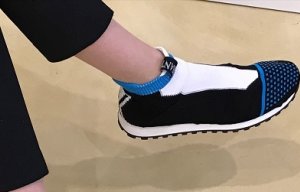
Third millennium shoe offers style, comfort and sustainability
Company launches an innovative safety shoe upper concept, designed to safeguard the planet, as well as the user’s foot.
26th February 2024
Knitting Industry
|
Brescia, Italy
The manufacturing process behind footwear releases large amounts of carbon dioxide. It is responsible for 1.4% of greenhouse gas emissions in the world, meaning that a pair of sneakers generates on average 30 pounds of CO2 emissions.
According to estimates from the World Trade Organization (WTO), around 23.2 billion pairs of shoes were produced in total in 2021, approximately 9 million tons by weight. It is therefore fundamental for the footwear industry to find sustainable solutions to reduce, recover and recycle waste efficiently.
It is necessary to create products differently, rethinking all manufacturing and raw material supply processes, to redefine the future of production. That’s the mission that led Santoni when it came to create the first 3D work shoe upper with its XT-Machine. The goal was to knit a shoe upper that could perfectly adapt to the foot and protect it during work, guaranteeing utmost breathability and comfort, without affecting the environment.
Santoni’s XT-Machine facilitates the production of three-dimensional uppers in single or double-layer fabric, which offer comfort, lightness, performance and unparalleled quality, in just ten minutes and without any waste.
By mapping the foot, the machine can position high-performance and completely recyclable yarns in the desired areas: TPU yarns with high resistance to abrasion or anti-cut in the areas of greatest stress, and yarns made up of natural fibres where there is direct contact with the foot, to simultaneously guarantee maximum comfort and protection.
After the knitting phase, the upper is almost ready for the application of the sole, thus generating a shorter manufacturing process that reduces times and transportation of fabrics and accessories.
This approach offers several advantages, including faster production and greater flexibility, therefore less use of energy and production of CO2, as well as the least possible waste of raw materials: the shoe is only made up of the yarns necessary to produce the upper, eliminating waste material and the subsequent disposal of scraps. This shows that technology can be an essential tool to reduce the impact of the footwear industry on the environment, and this is an important step towards a more sustainable future.
Business intelligence for the fibre, textiles and apparel industries: technologies, innovations, markets, investments, trade policy, sourcing, strategy...
Find out more