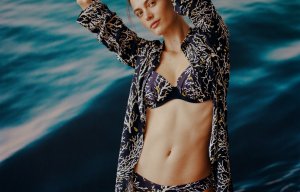
Creative awards for Chantelle and Wolford
Opinion
Anne Prahl reports from the annual beachwear, underwear and athleisure show, held in Cannes from 7-9 November.
15th November 2023
Anne Prahl
|
Cannes, France
MarediModa, the beachwear, underwear and athleisure fabrics and accessories trade fair, showcased a wide range of lower impact materials and processes, demonstrating the industry’s growing ambition to reduce its environmental footprint.
Over 100 premium European textile companies previewed their summer 2025 collections and key trends included the continued development of recycled and bio-based fabric options, the exploration of future circular solutions, and a focus on water and textile waste footprint reduction through the use of improved and new processes.
From lower impact to circularity
The use of lower impact fibres and yarns is on the increase in the beach, underwear, and athleisure industry as the collections on display demonstrated a strong focus on recycled, bio-based, biodegradable, and recyclable options for polyester, polyamide, and elastane.
Recycled polyester fabrics made from post-consumer plastic waste and polyamide fabrics from pre-consumer production or post-consumer material waste, have become a staple in most fabric collections, as they are known to reduce carbon footprint compared to the use of virgin resources.
Claudio Taiana, president at Taiana, noted that around 50% of the company’s production is now recycled. Taiana’s Relyfe collection utilises NEWLIFE recycled polyester filament yarn made from post-consumer plastic bottles and combines eye-catching colours and textures, such as seersucker effects.
Recycled elastane alternatives include Creora Regen by Hyosung made from 100% reclaimed waste and Lycra’s EcoMade, which consists of 20% pre-consumer Lycra fibre waste.
As designers are beginning to fall out of love with recycled synthetics made from post-consumer single-use plastic, textile manufacturers have started to explore alternative feedstocks. One example is Brugnoli’s Circle-Art collection, which utilises Fulgar’s Q-Cycle yarn made from recycled waste tyres, which would otherwise end-up in landfill, as they can’t be recycled into new tyres. These waste tyres are transformed into oil through a process called pyrolysis and subsequently made into polyamide yarn and fabrics.
Bio-based synthetics are another interesting area, as adoption of these types of fabrics can reduce the industry’s GHG emissions and dependence on fossil fuels. Brugnoli’s Br4 collection of bio-based fabrics makes use of EVO by Fulgar yarn derived from castor oil and is manufactured through a process which reduces both water and energy consumption by 20% compared to standard processes.
Innovation around bio-based stretch fibres is also on the rise, as Hyosung launched their elastane Creora made with 30% of bio-based raw materials in 2022 and The Lycra Company is currently collaborating with Qore to develop Qira, the first large-scale bio-derived elastane made with 76% renewable, non-edible corn. The material will offer the same functionality on stretch and recovery as current products and initial seed quantities will be available in early 24, while large-scale production and sales will commence in 2025.
Stretch fabrics are key in the swim and sportswear sector but the use of elastane is considered a major obstacle for textile recycling. The Lycra Company are therefore working on future stretch fibre recyclability through various collaborations, such as their partnership with Decathlon. For the manufacture of their swimwear material NEGOMBO, the sporting goods retailer replaced elastane with Lycra’s mechanical stretch T400eco fibre, which was combined with a patented and optimised knitting technique. The material’s composition is 52% recycled polyester and 48% T400eco and the product is already on sale, while the recyclability process is currently being tested with recycling partners.
The Lycra Company are also working with a selection of textile recyclers on technologies for recycling Lycra fibre and Lycra T400 fibre in blends with cotton, polyamide, and polyester. Initial tests indicate that the presence of 10% Lycra T400 fibre in a 90% recycled polyester fabric does not disrupt the recycling process and the company is continuing with further trials with various recyclers.
According to textile manufacturers at the fair, biodegradable fabrics are attracting much attention, as designers are trying to reduce the impact of unintentional synthetic fibre release on the environment. Both Eusebio and Brugnoli presented biodegradable fabric collections made with polyamide Sensil BioCare yarn, which is enhanced with an additive to accelerate the breakdown of microfibres in landfills and oceans. The fabrics start to break down after 200 days, are described to disintegrate by 80% after three years and have been certified as not harmful to human health according to Oeko-Tex standards.
