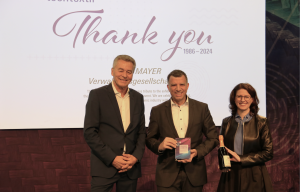
Techtextil founding exhibitors award for Karl Mayer
Company receives positive feedback on new developments. Smart solutions are of particular interest to large knitting mills and fully integrated companies.
18th June 2024
Knitting Industry
|
Albstadt, Germany
Mayer & Cie. presented an overview of its current portfolio in the circular knitting sector at the recent ITM in Istanbul. Two machine types – the SF4 3.2 III and the Relanit 3.2 HS II – and various smart solutions that make circular knitting more efficient were on display. knithawk, a tool for the optical detection of knitting defects, met with interest among the visitors. The same was true for knitlink, Mayer & Cie's hub for digital solutions.
Spare parts packages and conversion kits are also in demand for the long-term value retention of Mayer & Cie. machines. Overall, the industry continued to be restrained at the ITM, and a trend reversal has not yet been achieved.
"In line with the current market situation, we went to ITM with subdued expectations," says Benjamin Mayer, Managing Partner of Mayer & Cie. "As expected, visitor numbers fell short of those of 2022. Nevertheless, we have received positive feedback on our new developments. Our smart solutions are of particular interest to large knitting mills and fully integrated companies."
Making the tried and tested even better
The Relanit 3.2 HS mechanical single jersey machine offers high productivity, especially in the context of elastic plating. It processes a wide range of yarns and qualities extremely reliably. It is particularly suitable for processing recycled yarns. Their energy consumption is up to a third lower than that of a circular knitting machine with conventional technology.
In Istanbul, Mayer & Cie. presented an updated version of its flagship machine - the Relanit 3.2 HS II. The new open width take down is the single component that attracted the most interest. It ensures a uniform pull-off tension of the knitted fabric over its entire circumference. The knitted hose is only opened below the take-down rollers. Furthermore, the take-down is equipped with two drives - one for tensioning, one for rewinding and both can be controlled separately.
Another innovation of the Relanit 3.2 HS is aimed at reducing downtimes. The needle with predetermined breaking point, which was developed together with Groz-Beckert, prevents it from breaking uncontrollably and, in the worst case, breaking needle butt. The new spring sinker is also a joint development with Groz-Beckert. This makes the Relanit 3.2 HS II run more smoothly, produce less noise as well as with less wear and tear.
"Overall, the demand for single jersey knitted fabrics is currently low, which was also evident again in Istanbul," says Benjamin Mayer. "However, this is no reason for us not to further develop popular machines. After all, experience shows how quickly trends can change."
Lightweight three-tread fleece fabrics
With its SF4-3.2 III, Mayer & Cie. is addressing a trend in the clothing industry that is reflected beyond Turkey - lightweight, elastic three-thread knitted fabrics in both pure cotton and blends. The machine impressed at the ITM with its excellent plating ability, which saves time and costs when finishing the fabrics.
New Control 5.0
Both ITM machine exhibits were on display with the new Control 5.0 machine control system. Control 5.0 is a prerequisite for using knitlink, the hub for Mayer & Cie's digital applications. In this function, the machine control system attracted interest from various large customers.
In the standard SmartControl version, as shown in Istanbul, a so-called Smart Knob is attached to each machine foot. From there, all the functions that the machine operator needs for his work are available. More in-depth settings, such as those made by the knitting manager, are only possible from a mobile device. Any number of Mayer & Cie. machines can be operated from this at the same time.
All machines built from 2001 onwards can be retrofitted, and selected new machines will be equipped with the new generation of machine control systems from 2024.
Recognising knitting errors at an early stage
knithawk, a tool for optical defect detection, inspects the knitted fabric as it is produced. It sits in the single jersey machine directly at the knitting point. If knithawk detects a serious or recurring error, the machine is stopped. The tool also creates an error log.
"knithawk helps us save resources such as water, natural fibres and polyester," says Axel Brünner, Senior Product Manager at Mayer & Cie. "Real-time defect detection prevents many meters of defective fabric from being creazed in the first place."
Machine-specific upgrade and conversion kits
With its upgrade kits, Mayer & Cie. brings technological innovations to existing machines. These range from machine-specific upgrades, such as the Performance Kit for existing Relanit 3.2 models to the Senso Blue RS lubrication system.
In addition to the upgrade kits, Mayer & Cie. offers conversion kits for popular machine types. Two are currently available, one for the MV4 3.2 II/MBF 3.2 and the other for the S4-3.2 II/ SF4-3.2 III.
"Thanks to our long-standing representative Mayer Mümessillik, our Turkish customers can rely on competent and fast support, whether it is support for the conversion of a machine, digital solutions or the installation of new machines," concludes Benjamin Mayer.
Business intelligence for the fibre, textiles and apparel industries: technologies, innovations, markets, investments, trade policy, sourcing, strategy...
Find out more