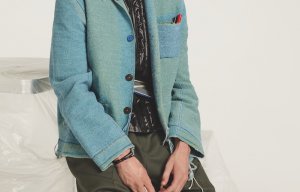
Stoll holds product innovation seminars at Pitti Filati
When ITMA Asia + CITME opened its doors in Shanghai one month ago, German flat knitting machine builder H. Stoll & Co was popping the champagne corks to celebrate the company’s 135th anniversary. Stoll was actually founded 135 years to the day on the 27th of July 1873. Â Developed from the pioneering spirit of Heinrich Stoll, the company is now a worldwide enterprise with a presence in over 70 countries with 135 years of inventions, patents and almost 300 different machin
27th August 2008
Knitting Industry
|
When ITMA Asia + CITME opened its doors in Shanghai one month ago, German flat knitting machine builder H. Stoll & Co was popping the champagne corks to celebrate the company’s 135th anniversary. Stoll was actually founded 135 years to the day on the 27th of July 1873.
Developed from the pioneering spirit of Heinrich Stoll, the company is now a worldwide enterprise with a presence in over 70 countries with 135 years of inventions, patents and almost 300 different machine models behind it. At ITMA Asia + CITME, Stoll demonstrated how a company with a long tradition and established technology should continue to innovate.
Stoll emphasizes the importance of flexibility and productivity as key factors for knitters’ economic success and presented its Multi Gauges concept as the ideal solution. Company spokesperson and Head of Marketing, Gerhard Berger told KnittingIndustry.com:
“We believe that the days are gone where a separate machine can be provided for each gauge. At Stoll there's only one answer to the question “coarse or fine?”. Both! Because the machines of the Multi Gauge class from Stoll can knit several gauges, even without needle exchange or gauge conversion.”Berger added: "The main advantage of Multi Gauge is that the user’s plant can be fully optimized giving greater flexibility. The capacity of all machines is optimized and even the shortest development times, latest trends or seasonal changes are no longer a problem."
Stoll also stresses the ability of these machines to demonstrate flexibility in the fashion sector with the option to have different gauges within the same knitted piece. Fine areas (knitted with all needles) and coarser areas (knitted with every second needle) can be combined easily. In the Multi Gauge process, it is possible to work with different numbers of ends of the same yarn in different areas in the same piece or to work in the same way with yarns of varying thickness or count. Patterned areas can not only be arranged in different colours but can also appear as different gauges.
The flexibility of the Multi Gauge machines, which are offered with working widths of 45 inches to 96 inches and two to six knitting systems, was demonstrated in Shanghai in a wide range of applications. Stoll exhibited a new prototype version of its best selling CMS 530 compact flat knitting machine which is faster and better than its predecessor. The CMS 530 multi gauge, with a working width of 50 inches (127cm) and three knitting systems was shown in three different gauges demonstrating three different applications. A prototype CMS 530 multi gauge machine was exhibited in 8.2 gauge which according to Stoll gives productivity increases of up to 14% depending on the fabric width, gauge and fabric type knitted. This is achieved through different technical improvement measures such as shorter carriage stroke, faster carriage turn around and higher carriage speed. Stoll emphasize that this can be achieved without compromising machine reliability or stitch appearance. The machine’s maximum knitting speed is 1.2m/s but it runs at 1.5m/s on empty rows.
The 8.2 gauge machine exhibited was knitting a men’s fully-fashioned zig- zag offset intarsia front panel sequentially in gauges 12, 14 and 16. With Stoll’s latest intarsia kit fitted to the CMS 530 it is possible to use 32 intarsia yarn carriers in narrow staggering and to supply them individually by means of Stoll’s clamping and cutting devices with 2 x 16 individual clamping and cutting points. This way complex intarsia patterns and 3-colour Jacquards can be produced in a quick and competitive manner, Stoll claims.
A CMS 530 multi gauge in 7.2 gauge was also exhibited with which Stoll demonstrated that permanent analysis of the main machine components is carried out on an ongoing basis. An example of this is in the stitch formation area, where Stoll continues to develop stitch appearance and spectrum and thus also the flexibility of the machines. With the exhibited machine, also a prototype, development was carried out on needle bed geometry, which lead to even higher fabric tension. This was demonstrated by the fabric shown at the exhibition, a sleeveless ladies’ shirt with V-neck and inclined running stitches in split technique without empty rows.
Stoll also demonstrated a new technique for tying-in ends when knitting intarsia on a CMS 530 in gauge 3,5.2. The machine was knitting a sleeveless multi gauge intarsia men’s shirt. According to Stoll, the new patent pending technique offers clear cost benefits for intarsia knitting, as the time-consuming and expensive manual knotting of yarns can be eliminated. The yarn ends are tied-in to the fabric directly on the machine without extra strokes and loss of time.
