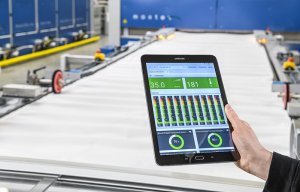
Destination Istanbul for Monforts
The Eco Applicator is a soft coating unit, which is designed to eliminate the need for conventional wet-on-wet padders.
8th August 2017
Knitting Industry
|
Mönchengladbach
With energy prices continuing to increase, Monforts Eco Applicator ‘bucks’ this trend for woven and knitted fabrics with retro fitting to existing finishing lines, the manufacturer of textile finishing machines reports.
In many textile mills, the cost of running integrated manufacturing lines – especially those for fabric finishing that can involve numerous sequences of heating and subsequent drying – is now eclipsing the cost of paying people to operate them. As a consequence, any process that can be introduced to reduce energy costs is welcomed by the market.
Monforts Eco Applicator has been highly successful since its introduction, both integrated into new finishing lines or retro-fitted to existing ones, according to the company.
The Eco Applicator is a soft coating unit, which is designed to eliminate the need for conventional wet-on-wet padders, instead employing trough and roller techniques to apply the required amount of liquid/coating to the fabric.
The unit itself does not actually save the energy, but by applying only the precise amount of functional finish, has been developed to ensure the subsequent drying time is shorter – in some cases dramatically so. The Eco Applicator’s versatility also allows mills to apply finishes to just one side of the fabric, or both, and even to apply separate finishes to each side, or to specific areas of a fabric, for endless possibilities, whether treating wovens, denim or delicate knits.
While being widely market-proven on woven and denim fabrics, major knitting manufacturers are now reaping the benefits the Eco Applicator provides.
Knitted fabrics must never be stretched and need to be treated in a relaxed state. The Montex 8500 stenter with vertical or horizontal chain return incorporates a TwinAir nozzle system that ensures the relaxed fabric is kept at a suitable height in between the upper and lower nozzle system, allowing for the fabric’s ‘bowing’.
Similarly, the Eco Applicator for knits is fitted with an advanced guidance system specially-adapted to the needs of delicate treatments and eliminating any possible ‘curling’ of the fabric edges prior to entering the stenter.
Compared with a padder system, where the initial moisture content of the fabric entering the stenter is 60%, with the Eco Applicator it is reduced to 40% and the knit fabric also has the shortest fabric path from the unit into the stenter.”
Business intelligence for the fibre, textiles and apparel industries: technologies, innovations, markets, investments, trade policy, sourcing, strategy...
Find out more