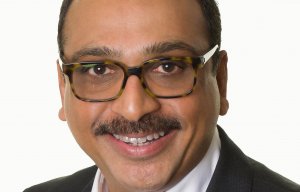
Chemical companies unite to accelerate sustainability
This article was originally published in Kettenwirk-Praxis and has been republished with the kind permission of Karl Mayer. It looks like leather, but no healthy animal hides are used to produce it and it offers exceptional characteristics - synthetic leather represents a real alternative to the expensive, natural version and offers many advantages. It is tough and durable, yet at the same time, it i
6th September 2011
Knitting Industry
|
Obertshausen
This article was originally published in Kettenwirk-Praxis and has been republished with the kind permission of Karl Mayer.
It looks like leather, but no healthy animal hides are used to produce it and it offers exceptional characteristics - synthetic leather represents a real alternative to the expensive, natural version and offers many advantages. It is tough and durable, yet at the same time, it is reasonably priced, resistant to dirt and can be cleaned easily.
The specific features of synthetic leather are also helping textiles to find new and different applications. When producing imitation leather, textiles are used as the backing material for the plastic coating and, together with the type of coating, determine the characteristics of the end product.
For example, the surface layer may have an open-pored or compact construction consisting of PVC, although the modern types are made from PU and are embossed or textured to produce different leather looks. Nonwoven, woven and increasingly warp-knitted textiles, as well as combinations of these materials, are used as the textile materials.
The textile backing materials are mainly responsible for determining the stretch and weight per unit area of the end product - the right design is available to suit every application.
Synthetic leather can be used in jackets, belts, shoes, bags, balls, car roofs, seat covers and furniture, such as sofas and chairs.
In some areas, synthetic leather is not just a cheaper alternative; it is also the only alternative.
For example, the furniture in hospital treatment rooms and medical practices is covered with imitation leather, since it is extremely resistant to the solvents used in the sterilisation/disinfection processes. In many applications, there is a demand for the plastic version, which looks very similar to leather, because of its low weight.
One example of this is in automotive construction. Artificial leather is used in car interiors to cover hard plastic components, such as the dashboard, steering wheel and handles, and it is also used in door panels and in the back and bottom of the seats.
Frequently, the area where the person sits on the seat is made from real leather, while the other areas are covered with the artificial material - a concept that is particular popular among French, American and Japanese manufacturers.
Another important use for synthetic leather is in low-cost furniture. Here too, this synthetic material is frequently combined with real leather.
In general, imitation leather scores points when used as a covering and upholstery material, which is hard-wearing, lightfast and easy to clean. But above all, these multilayer materials, which look like leather, exhibit excellent process ability and stretch when used to cover sharp edges and curved shapes.
However, their elasticity must not be too high - otherwise they will sag and become baggy. When used in clothing, synthetic leather can also set new fashion trends. This lightweight, washable material is reasonably priced and can be processed into a variety of different styles.
Materials having a certain degree of elasticity are also used here. However, the imitation leather used to produce bags has a high dimensional stability.
To make the synthetic material look even more like real leather, the lower side of the textile is flocked with leather fibres and tiny leather pieces. This is primarily a cosmetic process and, apart from the haptic effects, has no influence on the characteristics whatsoever.
Woven and nonwoven fabrics, and occasionally weft-knitted fabrics, are usually used when producing synthetic leather, but warp-knitted fabrics are now being used more and more.
Choosing which textile to use will depend on the final end-use. However, new developments in textiles and optimising the textile products have increasingly blurred the lines between the various end-uses.
For example, woven fabrics have dominated the clothing and furniture sectors until now. Warp-knitted textiles were too elastic to produce upholstery coverings and were too thick for manufacturing fashion goods, and were therefore used mainly for producing bags, luggage and shoes. For these products, warp-knitted fabrics have an excellent tear resistance and a soft handle, and can be draped easily for covering different shapes.
A qualitative market study carried out by KARL MAYER's product management team in China, which is the biggest producer of synthetic leather, shows that more warp-knitted textiles are being used as synthetic upholstery leather. The latest estimates currently put their share at 70-80% of total sofa production.
The warp-knitted textiles used in the synthetic leather industry are primarily produced on the HKS 3-M and HKS 2-3 high-speed tricot machines. The three-bar machine mainly works the ‘trainer' lapping that has already been used so successfully in the sportswear sector:
GB 1: 1-0/2-3
GB 2: 4-4/0-0
GB 3: 1-0/1-2
The fabric is raised in the weft direction; it is soft, and is made exclusively from a combination of textured and un-textured polyester. The coating is usually applied to the un-raised side to achieve a soft handle. The exception to this is the synthetic leather used in furniture. In this case, the coating is applied to the raised surface to give it the necessary strength.
When used for producing backing/carrier substrates for coatings, the trainer lapping is worked with a low stitch number and the textured yarns are processed in a different position to the one that is used to produce warp-knitted fabrics for sports shirts and shorts.
The textiles produced on the three-bar HKS machine are mainly used for covering sofas and chairs. The thickness of the warp knits generally means that they are better for this application than woven fabrics.
The fabrics produced on the two-bar HKS machine are looser and the following lapping can be worked:
GB 1: 1-0/1-2
GB 2: 1-0/3-4
This fabric is also raised on one side and it is used mainly for shoes and bags and in products that have to have a certain stretch. Fine textiles in gauges of E 28 to E 40 are ideal for producing synthetic leather for the clothing industry.
Unlike woven fabrics, a certain amount of expertise is needed when coating warp-knitted textiles. The viscose filament yarns in the plain weave fabrics generally enable the coating to adhere better and the shrinkage behaviour during processing can be controlled more easily. These are important factors for avoiding delamination.
On the other hand, warp-knitted textiles give more scope for varying the thickness, offer advantages when applying the coating thanks to their excellent slip resistance, and have very good mechanical properties, but above all, they are extremely economical to produce.
For example the HKS 3-M can achieve a speed of 2,400 min-1, manufactures products of exceptionally high quality and, compared to water-jet looms, incurs no water costs. Furthermore, when using cotton and viscose yarns, a shearing process has to be carried out to remove any protruding fibres, but this is not the case when processing smooth polyester yarns.
The many possibilities offered by their special features, together with the coatings used, mean that warp-knitted backing substrates offer much more scope for designing materials having a variety of different looks. All in all, these complex performance properties should give new impetus to warp-knitted textiles for use as backings for synthetic leather, which is in keeping with the current fashion for leather-look materials.
Business intelligence for the fibre, textiles and apparel industries: technologies, innovations, markets, investments, trade policy, sourcing, strategy...
Find out more