In their GreenLabel collection, Iluna Group utilise Amni Soul Eco yarn, which is also equipped with additives to speed up the material’s decomposition. While Amni Soul Eco decomposes in around 3 years in landfill and marine environment conditions, it is also 100% recyclable.
However, when choosing biodegradable textiles to combat harmful fibre shedding, it is important to also carefully consider any chemicals utilised in the colouration process or additional finishes applied.
Minimised water footprint
Most swim and beachwear fabric collections rely on strong colours and eye-catching prints and therefore go through extensive dyeing and printing processes, which traditionally require considerable amounts water, while potentially causing pollution. As awareness of these negative environmental impacts is growing with brands and consumers, it is encouraging to see more technical developments and commercial adoption of alternative colouration processes.
While companies like Eusebio utilise a closed-loop system which stores and reuses water from the dyeing and finishing process, many textile manufacturers have chosen dope-dyeing to reduce their water footprint. The process, also known as solution dyeing, adds colour to synthetic fibres before they are spun into a yarn. This method reduces water, chemical and energy use compared to traditional dyeing, as well as offering fade-resistant colours.
Iluna Group presented their extensive stretch lace collections, which use GRS certified Y.E.E.S. green Double D by Ambrofibre yarn, a dope-dyed pre-consumer recycled polyamide. The benefits of this yarn include a 55% saving in water usage, reduction of energy consumption by 54% and a 52% reduction on CO2 emissions per ton of yarn processed.
Estilmar showcased their collection made with the company’s Zero Water sustainable printing system, resulting in up to 95.6% reduced water consumption. The digital printing processes can be used on polyamide, polyester, viscose, and cotton, while reducing the need for five different machines and seven process steps to just one machine and two steps, including printing and drying. The entire process only takes 7 minutes and is suitable for neon colours as well as providing excellent colour matching regardless of the fabric composition.
Eurojersey introduced their new range of printed swimwear fabrics including customisable digital placement prints, which reduce water consumption due to the elimination of the steaming and washing stages. Building on the company’s Ecoprint technology, which boasts impressive environmental savings including the reduction of water consumption by 60% and energy consumption by 30%, Eurojersey have formulated a new print pigment recipe, which can be applied to plain and textured fabrics to create a washed-out ‘delavé’ effect.
Engineering out textile waste
Textile waste from the development and production stages is a significant issue, as industrial development and adoption of waste management systems and suitable textile recycling technologies are still underdeveloped.
As reported by Francesca Spinetta of Intima Media Group during her talk on product and process innovation for the beach and underwear sector, only 32% of the 50 textile companies interviewed recycle their production waste into new materials, while the remaining 68% opt to donate production leftovers to non-profit organisations, schools, universities, and start-ups.
Companies are increasingly employing digital technologies to reduce the production of textile waste in the first place, by ‘engineering out’ waste materials from the design, development, and production process. One such example is Penn Textile Solution’s Dreamknit collection, which utilises digitally knitted engineered panels, compression zones and placed breathability to reduce production waste and enable easier recycling through mono-material construction.
Also in focus was the use of 3D software systems to reduce material consumption and leftovers. Digital fabric libraries and virtual sampling play an important part in design and development, as Francesca Spinetta of Linea Intima revealed that 34% of surveyed textile manufacturers already digitise their entire collection, while 28% digitise more than 50%, and 19% less than 50%.
Digital solution provider Style3D Assyst and textile manufacturer Boselli & C. collaborated to showcase the latest fabric collections and 3D simulated product designs on a Fabric Kiosk, where users can digitally manipulate fabric and product designs. By combining a selection of software tools within the wider digital ecosystem, brands and textile and product producers can virtually collaborate to create better products in less time, reduce prototyping and material waste, and optimise cost and sustainability benefits.
Business intelligence for the fibre, textiles and apparel industries: technologies, innovations, markets, investments, trade policy, sourcing, strategy...
Find out more