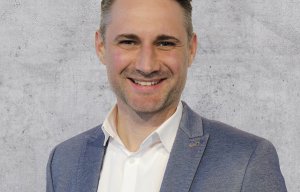
Personnel changes at Brückner
At Forest Side in Mauritius, CDL Knits is producing around 17 tonnes of knitted fabric every day.
28th November 2017
Knitting Industry
|
Leonberg
German textile machinery producer Brückner Textile Technologies has worked with Tropic Knits Group, a producer of high-quality fine knit garments for brands from Europe, US and South Africa, to develop a completely new machine concept, which CDL Knits, a fully integrated knitting, dyeing and finishing plant of the Tropic Knits Group, bought for its production site in Mauritius.
At Forest Side in Mauritius, CDL Knits is producing around 17 tonnes of knitted fabric (a variety of cotton fabric, cotton blends and viscose) every day, out of which 80% is assigned for Tropic Knits, which converts them into garments. For a long time, the operations and finishing team of CDL Knits has been looking for leaner production processes that would lead to further savings in terms of resources and energy.
The finishing line the company operated at that time comprised a relaxation dryer, a stenter and a compactor. The intention was to replace these three finishing machines by only one line without compromising the quality.
The new Brückner line for knitted fabric, which will in future replace CDL's three finishing machines is a special design: a relaxation dryer with pre-arranged stentering zone. Scroll rollers in the entry of the line provide for the spreading of the fabric and skew straightening rollers for the reduction of spirality. After that the fabric is pinned on precisely directly behind a special selvedge spreading unit, so that the selvedge waste is later reduced to a minimum.
A non-lube vertical transport chain, developed particularly for knitted fabric, transports the fabric through a ten metre long stentering zone. It is provided with a selvedge gumming unit, comprising several IR dryers and further hot air dryers for a complete drying of the gummed selvedges. Depending on the process and the fabric quality, it is possible to operate with up to 60% overfeed and a wet overstretching of 40% and more, according to the manufacturer.
At the end of the stentering zone a selvedge cutting device is installed. With minimum tension the fabric is then fed on to a specially coated transport belt leading into the 4-zone relaxation dryer. The fabric is dried with an optimised air control concept and it is relaxed due to the tumble-like movement so that the residual shrinkage is reduced to a minimum. The individually adjustable air flow in the dryer and the wet spreading and shrinkage in the stentering zone allows to influence the quality features such as shrinkage, fabric width and fabric surface to the optimum. The curling of edges in the dryer is prevented by a systematic and selective arrangement of the circulating air. “This new technology allows to save previously required expensive process steps,” the company explains.
Brückner’s Technical Director for Mechanical Design, who is an expert for the finishing of knitted fabric, visited CDL Knits in Mauritius directly after commissioning of the new line. Together with the customer he made tests with different fabrics and determined the optimum process parameters for each fabric quality.
After a short time, CDL was able to start the production. “The fabric quality is better than expected and the residual shrinkage, as well as the spirality, are for all fabric types less than 5%. CDL is already now saving about 40% of electrical and thermal energy compared to their previous process. But the biggest saving is definitely the significant reduced process time. Where previously 90 hours were required, is today 20 hours to achieve the same productivity. This gives enormous benefits regarding the delivery time,” the company reports.
The Tropic Knits Group is part of the Fine Knits cluster of Ciel Textiles, which is also located in Mauritius. Once a year Ciel Textiles hosts the Ciel Textile Chairman’s Manufacturing Excellence Award for its capital-intensive companies. The Knitting Division of CDL Knits won the award for Manufacturing Excellence twice in 2015 and 2016.
“This year, in September 2017, CDL won the World Class Innovation & Creativity Award. The installation of the new Brückner line at CDL Knits and the corresponding benefits for the company played a small but nevertheless important role in winning the award,” the company reports.
Business intelligence for the fibre, textiles and apparel industries: technologies, innovations, markets, investments, trade policy, sourcing, strategy...
Find out more