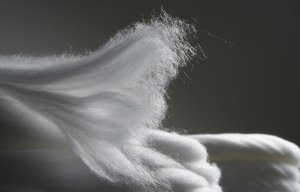
Lenzing continues to invest in Modal
Manmade fibres are durable, versatile and cost-effective and now account for more than 40 percent of all staple fibre consumption
20th October 2020
Knitting Industry
|
Bursa, Turkey
“Manmade fibres are durable, versatile and cost-effective. That’s why they have become indispensable in yarn production over the past decade and now account for more than 40% of staple fibre consumption,” says textile machinery manufacturer Truetzschler. Accordingly, the German company has supported this trend by developing highly specialized machines for manmade fibres that meet constantly rising expectations for quality and efficiency – and its TC 19i is now winning over customers worldwide, Truetzschler says.
The intelligent card TC 19i for manmade fibres was launched in 2019 and is now the international benchmark for manmade fibre processing. The results from major textile markets across Asia, Europe and the Middle East speak for themselves: customers were able to increase productivity by between 20% and 100%, while also improving quality (IPI) by between 20% and 55%, adds Truetzschler.
Turning sceptics into believers
Acarsoy Tekstil, a leading yarn manufacturer based in the Bursa province of Turkey, is a strong example of what can be achieved with the TC 19i for manmade fibres. The company has a daily production capacity of 65 tons of yarn across two production facilities, and manufactures a broad portfolio of cotton, linen, polyester, viscose, modal and lyocell yarns.
Cards are the beating heart of the spinning mill. We know we’ve made the right choice with the TC 19i for manmade fibres because it’s taking our superior quality to the next level.
Its processes include ring, compact, air jet, open end, core spun and siro spun technologies. Experts at Acarsoy Tekstil were initially sceptical when Truetzschler TC 19i cards were installed in the second air jet line for 100% viscose yarn (Ne 20 to 28). General manager Bülent DeÄŸirmencioÄŸlu, as well as his team of operations and maintenance managers, were unsure whether the required level of quality could be maintained when the TC 19i operated at such high speed. However, they were able to produce 60% faster with the TC 19i, and clearer cut numbers were 50% lower than the first line. In light of these impressive results, Acarsoy is now considering modernizing its other machines too.
“Cards are the beating heart of the spinning mill,” says Bülent DeÄŸirmencioÄŸlu (pictured centre above). “We know we’ve made the right choice with the TC 19i for manmade fibres because it’s taking our superior quality to the next level – while also cutting waste, reducing energy consumption and saving labour costs.”
Major improvements across all manmade fibre applications
Every single one of the manufacturers that tested the TC 19i for manmade fibres has been able to increase productivity and reduce yarn imperfections compared to predecessor machines, says Truetzschler. Of course, individual results vary depending on the customer’s specific application, raw material and process – but the TC 19i achieved success every time, the company adds. This success is largely made possible, Truetzschler says, by the T-GO gap optimizer, which has been specifically adapted to meet the requirements of manmade fibre applications.
The TC 19i’s technical details are as follows (see also diagram at top of article):
1. Stainless steel comb instead of screen fabric
2. Stainless steel cleaning flap
3.Stainless steel reserve trunk
4. Segmented feed tray
5. Special opening rollers for higher speeds
6. Stainless steel reserve trunk
7.More carding and less cleaning elements
8. WEBFEED with a large needle roller
9. T-CON 3 and T-GO Gap Optimizer for manmade fibres
10. Additional deflection roller
11. New doffer clothing TCC NovoDoff 3211″
“For cotton processing, a very narrow carding gap is often advantageous for the carding result – but this doesn’t apply to manmade fibres,” says Christoph Leinders, who was responsible for the design of the TC 19i.
“Our T-GO gap optimizer uses advanced, intelligent sensor technology to make sure the machine always maintains the best possible carding gap for the manmade fibre material, blend or application that is being processed. This gives the TC 19i a big advantage over machines from our competitors. We always know the exact carding gap and can adjust it during production using algorithms that we specifically developed for manmade fibres. This means changing environmental conditions or differences in the skill level of the individual operator no longer affect the carding gap setting – so quality levels remain constant.”
The T-GO gap optimizer for manmade fibres is as easy to operate as its counterpart for cotton Truetzschler explains. Only a few clicks on the display are required, and there’s no need for time-consuming flat setting work after each maintenance or re-clothing.
A winning combination of new and proven features
The excellent performance of the TC 19i for manmade fibres is made possible by several new and proven features. The doffer clothing NovoDoff 32, for example, has been specifically developed for manmade fibres by Truetzschler Card Clothing, a subsidiary of Truetzschler that is located in the Black Forest region of Germany. Its engineers invented a new process technology that makes the clothing even more robust and durable, and further improves quality while reducing maintenance requirements. Of course, the new card retains the outstanding features that have proven their performance in manmade fibre applications over many years, says Truetzschler.
All metal sheets in the tuft feeder and the transfer section to the card are made of stainless steel to ensure an optimal flow of manmade fibres. All covering elements for the cylinder and doffer are made of high precision, eloxated aluminium. A stainless-steel sliver coil tube and coiler plate ensures gentle sliver guidance during sliver coiling. And the pre-opener system of the TC 19i features one large roll with a special needling and surface treatment.
This makes it possible to reduce yarn imperfections (IPI) by up to 30% compared to rolls with conventional wires, while the average lifetime of the needle roll is twenty times longer than a conventional roll, claims Truetzschler. As manmade fibres gain importance for yarn production, the TC 19i is a powerful new card that delivers valuable performance across a wide range of applications.
Customers at spinning mills around the world are taking advantage of this new benchmark for manmade fibre processing – and moving ahead of their competitors by increasing productivity, efficiency and quality, concludes Truetzschler.
Business intelligence for the fibre, textiles and apparel industries: technologies, innovations, markets, investments, trade policy, sourcing, strategy...
Find out more