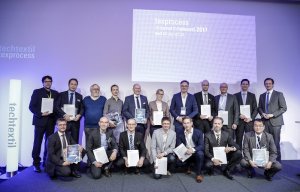
Texprocess honours new textile-processing ideas
Lenzing Group, Santoni SPA and Procalçado SA presented a joint concept to showcase that a sustainable solution for the footwear industry is already in existence
16th May 2019
Knitting Industry
|
Frankfurt
Tencel footwear. © Lenzing AG.
Lenzing Group, Santoni SPA and Procalçado SA presented a joint concept to showcase that a sustainable solution for the footwear industry is already in existence, at the Texprocess exhibition this week in Frankfurt.
“It is now up to the brand and designers to bring it to the consumer level,” Lenzing said in a statement today. “It is time that the polluting and hazardous footwear manufacturing process becomes cleaner, more circular and sustainable”, says Birgit Schnetzlinger, Business Manager Footwear at Lenzing.
The three-partner collaboration shows ways to reduce water impact, production time and minimize plastic waste in shoe production, making it a more sustainable and circular solution. The result of the partnership consists of the different stages in the manufacturing process, starting firstly with wood based Tencel branded lyocell fibers, secondly with Santoni’s 3D-knitted shoe upper and thirdly, ForEver soles from Procalçado SA. The result is a finished shoe where the environmental impact is reduced to a minimum, Lenzing says.
Key production steps for sustainable shoes
Lenzing’s wood-based and compostable Tencel Lyocell fibers are used in the manufacturing of shoe components, making it the more sustainable and a circular choice. “In addition to these sustainability aspects, Tencel Lyocell fibers are incredibly smooth and strong and can do an exceptional job of managing moisture and body heat, all important performance features for shoes,” explains Lenzing.
Santoni, known for its circular knitting and seamless machines enabled the production of a one-piece upper with the “revolutionary seamless and ‘no-waste’ 3D Intarsia technology” with a production time of only 5 to 7 minutes per piece, including 3-D areas and eyelets for laces - mapping directly onto the foot.
Gluing the outsole is the last step in the manufacturing process and that’s where Procalçado comes into. Procalçado’s ForEver soles provide different sustainable sole solutions. Pura Latex is a material extracted from the stem of rubber trees harvested from certified and controlled sources. This is then combined with other materials of natural origin, including Lenzing’s wood-based Lyocell powder or the new biodegradable thermoplastic outsole incorporated with Tencel Lyocell powder, which contributes to less usage of non-renewable raw materials.
The material matters
“The path to environmentally sound solutions always starts with the first step. Eco design plays an important role to make products sustainable over the entire product life cycle. It starts with the selection of the materials used, continues with the manufacturing process and finally ends up with the disposal after usage,” says Birgit Schnetzlinger, Business Manager Footwear in Lenzing. “With this solution we offer the industry a botanic solution for consumers,” Schnetzlinger concluded.
Business intelligence for the fibre, textiles and apparel industries: technologies, innovations, markets, investments, trade policy, sourcing, strategy...
Find out more