When knitting a new yarn, the first knitted stitch is split and then immediately transferred again. This way the yarn is fastened tightly to the old stitch. Additionally, this technique offers the possibility of knitting-in the yarn without a tuck loop and to securely feed-in starting from the first needle. With the standard method, the yarn has to be looped to the colour field border by using tuck loop. Afterwards these tuck loops have to be eliminated expensively by hand.Additionaly, with some yarns it is impossible to avoid visible markings in the fabric. Other knitting-in techniques such as locking by transferring or knitting-in with draw thread can also cause permanent markings. With Stoll’s new split technique the yarn is pressed into the needle hook by the closing needle latch (latch turn over). A secure yarn insertion without markings in the fabric is therefore ensured.
Stoll’s CMS 822 multi gauge is available in gauges 2,5.2 to E8.2. At ITMA Asia, a dress with a horizontal stitch line in the finished dress was produced as yard goods on the CMS 822 in gauge 7.2 which was also equipped with the company’s new intarsia kit. A classic intarsia argyle pattern, using 26 intarsia yarn carriers, covers the entire dress with different gauges. In addition, the dress is divided into two different gauges. The top has fine gauge knitting at the waistline and a coarse gauge knitted area of the flared skirt from the waistline down to the hem.
On the CMS 420 E multi gauge in gauge E6.2, a front of a ladies’ lace top was knitted sequentially. Four gauge appearances from coarse to fine were knitted sequentially.
A CMS 933 multi gauge in 3,5.2 gauge was also exhibited. With 2 x 3 systems and a working width of 96 inches (244cm) or 2 x 46 inches (117 cm), the CMS 933 multi gauge is according to Stoll, the most productive among the Multi Gauge machines. The machines is available in gauges ranging from 3,5.2 to 8.2. An intarsia fully fashioned men’s sweater in multi gauges with vertical and horizontal stripes in coarse gauge was knitted on the machine in tandem mode.
Two Knit & Wear models were exhibited. As well as the CMS 730 S Knit & Wear in gauge 7.2, a new model, the CMS 830 S Knit & Wear, was also shown. With an extra wide working width of 86 inches (218 cm), Stoll says that the machine is ideal for the production of oversized complete garments. The new model is equipped with three knitting systems and can be delivered in gauges 7.2 and 9.2. The machine shown was in gauge 9.2 and knitted a dress with a 12 gauge appearance.
Stoll’s exhibition program was rounded off by several machines from its Compact class, including two special machines. The CMS 530 T offers special pattern effects as well as narrowed fabrics knitted with all needles, which can be realized in a productive manner due to the divided additional transfer beds. At the show this was demonstrated with a sleeveless fully fashioned men’s hooded jacket with integrally knitted intarsia border. The fabric knitted with all needles will be plated with Lycra.
The CMS 530 T was equipped with Stoll’s new Plating Kit. Stoll offers its plating solution for all machine models (except the CMS 520 C and CMS 830 C Knit & Wear) for plating operations with covered elastane yarn. The new plating kit offers a professional solution for up to two plating operations and is offered in two variants attachable on the left or on the right machine side or on both (Up to 4 plating operations/yarn feeder tracks).
One variant offers optimized special plating yarn feeders which can also be used for normal knitting. The other works with special yarn feeder carriages taking-on normal yarn feeders. On both versions the yarn carriers are adjustable in height and longitudinal direction. The adjustment ranges are considerably wider than before offering an optimal setting option also for the most different yarns and patterns. The kit also includes a bobbin holder for two elastic yarn bobbins to be fixed horizontally. The bobbin holder has sensitive brakes and break control for processing the elastic yarn without slack tensioner. The thread tension is adjustable and the feeding has an electric stop function.
The well known CMS 520 C which Stoll says, always sells especially well during boom times for coarse knitwear was also exhibited. With this model, coarse gauge fully fashioned articles in 3 gauge can be knitted in a productive and reliable way. At the show, this was represented by a sleeveless fully fashioned mini dress with 1x1 and 2x2 cables produced in a hand-knit look.
Another machine from the Compact class shown was the CMS 420 E, with which a plated men’s sweater was knitted. The fully fashioned sweater was plated with Lycra using Stoll’s new plating kit. Finally, Stoll showed a CMS 822 in gauge E18, with which two fully fashioned pieces were produced simultaneously.
Coming soon on KnittingIndustry.com: Part 2 - 'Stoll - Tradition, Technology, Innovation'
Business intelligence for the fibre, textiles and apparel industries: technologies, innovations, markets, investments, trade policy, sourcing, strategy...
Find out more