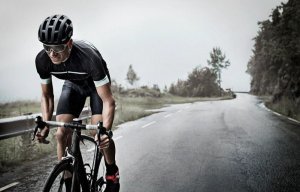
British cycling boom fuelled by textile technology
Truetzschler offers future-oriented technologies that enable the production of high-quality yarns from cotton waste
17th February 2020
Knitting Industry
|
Tashkent, Uzbekistan
© Truetzschler
“The demand for clothing is increasing worldwide, but the areas for cotton cultivation are limited.” These are the words of fibre preparation specialist Truetzschler, a textile machinery manufacturer which, contributes significantly to the sustainable use of this valuable raw material with future-oriented technologies that enable the production of high-quality yarns from cotton waste.
One example of a successful sustainability concept is Bakan Tex in Uzbekistan, a company founded in Tashkent in 2017 after the Uzbek government decided to promote the entire value chain around its domestic textile sector.
Bakan Tex produces first-class combed ring spun yarn. In the process, the so-called ‘comber noil’, which contains short fibres and neps that are undesirable in high quality combed ring spun yarn, is combed out at the combers. As the fibres have already passed through the blow room and over the cards, it is high-quality waste.
© Truetzschler
“Comber noil is a recyclable raw material which is used, for instance, in banknotes or hygiene products. It can also be spun into excellent rotor yarns. This is made possible by shortening the process through the use of integrated draw frames (IDF),” Truetzschler explains. “To allow processing into a good yarn, the fibre length can be significantly shorter thanks to the IDF and the yarn is of excellent quality even if 100% comber noil has been processed. Until now, this has not been possible without the shortened process.”
Bakan Tex already uses this great potential. In its subsidiary FT Textile, founded in 2019, a rotor spinning mill which processes the noils of Bakan Tex is operated with 250 employees and 22 Truetzschler IDF 2 systems produce the feed for 8640 rotors. In addition, the company has invested in additional IDF machines and a recycling plant to process blow room and carding waste with the short preparation process.
Truetzschler spoke to three FT Textile executives - Mr Sekar Rajam CEO, Mr Jaya Prakash, Quality Production Manager and Mr Abdukayum Saidov, Director, about the advantages of the shortened process with IDF.
From left to right: Mr. Sekar, Mr. Saidov, Mr. Prakash. © Truetzschler.
Truetzschler: What made you decide to process your own noils with IDF2? What convinced you of this concept?
FT Textile: At FT Textile we rely on OE spinning. We use 100 % raw cotton, but also cotton mix with waste (comber noil). This process allows excellent processing of short fibres (fibre length 20.6 mm) into yarn.
Truetzschler: What are the main advantages of the shortened process for your spinning mill? Does it open up savings potentials for you?
FT Textile: This process is particularly suitable for us, since we can use short waste fibres produced during combing without any problems, in addition to so-called virgin cotton. This not only saves raw materials, but also space, energy and personnel.
Truetzschler: How much yarn do you already produce with the shortened process? And how are your future plans in this respect?
FT Textile: So far, we have produced an average of 450 tons per card. We produce yarn from Ne 10 to 36. In the near future, we expect to produce at least 1,000 tons of yarn with consistent quality from each card.
Truetzschler: What blending ratio do you use? And how much waste and raw cotton do you blend?
FT Textile: We produce with three blending ratios: The first blend consists of 100 % raw cotton, blend 2 of 80 % cotton and 20 % waste. Blend 3 contains only noils.
Truetzschler: How do you assess the yarn quality? What do your customers say?
FT Textile: Excellent! We are extremely satisfied with the quality. We have not yet received any major complaints from our customers.
Truetzschler: For which end products are the yarns produced with the shortened process (IDF2) used?
FT Textile: Our customers mainly come from the knitwear (circular knitted fabrics) and woven fabric sector.
Truetzschler: In your opinion, what are the ecological advantages of this process?
FT Textile: The most important advantages for us are the significant energy savings and the reduced space requirement. Also important for us is the fact that we need less personnel due to the simplified can transport.
Truetzschler: How do you assess the future significance of the shortened process?
FT Textile: We are convinced that the shortened process will continue to be important for us.
Truetzschler is committed to achieving maximum value creation and quality for its customers by means of innovative concepts, trendsetting and efficient processes as well as a high level of service competence. In the areas of spinning preparation, card clothing and nonwovens/BCF it offers cutting-edge technologies and complete services throughout the world, all the way to turnkey systems.
Business intelligence for the fibre, textiles and apparel industries: technologies, innovations, markets, investments, trade policy, sourcing, strategy...
Find out more