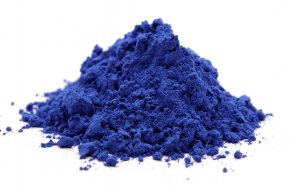
Call for action on textile wet processing
Adrian Wilson talks to imogo founding partners Ellinor Niit and Per Stenflo about their Dye-Max spray application technology for dyeing cotton and other cellulosics.
17th November 2020
Knitting Industry
|
Linhamn, Sweden
Adrian Wilson (AW): Hi Ellinor and Per, can we start by introducing imogo’s spray application technology for dyeing cotton and other cellulosic fabrics – the Dye-Max?
Ellinor Niit (EN): Sure. Dye-Max spray dyeing technology can slash the use of fresh water, wastewater, energy and chemicals by as much as 90% compared to conventional jet dyeing systems. This is due to the extremely low liquor ratio of 0.3-0.8 litres per kilo of fabric and at the same time, considerably fewer auxiliary chemicals are required to begin with.
Per Stenflo (PS): All of the chemicals are used in the process which also greatly reduces the production of wastewater and the low liquid content in the fabric meanwhile minimises the energy needed for fixation.
AW: You’re based in Sweden, and recently became a member of TMAS, the Swedish textile machinery association. Scandinavian countries in general have pioneered many new sustainable textile initiatives, from brand leaders back to the developers of new fibres as alternatives to cotton, such as re:newcell in Sweden and Spinnova in Finland. Yet you have reservations about the true sustainable value of such products?
The problem is that all the environmental benefits the fibres potentially deliver may be lost in the further processing, and especially in conventional dyeing.
PS: It’s not the fibres themselves, but the processes they’re subjected to in conventional manufacturing – especially dyeing and finishing. These fibre developments are very admirable. Spinnova is making fibres from forestry industry waste fibres and can recycle its own fabrics and make new fibres out of them and re:newcell is using recycled cotton waste, but then, what happens to them before they get to the consumer? How do you make it really a completely environmental process?
The problem is that all the environmental benefits the fibres potentially deliver may be lost in the further processing, and especially in conventional dyeing. The same is also true for organic cotton and recycled polyester. If you’re turning PET bottles into polyester fabrics, the circular stream that’s being established for making new PET bottles from used ones is also just being diverted from a circular system.
EN: There was a major project by the Swedish research organisation Mistra Future Fashion, involving many brand and research institute partners recently. The project’s Fibre Bible 1 and 2 reports conclude that it’s very difficult to make assumptions that one fibre is better than another, because it’s so much about how fabrics and garments are being produced from them. It’s not the material itself. If you produce in a process where you are still using coal for generating electricity, for example, and not greener electricity – the sustainable footprint is hugely different. The study also found that 55% of the chemicals used in a garment come from the dyeing. Even if a garment is being labelled as made from ecological cotton, it is probably produced in the same way as standard cotton, and sometimes will use even more chemicals, because there’s a need for some extra processes. So basically, an organic or recycled cotton t-shirt is not automatically more sustainable than a conventional cotton t-shirt, or even one made from synthetics – the alternative fibres are a good start, but you have to consider the entire life cycle of a garment.
PS: What we’re trying to do in all of our communications is bring this aspect up, because it’s generally being overlooked. There’s a lot of attention given to these new fibres and rightfully so – they’re great. But then the next steps – the processes – are lost in discussions and it ends up being just a very small percentage of environmental savings that are being made, when in the bigger picture they could be much more significant.
AW: Is it also a problem that these new fibres usually end up in blends with others?
EN: It can be, and it’s important for all the designers and engineers who are developing new textile materials to keep this in mind. What types of fibres are they going to blend, and is it really necessary? What purpose is the blend serving? Elastane is now in everything, for example, and that causes huge problems in recycling later on.
PS: Colouration also plays a big part in this, and blending natural fibres and synthetics also involves two dyeing processes, of course, creating double the amount of waste.
AW: Using alternative fibres is perhaps also not asking for such a big a commitment from the textile manufacturer, in terms of investment, compared to taking on a new technology?
PS: That’s true, and that’s important as well, of course, but maybe it doesn’t have to be a big investment. We are looking at alternative business models and with our equipment, depending on who you are as a producer, it’s not a gigantic investment to really take some serious steps. We calculate a one-to-two-year return on investment if it’s a fully paid for system, but there are renting and other options.
AW: What about cooperations coming from the brands back down the supply chain, because that would be an ideal scenario? Where the brands are taking much more of an interest in the entire process?
EN: There is definitely an interest from a lot of the brands we’re talking to. They see it, but their challenge is that it’s much easier to communicate about new fibres than about the dirty processes that follow. So that’s the challenge. A second is making these fibres genuinely feel like regular cotton, and progress is ongoing there.
AW: Do you see a strong movement away from fast fashion in Sweden?
PS: Well, there’s certainly a movement, but I’m not sure how strong it actually is. All of the major Swedish brands now have sustainable collections but how sustainable they really are is sometimes questionable. I don’t question their ambition to be more sustainable, but how can they be, when the supply chains look like they do and there are such limited options for sustainable processing? It’s not possible today. There are a handful of Dyecoo units out in the world, for example, and that’s probably the most sustainable way of dyeing polyester, but that’s limited to Nike and Adidas and maybe a few others. Everyone else has no option but to go down conventional manufacturing routes. There are a lot of smaller brands popping up too – not just in Sweden – with big sustainable ambitions, and they try, but how successful can they be, given the infrastructure that’s in place?
EN: We should mention one Swedish company that is doing really well, and that’s the workwear brand Fristads, which has introduced the first Environmental Product Declaration for such products and got a huge response from both consumers and corporate customers. It helps that the look for workwear products such as jean jackets with oversized pockets is very much now in terms of fashion in Scandinavia, and their sustainability agenda is being driven at a grass roots level.
AW: In addition to cotton and cellulosics, have you looked at how effective DyeMax is on synthetics like polyester?
EN: Right now, our focus is on cotton, and in our processes so far, it’s easier for us to dye cellulosics. I have many years of experience in dyehouses, however, and with polyester it was always possible to achieve 100% fixation on the fibres, with not as many pre-treatments required as there are for cotton, such as scouring, bleaching and desizing, along with other pre-treatment processes even before you can start to dye. Next year we are planning to scale up our tests on polyester.
AW: So, in summary, what’s the key message from imogo?
PS: New clean fibres and dirty old processes don’t make sense together.
EN: There are not enough alternative routes allowing textile manufacturers to bypass those conventional, resource-intensive systems. Yet…
Business intelligence for the fibre, textiles and apparel industries: technologies, innovations, markets, investments, trade policy, sourcing, strategy...
Find out more