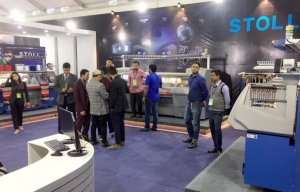
Stoll presents latest innovations in Bangladesh
The very latest flat knitting technology from leading German flat knitting machine builder Stoll went on show at a three day Open House Event from 3-5 July at Stoll GB Ltd’s newly refurbished showroom and design centre in Leicester, UK. A range of the latest Stoll machines was exhibited but the star of the show was the CMS ADF-3, Stoll’s electronically controlled flat knitting machine with direct yarn feed and motorised yarn feeders.
13th August 2013
Knitting Industry
|
Leicester
The very latest flat knitting technology from leading German flat knitting machine builder Stoll went on show at a three day Open House Event from 3-5 July at Stoll GB Ltd’s newly refurbished showroom and design centre in Leicester, UK. A range of the latest Stoll machines was exhibited but the star of the show was the CMS ADF-3, Stoll’s electronically controlled flat knitting machine with direct yarn feed and motorised yarn feeders.
The Reutlingen headquartered company’s CMS ADF-3 was unveiled at last year’s recent ITMA ASIA + CITME 2012 in Shanghai and has been exhibited more recently in Germany and Italy before being shown in the UK. The CMS ADF-3 gets its ADF designation from the name Autarkic Direct Feed, with the word autarkic coming from the German autark, meaning independent or self-sufficient – referring to the individually controlled yarn feeders.
The CMS ADF-3 is radically different to Stoll’s current machine range where feeders are moved in and out of the knitting area by the cam box or carriage and where the yarn path to the needles runs from the yarn packages at the rear of the machine via the top mounted yarn control units and side mounted friction feed wheels at either or both sides of the machine.
In the case of the ADF machine the yarn path is simplified by being fed directly from the top mounted yarn control units to the needles between the open or split carriage – there is no prohibitive bow connecting the front and rear cam boxes.
Direct feed aims not only to lower yarn tension but also equalise yarn tension as the carriage moves back and forth, leading to better quality fabrics.
The ADF’s yarn feeders are completely independent of the carriage movement and are controlled independently by motors. The machine is fitted with eight double sided radially positioned feeder rails and can be fitted with 16 feeders for each end of the machine giving a maximum of 32 feeders. Each of the 32 feeders is driven by two motors via belts – a larger motor controls the horizontal movement of the feeder and a smaller motor controls the vertical movement of the feeder.
The radial feeder rails are said to help maintain exact feeder position at knitting, especially where accuracy is required as in intarsia knitting. The motorised vertical feeder movement replaces the need to swing or swivel the feeder in complex knitting situations and also eliminates wasteful feeder kick-back by carriage movement.
At first impression the ADF is something akin to other machines which use motorised feeders and direct feed. However, the machine is actually significantly different on closer inspection and its programmable motorised control of vertical feeder movement sets it apart.
For intarsia fabrics, up to 32 feeders are used in two knitting systems with the third system being reserved for stitch transfer allowing ‘full production’ at every stroke of the carriage. Stoll estimates that fabrics take two and a half times longer to knit on a standard machine using feeder kick-back - feeders can be moved in and out when required in very small areas and no feeder kick-back is required. The multi-colour intarsia being knitted on the E12 ADF machine in Leicester showed the narrow field possibilities of the machine and the benefits of having independent feeder control. Much narrower colour fields are now possible for intarsia knitting on the ADF machine.
The ADF also enables the knitting of plated intarsia patterns which has always been possible to do on standard machines in theory but has not been practical until now. As motorised feeder adjustment is carried out via the machine’s touch screen controller, feeder position and height can be controlled accurately without the need for manual adjustment and setting. This, Stoll says allows the high level of precision required for intarsia plating.
Reverse plating in intarsia, where back and front bed knitting in the same colour is combined with other colours/ structures in the same course is another ADF advantage. In plating the ADF machine uses the two feeder technique which is widely used on standard flat knitting machines. However, each feeder is set relative to the other and in height position via the touch screen controller only.
The ADF machine also introduces an updated clamping and cutting system where the machine can go directly from knitting to clamping and cutting. Current CMS models are required to employ ‘empty carriage strokes’ to bring clamping and cutting into play which occurs often during multi colour intarsia production.
The ADF’s standard feeders can be used for normal knitting, intarsia, plating and inlay. Stoll says there is no longer a need to change feeders for specific applications.
The ADF machine does however also use a lot of proven Stoll technology such as its sprung latch needles, CMS needle beds, take-down and standard CMS HP cam box carriage with 5 inches between knitting systems. Available gauges are E10, 12, 12/10, 14, 14/12, 16, 18, 7.2 and 8.2.
Other machinery and equipment demonstrated at the event were:
Stoll GB recently announced that it is the sole agent in the UK for Mentasti finishing equipment and in addition to the Stoll exhibits, the following equipment was on display and being demonstrated during the event:
A technician from Mentasti was on hand to demonstrate the equipment and answer any technical queries visitors had.
The well attended event, which hosted most of the UK’s leading knitwear manufacturers, took place at Stoll GB’s purpose built showroom and Design Centre which opened in May this year. As well as machine sales, the company offers a full range of services such as full machines parts supply, after sales support and innovative Design Centre, where designers can work alongside technicians to develop and realise their design concepts ideas.
Stoll Backs UK Knitwear Design Centre
Business intelligence for the fibre, textiles and apparel industries: technologies, innovations, markets, investments, trade policy, sourcing, strategy...
Find out more