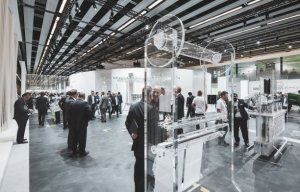
Groz-Beckert Webinar: Ultra-fine knitted fabrics
Warp knitting machine builder Karl Mayer, says there is currently a high demand in the clothing and lingerie sectors for delicate, sheer, elastic knitted fabrics. The German company says these exceptionally pliable fabrics enable completely new designs to be created, offer haptic characteristics that have never been achieved before, and promise continuing lucrative business - a trend that has encouraged warp and
12th October 2011
Knitting Industry
|
Obertshausen
Warp knitting machine builder Karl Mayer, says there is currently a high demand in the clothing and lingerie sectors for delicate, sheer, elastic knitted fabrics. The German company says these exceptionally pliable fabrics enable completely new designs to be created, offer haptic characteristics that have never been achieved before, and promise continuing lucrative business - a trend that has encouraged warp and weft knitters to develop fabrics in extremely fine gauges.
Karl Mayer claims its new HKS 2-3 E machine (right) is setting new standards in the production of super-fine fabrics. The new machine has a record fine gauge of E 50 and its technical features enable it to produce what the company calls ‘the finest warp-knitted stretch fabrics in the world'.
"The basis for this exceptional achievement is the clever way in which tried-and-tested components for processing elastane have been combined with specific new innovations," Karl Mayer explains.
The knitting elements in particular were completely redesigned for operating at this particular needle gauge to enable them to process extremely fine yarns.
According to Karl Mayer, the HKS 2-3 E provides controlled relaxation and handles the fabric so that felting and tension variations are eliminated. To do this, the machine has been equipped with the elastic fabric batcher no. 29 B.
The standard fabric batcher no. 34 A or AE, which is also suitable for taking-up stretch fabrics, was not used in this case because its friction-driven ascending batch winder cannot handle the fabric gently enough.
"When producing very fine fabrics, the increasing roll weights may often cause felting and stitch distortion. On the other hand, type no. 29 B operates with a central winder equipped with an active drive," Karl Mayer explains, adding:
"The speed of the shaft is adapted to suit the increasing roll diameter by means of an automatic, fabric-tension-controlled speed regulator - an expensive but reliable solution, especially when taking-up very fine fabrics, which also guarantees a uniform roll build-up."
Another device for improving the quality of batching is the integrated spreading device. The three shafts just in front of the central winder smooth out any edges that have rolled over by means of spiral springs, thus ensuring that the roll build-up is straight in the horizontal direction.
In addition to the central winder, the 29 B batcher also has a relaxation zone. This zone, which is located immediately after the fabric take-down point, reduces any inherent tension and consists of several smoothly rotating rollers for transporting the fabric.
Protechna supplies Procam, a camera monitoring system for use in fabric quality control, which Karl Mayer fitted to its E 50-gauge HKS 2-3 E for last month's ITMA trade fair.
The optical inspection system was premiered at ITMA 2003, and is mainly used in the production of high-quality stretch articles and automotive fabrics. Unlike conventional systems using a scanner, which moves continuously from left to right and back again along the fabric web to detect faults, the new Procam camera monitoring system provides a complete overall picture of the entire fabric piece between the knitting elements and the take-down point.
The fabric is therefore inspected in the lengthwise and crosswise directions across the entire width. Karl Mayer says, any faults are detected reliably, objectively and reproducibly - and this system reduces the reaction time considerably when dealing with yarn breakages.
The machine is stopped instantly and reliably right at the position where the fault has occurred, which is said to guarantee the shortest possible fault lengths, even at high operating speeds. Minimal time and effort are said to be required to make adjustments when the fabric has to be changed, which increases the efficiency of the Procam system even more. The maintenance and upkeep costs are also claimed to be low, since this contactless monitoring system operates without any wearing parts.
The HKS 2-3 E was largely developed to process elastane yarns only. It can reach speeds of more than 3000rpm can thus achieve a rate of productivity that Karl Mayer says puts it far above comparable technologies, such as circular weft knitting technology.
The HKS 2-3 is also available with a gauge of E 50, and is an all-round machine for producing non-stretch fabrics. Both machines are also available in gauges E 36 and E 40 and with a working width of 130 inches.
According to Karl Mayer, the high-speed, two-bar tricot machine in a gauge E 50 can produce a lightweight, opaque stretch fabric from microfibre yarns, whereby the construction of the knitted surface can hardly be detected by the naked eye. This is due to the exceptionally large number of stitches per square centimetre. Despite having the look of a woven fabric, these pliable fabrics have the typical stretch characteristics of warp-knitted textiles.
The ultra-fine fabrics can even be used to produce body shaping effects, says Karl Mayer. At ITMA 2011, the HKS 2-3 E in gauge E 50 was producing a sample that fully meets the requirements of Invista's Lycra beauty fabric concept.
The body shaping and comfort characteristics of the fabric were successfully tested in accordance with the standards laid down by Invista, a producer of polymers and fibres. It now carries the Lycra beauty label in the ‘Sculpt' category. This classification applies to lighter-weight fabrics with high-tech functions and more subtle shaping.
The fabrics weigh less than 200 gsm. Sculpt comes after the ‘Smoothing' and ‘Sensual Curves' categories and before ‘Control' in the sequence of shaping effects, and describes a fabric where the main emphasis is on compression and the body shaping effects.
Karl Mayer says the high yarn density in the E 50-gauge fabric also produces a silky shimmer, a soft, uniform handle and a drape that can adapt easily to different shapes and forms. These characteristics open up completely new possibilities when designing products, the company says.
The specific physical and textile characteristics of these extremely fine warp-knitted stretch fabrics are currently being evaluated by Karl Mayer's product developers, who are carrying out the relevant tests and investigations.
Business intelligence for the fibre, textiles and apparel industries: technologies, innovations, markets, investments, trade policy, sourcing, strategy...
Find out more