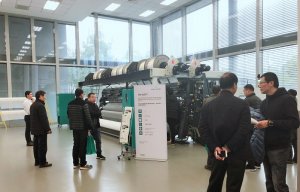
Karl Mayer launches TM Weft in China
Compared to the conventional version, this new machine offers an improved cost:benefit ratio and advantages in terms of its operation and maintenance.
25th November 2014
Knitting Industry
|
Obertshausen
Karl Mayer Malimo, the leading textile machinery manufacturer that specialises in technical textiles, has combined the key components of its RS MSUS-V machine with biaxial technology and developed a biaxial machine featuring weft insertion in line with the knitted courses to suit the market.
This new innovation is known as the Biaxtronic CO and compared to the conventional version, this new composite machine is said to offer an improved cost:benefit ratio and advantages in terms of its operation and maintenance.
The products made on this machine are also said to provide a different type of quality, making them suitable for the Chinese wind turbine market – Chinese manufacturers of multiaxial structures for the blades of wind turbines require a construction containing weft yarns that are not pierced during the knitting process.
As with all stitch-bonded biaxial textiles, the fabrics produced on the Biaxtronic CO are made up of zero inlays and weft yarns and, if required, an additional base web, such as a chopped glass strand mat or a nonwoven.
The two reinforcing yarn systems are inserted absolutely straight and parallel at angles of 0 and 90º and fixed in place by stitches. This is said to avoid variations caused by the construction, which lead to loss of strength and undesirable stretching with woven fabrics.
The weft yarns are not pierced or damaged. This enables higher strength levels to be achieved when using conventional materials. As well as that, new yarn combinations can be used for the same strength values, the company reports.
The Biaxtronic CO is available in working widths of 100", 101" and 102". The gauges available as standard are E 5, E 6, E 7 and E 10. The standard features also include the KAMCOS system, an N-drive with a maximum of three pattern discs, an operating interface with 12.1" touchscreen monitor, and a warp beam frame with one or two warp beam positions.
An electronically controlled yarn let-off drive is available for each mounted warp beam. The maximum flange diameter of the sectional warp beams is 32". The zero inlays are delivered via electrically driven delivery rollers from creels. The tried-and-tested MSUS system is responsible for weft insertion.
The knitting elements are also similar to those of a weft-insertion warp knitting machine, and include a compound needle and closing wire bar, knock-over sinker bar, zero inlay bar, counter retaining bar with support rail, and one or two ground guide bars for stitch formation. Every yarn is tied-in in a stitch at the knitting point to bond the structure of the textile.
The Biaxtronic CO combines the latest materials with complex design solutions, especially in terms of the drive technology and the weft insertion system. These optimised features enable this high-performance machine to reach speeds of up to 1,400 min-1 and to achieve maximum production rates of 6.5 m/min, the manufacturer reports.
The weft laying frequencies are also extremely high. The Biaxtronic CO produces top-quality products. In particular, the continuous transport belt for feeding the chopped glass strands under the yarn layers produces textiles with no faults. This system guarantees that the chopped glass strand mat and the weft layer are kept separate at all times.
Business intelligence for the fibre, textiles and apparel industries: technologies, innovations, markets, investments, trade policy, sourcing, strategy...
Find out more