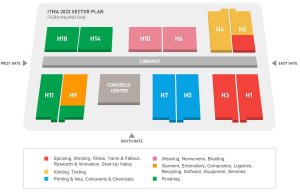
ITMA 2023 exhibition sector plan unveiled
Swedish textile machinery association members push forward new sustainable dyeing technologies.
5th April 2023
Knitting Industry
|
Stockholm, Sweden
Two members of TMAS, the Swedish textile machinery association, are at the forefront of a brand-backed revolution in replacing water and energy-intensive technologies for the dyeing and finishing processes that will take centre stage at this year’s ITMA exhibition in Milan from June 8-14.
“There are currently an estimated 90,000 jet dyeing machines in operation worldwide and between 60-70% of them are outdated to a factor of two-to-three in terms of the savings in energy, water and dyes and finishes that can be made – even with the latest conventional systems,” says TMAS secretary general Therese Premler-Andersson. “That productivity gap is considerably higher when considering the latest highly digitised and precise non-contact spray systems for these processes that have been introduced to the market by TMAS companies Baldwin and imogo in the past few years.”
Production tested and approved spray technology
Baldwin’s TexCoat G4, a non-contact spray technology for textile finishing and remoistening engineered and manufactured in Sweden, not only reduces water, chemicals and energy consumption, but also provides the flexibility to adapt to a customer’s requirements in terms of single and double-sided finishing applications.
It is designed to allow a controlled and optimal coverage of the exact amount of finish chemistry for reaching specific characteristics of the fabric through a combination of precision valve technology coupled with optimised software algorithms to ensure accurate and even finishing coverage with virtually no waste.
TexCoat G4 can reduce water consumption by as much as 50% compared to traditional padding application processes. In today’s world of volatile energy prices, imagine cutting gas and electricity costs by 35-50%. Productivity is also increased by 50% because of the lower wet pick up which allows for higher line speeds. Putting it simply, for replacing every 2-3 pads with a TexCoat G4 is equal to adding the productivity of an additional finishing line at a fraction of the cost, with no additional floor space and no added labour, says TMAS.
“Traditional textile finishing by padding is a wasteful, antiquated process,” says Rick Stanford, Baldwin’s VP of global business development. “High pick-ups drive high energy consumption and frequent bath changes generate a lot of avoidable chemical waste. Brands and mills are thankfully now starting to see environmental and economic benefits with the help of our non-contact precision spray systems. These systems increase product quality, improve mill profitability and deliver quantifiable sustainability benefits.”
True sustainability potential
Similar impressive savings can also now be made in textile dyeing with imogo’s Dye-Max spray dyeing technology.
It can slash the use of fresh water, wastewater, energy and chemicals by as much as 90% compared to conventional jet dyeing systems as a result of an extremely low liquor ratio of 0.6-0.8 litres per kilo of fabric. At the same time, considerably fewer auxiliary chemicals are required to start with.
The application unit of the Dye-Max consists of a closed chamber containing a series of high speed digitally controlled valves with precision nozzles for accurate and consistent coverage.
Fast changeovers with virtually no waste together with a high production speed enable a high productivity and unmatched production flexibility.
At ITMA 2023 the proven Mini-Max laboratory unit, used alongside Dye-Max installations for pre-determining application volumes and colour matching for Right First Time dyeing, will demonstrate the principles of imogo’s technology.
The huge potential of Dye-Max has been quickly recognised by brands seeking solutions to their sustainability targets and an industrial-scale installation is currently being commissioned. Further details will be announced prior to ITMA 2023.
“It’s fantastic that all of this innovation is taking place in Europe based on established know-how and forward thinking,” says TMAS Secretary General Therese Premler-Andersson. “Spray application technologies are a perfect illustration of how new digital technologies can lead to more sustainable production, in this case by replacing water-intensive processes with the highly precise and controlled application of dyes and chemistries as vapour.
“TMAS members – backed by Swedish brands and advanced research institutes – are playing an active part in pushing forward new concepts that work. Digitalisation now goes hand in hand with sustainability for the textile industry’s future.”
Business intelligence for the fibre, textiles and apparel industries: technologies, innovations, markets, investments, trade policy, sourcing, strategy...
Find out more