the ‘sign of the times’ and the importance of energy efficiency,” Klaus Heinrichs explains.
“Energy efficiency is an important global topic with textile producers faced with the challenge of coming to terms with volatile energy and raw material prices and the ecological demands of retailers and ultimate users.”
“This is a great boost for the German textile machinery industry as a trendsetter and technology leader, and in particular for Monforts.”
“More efficient technology may cost more, but the procurement costs account for less than 20% of the life-cycle costs if you take the total costs for energy into consideration.”
“The payback period for the Monforts technology generally lies in the order of 18 months to two years. Any anyone who recognises that will decide even more quickly for energy-efficient and resource-conserving solutions.”
Business intelligence for the fibre, textiles and apparel industries: technologies, innovations, markets, investments, trade policy, sourcing, strategy...
Find out more