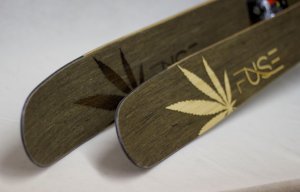
Natural fibre composites and knit-to-shape products
Lovis Kneisel, CEO of Fuse, talks to Karl Mayer’s Ulrike Schlenker about an alpine ski made from hemp-based composites.
10th April 2024
Knitting Industry
|
Obertshausen, Germany
Markkleeberg, Germany based Fuse, a biobased composites manufacturer, is one of the main players in a current project to develop an alpine ski with an overall more sustainable and ecological production process than before. Specifically, the CO2 footprint is to be significantly reduced, and to achieve this, the value chain is to be converted to a circular one and production is to be switched to processing the renewable raw material hemp in composite production. Fuse is working together with Karl Mayer Technische Textilien on the latter task.
Ulrike Schlenker from the Corporate Communication team at the Karl Mayer Group spoke to Lovis Kneisel, Managing Director of Fuse GmbH, about the background and expectations surrounding the project.
Ulrike Schlenker (US): Why did you choose to build an alpine ski for the joint project?
Lovis Kneisel (LK): We had already been working on the development of adapted semi-finished products for biocomposite products in various market sectors for some time before the start of the project. Alpine sports is an industry that is fundamentally very open to innovations in the field of sustainability and, due to the many small players, provides rapid feedback on the suitability of new material systems and process approaches.
Alpine skiing as such is an enormously exciting product, as the focus here is very much on performance. In close cooperation with SPURart in particular, our team has succeeded in substituting 100% of the glass fibre used and still developing an extremely high-performance ski. Even the SPURart pros are impressed by this innovation both on and off the slope.
US: Flax fibres are already being processed in the composites sector. What fascinates you about hemp? Are there any concrete figures on the benefits of this natural fibre in terms of environmental impact?
LK: Flax and hemp are largely related in terms of their performance in composite materials. The advantage of hemp over flax lies in its ecology, but also in its economy. Unlike flax, hemp can be grown completely without chemical pesticides and is also available in good quality outside Belgium and France. As we consistently rely on secondary fibres - the so-called value fibres - for our semi-finished products, we are not in the usual procurement competition with the clothing industry for flax long fibres and can therefore pass on a very attractive cost structure to our customers.
US: What are the main advantages of using natural fibre tapes compared to natural fibre yarns in terms of the process chain and impregnation behaviour?
LK: The tapes are produced directly from the fibre as a flat structure, which saves the entire spinning process and also parts of the subsequent surface formation. The advantage of this is an essentially streamlined process.
US: What impact do you expect the project to have? What potential is there for the composites industry in other market segments? In your opinion, what other applications are possible apart from sports and automotive?
LK: Natural fibre composites can be used in many different areas of application. The focus is not only on mobility or sports applications. They also offer advantages when used in load-bearing components in the building and construction sector or in the logistics sector. We are currently working together with a Swiss start-up to develop a circular Euro pallet.
US: How can natural fibre-based composites be paved the way for widespread applications? What challenges are there?
LK: The industry's interest in bio-based materials is very high and growing rapidly in light of the urgent need to decarbonize the industry. Biogenic raw materials in general, and fibres in particular due to their high-performance requirements, are growth-dependent in terms of their qualitative and quantitative character. The main challenges are therefore always the reliable provision of high-quality and homogeneous materials and the continuous reduction of supply costs for industrial semi-finished products.
US: Let's talk about the cooperation with Karl Mayer Technische Textilien. How long have you been working with this partner in the composites industry and what do you value about them?
LK: The cooperation with Karl Mayer developed in the course of initial preliminary investigations for the HempSki project described above and has been steadily expanded since then. We value the company for its innovative spirit and its constant willingness to try out new things.
US: Thank you very much for this interesting interview.
Business intelligence for the fibre, textiles and apparel industries: technologies, innovations, markets, investments, trade policy, sourcing, strategy...
Find out more