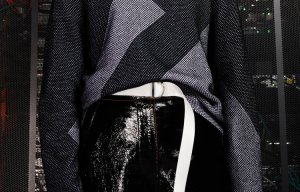
Evolution St. Louis receives investment
The RS 2 EL-F and RS 3 EL-F – KARL MAYER’s new machine range for producing circular bale and packaging nets. Textile nets have proved to be firm favourites for use in technical and semi-technical applications. They protect against the sun, wind and hailstones, keep mosquitoes and birds at bay, and can be used as ball-catching nets and packaging materials. Warp-knitted circular bale nets in particular have proved to be invaluable tools for use in harvesting crops, and the tec
12th June 2007
Knitting Industry
|
The RS 2 EL-F and RS 3 EL-F – KARL MAYER’s new machine range for producing circular bale and packaging nets.
Textile nets have proved to be firm favourites for use in technical and semi-technical applications. They protect against the sun, wind and hailstones, keep mosquitoes and birds at bay, and can be used as ball-catching nets and packaging materials.
Warp-knitted circular bale nets in particular have proved to be invaluable tools for use in harvesting crops, and the technology used to produce the nets is constantly being optimised and updated. To this end, KARL MAYER Textilmaschinenfabrik GmbH has been introducing a new group of machines for producing circular bale and packaging nets onto the market since last summer.
The RS 2 EL-F is the first member of this new family of net manufacturing machines from KARL MAYER. This two-bar raschel machine is intended to replace the old RS 2 NK-F. It is available in a working width of 226" and a gauge of E 6/6 (1 needle per inch), and produces circular bale and pallet nets extremely efficiently.
Thanks to the electronic guide bar control facility, which is an integral part of the overall machine concept, the new RS 2 EL-F can operate at production speeds of 1,500 rpm, which makes it up to 25% more efficient than its predecessor. Other advantages of KARL MAYER’s new machine include its cutting and clamping device, which can be used for automatically incorporating marking tapes, and its compact, cleverly engineered batching system, which guarantees a constant, firm edge build and a high winding density. The RS 2 EL-F also comes equipped with the KAMCOS® system, which results in increased productivity and flexibility, and can be linked up to the KARL MAYER Teleservice system. This is a component part of the KARL MAYER Service Plus package and maximises the machine’s operating availability. The procedures for handling the machine have also been simplified. For example, a pneumatic insertion device at the batching system makes it easier to position the empty roll, and the compact construction ensures that all areas of the machine are clearly visible.
The RS 2 EL-F has already demonstrated all these features in practice. After it was unveiled during an open house event at the company’s headquarters in July of last year, it passed all its production trials with flying colours and went into mass production in March.
The RS 3 EL-F is the flexible sister machine to the RS 2 EL-F and thus complements this family of net manufacturing machines. Equipped with a third inlay-processing guide bar, this latest development from KARL MAYER extends the range of patterns that can be worked at virtually any speed. The design of the machine also enables a speed of 1,500 rpm to be achieved, but this will, of course, depend on the lapping being worked. The possibilities of this are currently undergoing extensive trials in KARL MAYER’s development department. In addition to testing conventional pillar stitch/inlay constructions for covering bales of straw and hay and for securing silage, the development work has focused, among other things, on using the third guide bar for inserting an additional inlay. This can be incorporated in an even or counter notation arrangement, and enables the stability and density of the nets to be increased, if they are to be used as lawn/turf nets, for example. This ‘reinforcement inlay’ could also be partly incorporated at the points of central force insertion.
Different inlay arrangements, such as arranging the inlay over several courses, are also being studied. This results in reduced yarn consumption and a steeper inlay arrangement for a higher crosswise elongation when pulling the net in a crosswise direction. Water can also run-off more easily during storage of the bales of straw or hay. The additional crossing inlay yarn also guarantees adequate stability and makes it less likely that the contents of the bale will fall out during transport. All the different types of lapping can be worked quickly, easily and reliably using the electronic guide bar control facility, to produce cleverly engineered nets for packaging and securing agricultural produce and loose, compactable goods, such as paper, wood chippings, waste and recyclable materials.
The nets can also be used for securing pallets and containers during transport. The researchers at KARL MAYER are also currently investigating and testing other applications. The batching system for the RS 3 EL-F is also currently undergoing trials. The new design is intended to facilitate handling and thus reduce downtimes. The film slitting and drawing unit has also been modified to meet the new requirements, and has been fitted with new drives, for example.
The work being carried out to optimise and test the RS 3 EL-F machine is scheduled to be completed by the autumn of this year.
Business intelligence for the fibre, textiles and apparel industries: technologies, innovations, markets, investments, trade policy, sourcing, strategy...
Find out more