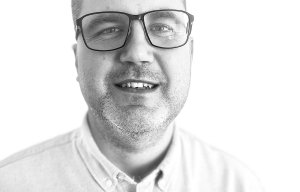
New subsidiary and new managing director
Revolutionising textiles manufacturing with digital shop floor management and DPM.
31st October 2023
Knitting Industry
|
Obertshausen, Germany
According to leading textile machinery manufacturer the Karl Mayer Group, the textiles industry stands on the brink of transformation, driven by the fusion of cutting-edge digital technologies with traditional manufacturing practices. In this era of unprecedented change, the introduction of digital shop floor management and innovative solutions like Digital Production Management (DPM) by the group’s KM.ON are reshaping the landscape of textiles production, enhancing efficiency, transparency, and sustainability across the industry.
Changing landscape of textile manufacturing
As the global economy evolves, businesses are tasked with optimising production elements to maximise value and adapt to an ever-changing market. The textiles industry faces a complex landscape characterised by economic uncertainty, fierce competition, rising input costs, and increasing consumer demands for sustainability and ethical practices. In response, textiles manufacturers are seeking innovative solutions that can streamline their production processes and enhance overall profitability.
Digital shop floor management: a paradigm shift
Enter digital shop floor management – a concept that signifies the integration of advanced information technologies into the heart of manufacturing operations. With the ability to provide real-time data insights, digital shop floor management is a transformative force that empowers textiles manufacturers to achieve optimal operational efficiency, cost savings, and control over their production processes. It marks a departure from manual and segregated approaches to a seamless, interconnected ecosystem.
Introducing DPM: a game-changer for textile manufacturing
At the forefront of the digital revolution is KM.ON's Digital Production Management (DPM), a ground-breaking software solution tailored specifically for the warp knitting sector. DPM leverages the power of the Internet of Things (IoT) and advanced analytics to create transparency on the shop floor, empowering production managers with real-time, production-specific key figures. With insights into factory operations, managers can identify patterns, optimise resource allocation, and make data-driven decisions that enhance efficiency. This real-time monitoring and analysis go hand in hand with DPM's capacity to provide operational control. From creating products and work orders to streamlining production planning, DPM centralizes and optimizes every aspect of the production process.
DPM's specialised features
Let’s delve into the specialised features that make DPM truly ground-breaking within the textile knitting sector, Karl Mayer says.
Performance Report
DPM's Performance Report offers a comprehensive overview of key data on factory performance. By comparing the performance of different shifts or machines during various periods, managers can identify patterns, optimize resource allocation, and drive continuous improvement.
Piece Overview
Keeping track of production progress becomes effortless with DPM's Piece Overview. Managers can access real-time information on the status of each piece and estimate completion times.
Quality Report
Ensuring top-notch fabric quality is paramount in the textile industry. DPM's Quality Report empowers managers to monitor and analyse quality-related data, such as stops, quality-related machine messages, and setting changes, enabling proactive measures to maintain consistent quality standards.
Article Management
Efficiently managing technical information on fabric is crucial for successful production. DPM's Article Management feature provides a centralized repository of fabric-related parameters, ensuring standardized and reproducible production processes.
Machine Report
At the heart of DPM's Machine Report lies real-time machine data. By providing live updates on machine performance, output, speed, and remaining time for beam changes, managers can optimize machine utilization, minimize downtime, and maximize productivity.
Production Planning
DPM's Production Planning feature enables efficient work order scheduling, optimizing machine usage, and minimizing idle time. With a clear view of production plans, managers can make informed decisions, ensuring optimal resource allocation and on-time delivery.
Advantages of DPM
The implementation of DPM brings forth a host of benefits for textile management and owners. Lean processes on the shop floor become a reality as bottlenecks are identified and operations streamlined, leading to increased productivity and reduced costs. The reduction of paperwork minimises administrative overhead, allowing personnel to focus on value-added tasks. Transparency into fabric quality and production progress empowers managers to proactively address issues and maintain quality standards.
Embracing sustainability and profitability
DPM doesn't just optimise production - it aligns with the industry's growing focus on sustainability. By optimising resource allocation, reducing waste, and enhancing overall sustainability, DPM ensures textiles manufacturers meet industry standards and customer expectations.
Pioneering digital transformation
KM.ON's DPM exemplifies the textiles industry's transformation through digitalisation, Karl Mayer says. By embracing DPM, textile fabric managers and owners unlock the potential for increased revenue and optimised costs. DPM's integration of real-time data, advanced analytics, and operational control paves the way for greater profitability amid the constantly shifting market environment.
The textiles industry is no longer confined to traditional production methods. The digital shop floor and solutions like DPM are ushering in a new era of efficiency, transparency, and sustainability. As textiles manufacturers worldwide navigate the challenges of a dynamic market, digital transformation offers a beacon of potential and opportunity. Through partnership with KM.ON and the adoption of DPM, textile manufacturers can redefine their processes, drive growth, and secure a thriving future in the ever-evolving textile landscape, Karl Mayer concludes.
Business intelligence for the fibre, textiles and apparel industries: technologies, innovations, markets, investments, trade policy, sourcing, strategy...
Find out more