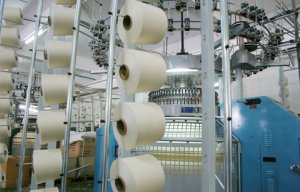
Beverly Knits expands operations
Leading warp knitting machine builder Karl Mayer has revealed details of its recent collaboration with fellow German finishing machine builder Brückner Textile Technologies in the area of the continuous finishing of seamless warp knitted garments. Karl Mayer explains the fruitful collaboration in depth "Today's fashions are stylish and comfortable, and change faster than they have ever done before. Manufacturers along the entire production chain react to these dy
14th November 2011
Knitting Industry
|
Obertshausen
Leading warp knitting machine builder Karl Mayer has revealed details of its recent collaboration with fellow German finishing machine builder Brückner Textile Technologies in the area of the continuous finishing of seamless warp knitted garments.
Karl Mayer explains the fruitful collaboration in depth
"Today's fashions are stylish and comfortable, and change faster than they have ever done before. Manufacturers along the entire production chain react to these dynamics by constantly refining and revamping their production techniques, and cooperating closely with other companies is the best way of optimising the results.
Cooperation between Karl Mayer and Brückner Textile Technologies is one example of how highly efficient manufacturing stages can be cleverly linked up to each other. This cooperation led to the development of a technique for continuously finishing seamless, warp-knitted items.
The seamless components are produced in a piece on an RDPJ machine and selvedges are also knitted-in at the same time. These extra strips of material are used for pinning the fabric in the stenter during subsequent heat-setting. This enables the tubular components to be finished in the open width. This processing sequence, which features seamless transfer between the processes, has been successfully tested by a finishing company. Details of the relevant procedures will now be presented.
The RDPJ and DJ machine series are perfect for producing seamless goods and items that require very little make-up. The two-bar raschel machines are uniquely flexible. They can be used to produce:
The fabric parameters can be set and monitored accurately thanks to the machine's special technical features, such as the Multispeed facility, and other innovative solutions, such as the patterning, yarn feed and fabric take-down systems.
For the practical trial, the RDPJ 4/2 (Fig. 1), with a working width of 138" and a gauge of E 24, produced three long-sleeved shirts in a fabric panel. The sequence of articles was defined by two selvedges for subsequent mounting in the stenter (Fig. 2). A core-spun yarn was processed in the jacquard bar and a standard yarn was processed in the ground guide bars. The fabric was made up of 81% PA 6.6 and 19% elastane.
The yarns used to produce the long-sleeved shirts on the RDPJ:
GB2: PA6.6 dtex 40f34
PJB 3-1: PUE dtex44 + PA6.6 dtex 38f34
PJB 3-2: PUE dtex44 + PA6.6 dtex 38f34
PJB 4-1: PUE dtex44 + PA6.6 dtex 38f34
PJB 4-2: PUE dtex44 + PA6.6 dtex 38f34
GB5: PA6.6 dtex 40f34
When relaxing and heat-setting conventional seamless articles, the tubes and stockings are normally finished individually. In this case, each separate piece is pulled onto a special frame before heat-setting. These small units consist of a dryer, a steam chamber and a tunnel for hot-air heat-setting. Separate technical options are available for finishing straight-cut tubular items and stockings.
However, tubular finishing is not ideal when processing elastane-containing knitted fabrics because of the size of the processing zones available, the achievable temperatures and the process reliability.
Brückner Textile Technologies can now offer state-of-the-art finishing technologies for after treating high-stretch articles. Tubular, seamless articles can now be finished in the open width on the stenter with its tried-and-tested process control facilities by incorporating selvedges into the fabric panel. A pre-heat-setting stage can now be linked up directly to the warp knitting process.
The main advantage of doing this is that there is less tendency to tear, crease or snag. The risk of colour variations caused by excessively high heat-setting temperatures, variations in the elasticity, and fluctuating widths can also be avoided. The following processing stages include continuous jet dyeing and subsequent heat-setting.
The Power Frame VNB stenter (Fig. 3) works with a perforated belt carrier for supporting the fabric as it is transported through the machine. The belt is also moved vertically at short amplitudes to produce a gentle vibrating effect, which relaxes the fabric and promotes shrinkage in the steamer zone.
Further technical features of the machine include:
The features of the machine produce a fabric with accurate and reproducible dimensions, since the weight of the fabric in the length and width are optimally uniform. The finishing trials produced minimal differences between the inner and outer fabric panels.
The maximum variations were +/- 1 cm. After subsequent washing at 60°C, the maximum residual shrinkage was 0 to 5%. Some general recommendations for treating the textile have been drawn up on the basis of the trials:
The fabrics paths should be as short as possible, especially at the entry point of the machine, in order to minimise elongation; support drives for the guide rollers needed are an advantage
The perforated belt should be positioned close to the entry and exit rollers for avoiding sagging and thus preventing the fabric from becoming longer
There should be a small gap between the pin bar and the perforated belt to avoid stitch distortion and weight variations, especially around the edges of the fabric.
Market reaction to the warp-knitted seamless items With their special characteristics, the items produced on the RDPJ and DJ are setting the trend in fishnet stockings, lingerie, outerwear, medical textiles and sportswear.
For example, collections developed by Cifra, Shiseist, Leonisa, Zerofit and mash mania are already impressing the market. Manufacturers are particularly interested in the possibilities of combining functional zones and specific compression/control characteristics. Conventional methods for working zones with different levels of stretch in the fabric involve using different types of materials, which are combined in intricate and complex designs.
This method involves a great deal of time and effort to procure the materials, incurs high production costs, and produces seams that are uncomfortable when the garment is worn. The unique productivity of double-bar raschel machines also gives rise to financial advantages.
At a speed of 250 to 300 rpm, roughly 20 long-sleeved shirts, 240 pairs of tights, or approximately 55 shapewear briefs can be produced on the RDPJ in a gauge of E 24. This efficient machine can also process a wide range of different yarn materials. For example, non-stretch yarns can be processed in the jacquard zone and even uncovered elastane can be processed to produce a variety of different constructions."
Business intelligence for the fibre, textiles and apparel industries: technologies, innovations, markets, investments, trade policy, sourcing, strategy...
Find out more