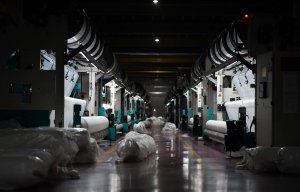
Karl Mayer’s game-changer in production management
Digital Production Management (DPM) from KM.ON will be officially released at ITM 2024.
28th May 2024
Knitting Industry
|
Obertshausen, Germany
KM.ON is launching a new software solution at the forthcoming ITM in Istanbul (4-8 June 2024), that improves shop floor management in the warp knitting industry. Digital Production Management (DPM), as the innovation is called, uses the possibilities of the Internet of Things (IoT) and state-of-the-art analyses to create maximum transparency in production and provide production managers with production-specific key figures in real time.
The insights into factory operations are worth their weight in gold and DPM can be used to recognise patterns - such as the occurrence of recurring faults during machine operation - optimise resource allocation and make data-driven decisions to increase efficiency.
With its comprehensive reporting options, DPM is integrated between KAMCOS and the customer's ERP into his company's system landscape.
Features in detail
Home view
- Overview of Factory Performance: displays key performance indicators for the entire factory, including daily tracked production data such as output in meters, overall efficiency, and under-performing machines
- Production Time: shows a distribution of machine operating hours, categorizing them into running, stopped, and offline times
- Live Machine Status: the status of all machines is displayed live, categorized by operational states such as running, stopped, or offline, and includes details on which machines have the longest downtime and offline times
- Output and efficiency: displays the meters produced and the machine efficiency for the last seven days, and visualizes their ratio
Pieces view
- Live production tracking: provides live data on the progress of each piece produced; easily identify which pieces are actively being fabricated and which machines are carrying out their production
Machines view
- Displays the current status of each machine ("running", "stopped" or "offline"). It is possible to filter by status to enhance clarity
- Operational Insights: includes data on machine running time over the last 24 hours and the remaining time until the current piece is completed
Output & Efficiency report
- Performance Analysis: analyzes the output in meters as well as machine efficiency across selected time periods, with options to view data for single or multiple machines
- In-depth Productivity Metrics: details on machine productivity, including output, efficiency, runtime, downtime and stoppages; illustrates the correlation between produced meters and efficiency per hour
Machine speed report
- Speed fluctuation: indicates change in the speed of a machine compared to the threshold set by the production manager. It reveals loss of speed and the possibility for process optimization on a shop floor, aiming to increase efficiency of production processes.
Activity report/Logbook
- Comprehensive Activity Log: compiles all machine stoppages and activities, details the duration, the type, and the proportion of each, such as yarn breaks or beam changes. Displayed activities are able to be customized according to the requirements of a given factory. The data on physical processes at the machine is entered via an input device by an operator.
Piece Quality Report
- Quality Insights: provides an overview of parameters that have impact on the quality of each piece produced, including speed change and yarn run-in change.
- Detailed Metrics: offers additional insights with details such as total length, number of stops, piece start/end times, and machine identifiers.
With its performance features, the DPM offers decision-makers and owners of textile companies a wide range of benefits.
“The digital production management solution enables bottlenecks to be identified, workflows to be simplified and operating processes to be optimised. This allows for higher productivity and lower costs,” explains Yevgeniya Nedilko, Cluster Lead Operational Excellence at KM.ON.
In addition, the administrative workload can be significantly reduced as the company can largely switch to a paperless working method. Staff can concentrate on their actual, value-adding work.
Yevgeniya Nedilko and her team are looking forward to many good discussions with their guests about DPM at ITM (4-8 June 2024, Tüyap Fair and Congress Center Istanbul, Hall 3 Stand 303A).
Business intelligence for the fibre, textiles and apparel industries: technologies, innovations, markets, investments, trade policy, sourcing, strategy...
Find out more