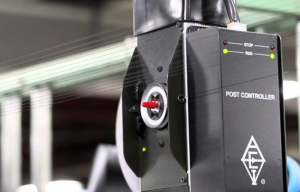
Karl Mayer acquires YTC yarn tensioner technology
Technical progress in the warp knitting is certainly the domain of German machine builder Karl Mayer and the continual increased performance, quality and flexibility of the machines it produces have helped the company enjoy considerable success for many decades around the world. One of the most important chapters in the company’s history was the integration of carbon-fibre-reinforced plastic (CFP) bars into the machines and the corresponding modification of t
23rd March 2010
Knitting Industry
|
Obertshausen
Technical progress in the warp knitting is certainly the domain of German machine builder Karl Mayer and the continual increased performance, quality and flexibility of the machines it produces have helped the company enjoy considerable success for many decades around the world.
One of the most important chapters in the company’s history was the integration of carbon-fibre-reinforced plastic (CFP) bars into the machines and the corresponding modification of the machine design. The CFP high-precision composite components are up to 25% lighter than conventional components and are also more rigid, enabling speeds to be increased considerably for simultaneous optimisation of machine availability. The high temperature stability of the CFP materials has enabled the window for problem-free machine operation to be increased from +/- 2°C to +/- 5°C and subsequently to +/- 7°C.
The company’s tricot machines were the first to profit from this lightweight construction technology, and have been available with CFP bars since ITMA 2007 in Munich. Once the gradual changeover of that particular machine series had been completed, work began on adapting the company’s raschel machines and the first machine with CFP components, the RSE 4-1, will appear in the market at the beginning of April this year.
Karl Mayer has now further optimised the use of this technology and made it easier to operate with a revamped bar and shaft concept. The company’s engineers have come up with a solution which has allowed high temperature stability, now a standard feature in warp knitting technology, to be achieved more easily and efficiently. The key to the increased efficiency is the substitution of the old continuous tempered shafts with control of the bars with components that have been divided up into high-precision segments.
Karl Mayer says the shaft is divided into segments according to specific machine parameters and it is no longer necessary to carry out the ‘heating-up’ stage that was previously required following a machine stoppage. This has reduced the time-consuming heating-up phase, cut down on energy costs and dispensed with the need to specifically adjust components during the start-up phase, the company says.
In addition to the short start-up times, Karl Mayer says that machines equipped with second generation CFP technology are more stable to ambient temperatures when operating and thus guarantee high gauge accuracy. Even when producing fine fabrics and at large working widths, the machine runs smoothly at top speed to produce top-quality textiles, Karl Mayer says.
Karl Mayer says the changeover to high-speed knitting machines with second generation CFP components will start shortly and will be carried out gradually over the course of the year. Karl Mayer has applied for patent protection for the innovative system.
Business intelligence for the fibre, textiles and apparel industries: technologies, innovations, markets, investments, trade policy, sourcing, strategy...
Find out more