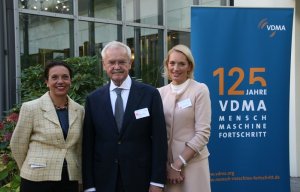
Regina Brückner elected new chairperson of VDMA
Greek circular knitting company Komotex AG has taken delivery of the country’s first Thies iMaster H2O dyeing unit and claims to have achieved rapidly successful results. The company produces ‘body width’ tubular fabrics, ranging in diameter between 20 and 90cm. Production Manager, Arno Stumpp says: “It is not easy to find a dyeing machine able to produce high quality results for such narrow and very sensitive articles.” “The reason for ou
20th April 2011
Knitting Industry
|
Xanthi
Greek circular knitting company Komotex AG has taken delivery of the country’s first Thies iMaster H2O dyeing unit and claims to have achieved rapidly successful results.
The company produces ‘body width’ tubular fabrics, ranging in diameter between 20 and 90cm. Production Manager, Arno Stumpp says: “It is not easy to find a dyeing machine able to produce high quality results for such narrow and very sensitive articles.”
“The reason for our success with the new Thies unit is a direct result of the internal winch technique, which ensures a gentle treatment of the fabric without affecting its elasticity,” Mr Stumpp says.
As part of the German-based International Group ESGE Textilwerk Maag, a 4th generation family owned company founded in 1881, Komotex was established in Xanthi almost 40 years ago. The company specialises in high quality circular knitted goods for ladies, gents and childrens underwear, including the ESGE, Pompadour, CITO and Schöller brands, as well as producing under the Bugatti licence. It also produces products for branding by other international companies.
The Greek operation carries out knitting, dyeing, bleaching, finishing and cutting before transferring the cut pieces to ESGE’s facilities in Bulgaria and Romania for make- up and final shipment to customers.
“We specialise in producing ‘body size’ tubular knits guarantying that with most of them there are no side seams in the finished products” said Arno Stumpp.
The company works with a wide mix of fibres and blends including cotton, wool, micro modal, viscose and polyamide together with elastane.
Many knits feature, for example, cross dyed white polyamide and cotton to produce striped effects. A special product, ‘Jacquard-streifen’ (jacquard stripped effect) may contain 40% polyamide, 30% viscose, 25% micro modal and 5% elastane. Another typical product contains, for example, 95% micro modal and 5% elastane.
“As one of Europe’s leading producers of knitted underwear, we are highly experienced in producing top quality products, where the specifications and parameters are constantly monitored. These include the weight (gsm) and the all important residual shrinking – where very stringent tolerances are specified, particularly for knits containing elastane.”
Where the knits contain elastane they undergo a heat setting pre-treatment at temperatures of up to 185°C. Generally, Komotex works with knitted weights of between 120 – 180 gsm, but if it includes cotton/elastane ribbing on for example sleeve cuffs, the weight can increase to 250 gsm.
“When working with a 3 minute rope cycle, for example, we must closely watch all the specified parameters to ensure that the tolerances are met,” says Arno Stumpp.
Komotex took delivery of its first Thies dyeing machine, a 4-chamber eco master, some 18 months ago, following poor support and technical problems with a previous supplier. The company says the eco master has proved to be excellent in meeting its special requirements for the dyeing of small ‘body size’ diameter knits.
The second Thies unit, the new, recently introduced, iMaster H2O was installed late last year. Featuring two chambers, each with a nominal capacity of 100kg, the unit is said to have proved even more successful with the company’s special knits demanding even lower residual shrinkage parameters.
“Since its installation we have opted to use the new iMaster H2O unit to achieve the highest quality while achieving the low shrinkage tolerances demanded by our customers– all as a direct result of the unit’s internal winch drive,” Arno Stumpp clarified.
“I consider that this development is the future for knitwear dyeing operations, and welcome its possible introduction in higher capacity units.”
The winch in the new iMaster H2O model is located inside the kier and designed to operate at speeds of up to 500 m/min. Featuring individual drives, the winch is frequency controlled and features a low rope lifting height to ensure minimum fabric tension. It also offers reduced maintenance, easy handling, and lower spare parts costs and is ‘completely’ interchangeable unit.
The new Thies iMaster H2O dyeing machine has been designed to handle all types of fabric and knit goods whilst ensuring economical and environmentally friendly operation, offering ultra low liquor ratio’s as low as 1:3.7 for cottons.
“We must always look to reducing our utility overheads including water, and the iMaster H2O’s low liquor ratio is another plus for the new unit when we are treating cotton products,” Arno Stumpp stated.
Komotex generally operate the machine with 200kg/batch but, depending on the product occasionally reduce it to 140kg. The company normally works with a total dyeing cycle time of 5-6 hours but, once again, depending on the fabric being produced, it can be extended to 8 hours to meet specific quality standards demanded by Komotex.
Business intelligence for the fibre, textiles and apparel industries: technologies, innovations, markets, investments, trade policy, sourcing, strategy...
Find out more