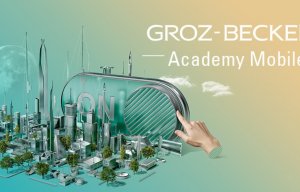
Groz-Beckert July seminars
In this article, leading German warp knitting machine builder Karl Mayer explains the art of producing good quality warp knitted velour fabrics, using a unique combination of knitting and finishing technology and know-how.
10th September 2014
Knitting Industry
|
Obertshausen
In this article, leading German warp knitting machine builder Karl Mayer explains the art of producing good quality warp knitted velour fabrics, using a unique combination of knitting and finishing technology and know-how.
Upholstered furniture is an elegant interior design element. It creates an oasis of calm and its soft upholstery invites us to make ourselves comfortable for a while. This feeling of comfort and cosiness is produced by the soft, erect fibrous upholstery, which can be produced in a range of different designs.
Depending on the type of process, the height of the pile loops, and thus the extent of the three-dimensional effect, can be adjusted. Velvet is produced with pile loops of up to 2 mm in length, velour is produced at a loop length of 2 to 4 mm, and plush is produced when the loops are longer than 4 mm. Finishing is used to create further effects on the fleecy textiles, and includes raising, shearing and brushing.
An HKS 3-M P machine is used to produce fabric with a velvet like surface. This high-speed tricot machine with pile mechanism produces a typical loop pile fabric from polyester filament yarns. The loops are then cut open during the subsequent shearing process. The fibrous layer has a high degree of fibre orientation and a relatively flat construction.
Warp knitted fabrics having a pile height greater than 4 mm are produced on double bar Raschel machines. Karl Mayer’s RD machines produce two fabric webs with two needle bars, with a pile yarn joining them in-between, which is subsequently cut. The final fabric is known as cut plush.
No pile mechanism is needed to produce warp knitted velour having fibrous layers of average height. The most suitable machine in this case is the HKS 3-M in a gauge of E 28, which produces a fabric with long underlaps, which are then raised slightly or thoroughly.
If elastane is processed in the ground, the long yarn stretches can also be cut open. The velour fabric shown here was produced by raising. The starting fabric was a dense, warp knitted fabric consisting of a plain construction and a counter notation tricot construction worked by ground guide bars GB 3 and GB 2, combined with a long underlap. Ground guide bar GB 1 worked the long underlap of 12-13/1-0 to process the yarns lying on top.
During the subsequent finishing process, the underlap was raised thoroughly, i.e. it was cut through completely. Another processing stage was then carried out on the fabric, in which the longest filaments were cut. This shearing process, which is also known as yarn end cutting, produces a uniform surface. If yarn end cutting is not carried out, the cut fibre ends produce a plucked, fleece-like surface.
The process that combines warp knitting with long underlaps, thorough raising and yarn end cutting produces an tilting velour with a dense, stable fibrous layer without any fibre orientation. In contrast to tilting velour, this velour cannot be stroked in a specific direction. With upright velour, the cut surfaces of the vertical fibres determine the appearance of the fabric with its matt, velvety shimmer, and not the peripheral surfaces of the filaments, which are more or less flat.
Upright velour has a full, dense feel and is dimensionally stable. It also exhibits exceptional pull-out resistance – a typical characteristic of warp-knitted velour.
This characteristic in particular makes this fleecy fabric ideal for producing soft toys, i.e. fabrics with pull-out resistance are a requirement for many countries. In addition to being used in cuddly toys, warp-knitted upright velour fabrics are perfect for chair and seat upholstery in public buildings and the contract sector.
The velour fabric on this page weighs 379 g/m2 and is made entirely from flat and circular multifilament polyester yarns.
Karl Mayer’s product developers worked closely with specialists at Xetma Vollenweider GmbH on the finishing processes since, as Andreas Schneider says, "Producing raised velour is a complex business. All the processing stages, from selecting the yarns to making the tips uniform, must be harmonised with each other. Raising, in particular, requires a great deal of knowledge and expertise."
Xetma Vollenweider’s sales manager, an experienced manufacturer of dry textile finishing machines, was involved with carrying out the processing tests on warp knitted velour in the company’s own technical centre.
A Multisystem XR is available in Xetma’s laboratory. This machine consists of 24 raising rollers in the working position and 12 rollers – with the same or different roller covers – in the stand-by mode. The variable pile/counter-pile raising roller ratios of the Multisystem XR can be used to create a variety of finishing effects, including conventional pile/counter-pile raising in a ratio of 1:1, and the fully felting process using only pile or counter-pile rollers.
Xetma Vollenweider is also the first manufacturer to develop raising technologies using different ratios between the pile and counter-pile rollers. Depending on the number of raising rollers in the drum, pile/counter-pile ratios of 1:2, 1:3 and 1:4 are possible, in which case, the higher the number of counter-pile rollers, the shorter and denser is the raised pile. This is an advantage when processing woven and weft knitted fabrics, whose ground has to be raised intensively and then consolidated.
If the raising roller ratio is set optimally to suit the particular article, higher output levels can be achieved for shorter processing times. The roller clothing, i.e. the characteristics of the raising surface, is also important for the properties of the velour. The relationship between the technical parameters of the raising process and the results are to be investigated in detail during further trials to be carried out by Xetma Vollenweider and Karl Mayer.
A uniform surface was produced on the fibrous layer by yarn end cutting in one of the last processing stages.
Business intelligence for the fibre, textiles and apparel industries: technologies, innovations, markets, investments, trade policy, sourcing, strategy...
Find out more