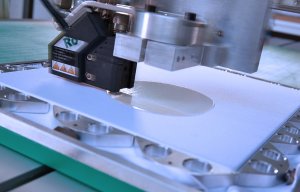
Adding value through additive manufacturing
Friedel Dickmeiß and Jörg Alexander, Oerlikon Barmag Statistics reveal that spinning line capacities are becoming increasingly large The majority of recent installations for polyester have been spinning lines directly connected to a common reactor. Lines of this kind are economically prudent, although flexibility is very limited compared to extruder spinning lines. Here, additive injection and mixing systems can help regain this lost flexibility.
28th March 2013
Knitting Industry
|
Remscheid
Article written by Friedel Dickmeiß and Jörg Alexander, Oerlikon Barmag
Statistics reveal that spinning line capacities are becoming increasingly large.
The majority of recent installations for polyester have been spinning lines directly connected to a common reactor. Lines of this kind are economically prudent, although flexibility is very limited compared to extruder spinning lines. Here, additive injection and mixing systems can help regain this lost flexibility.
With the help of these systems, masterbatches and additives can be introduced into the melt path at various points between the reactor and the spinning positions. Any number of units can be installed at one reactor spinning line. Depending on the position of the melt distribution pipework, the injection unit can feed additives into anywhere between 2 or more than 48 spinning positions. Today, units are already in operation in 2, 4, 12 and 24 position direct spinning lines.
Fig.1.
Thus, the variety of yarn to be manufactured simultaneously can be increased dramatically. Typically, customers inject the following additives: TiO2 masterbatches, various colour masterbatches, flame retardants, UV stabilizers, etc.
In order to find suitable positions, numbers and capacities for installing these additive injection and mixing systems, the following aspects need to be taken into consideration:
In all cases, the system comprises three main components: feeding extruder, metering pump and powered dynamic mixer. A typical configuration is shown in Figure 1.
In these processes, the three major conditions that need to be fulfilled by the additive feeding and mixing systems are:
1. The masterbatches or additives need to be injected in a defined ratio with very high accuracy and reproducibility. This is achieved by using a metering pump that runs at a pre-calculated speed, taking the speeds of all relevant spinning pumps into account. The design of the metering gear pumps guarantees high volumetric efficiency, which makes the metering accuracy independent of viscosity and melt-pressure variations.
Due to the very abrasive behaviour of the masterbatch , the metering pumps are partly manufactured from PM steel. In order to reduce the number of bends in the melt pipes for the entire masterbatch melt system, “inline design” metering pumps are used nowadays.
Fig.2.
2. The masterbatches or additives need to be mixed into the main polymer stream in a very even manner so as to achieve the optimum homogenization of all components. This function is carried out by the powered 3DD mixer (three-dimensional dynamic mixer). The arc-shaped cavities of the internal rotating section and the stationary cylindrical section divide the axial melt streams into
extremely fine layers, which are constantly rearranged in the tangential and axial directions and then reunited. The melt flow characteristics inside the mixer combine the two principles of mixing: the dispersive mixing effect, with the high-shear principle, and the distributive mixing effect, which divides the flow into a large number of small units. Distributive mixing is designed to improve the spatial distribution of the components, while dispersive mixing can cut agglomerates wherever minimum stresses and deformation are required. Thus, melt is cut into thousands of small slices, resulting in excellent mixing results.
A broad range of mixer speeds is possible, independent of the melt volume passing through the mixer. Insufficient mixing energy will result in poor homogeneity. On the other hand, excessively-high mixing power will cause high melt temperatures and a high pressure drop. In the case of the 3DD mixer, selecting the appropriate rotor speed generates the desired mixing effect.
In addition to the mixing elements, the rotor inside the mixer also incorporates a metering screw section. This enables the mixer to work with virtually no pressure drop.
The pressure drop necessary for mixing is compensated by the pressure generation in the screw section. This allows the retrofitting of this mixing system without the need for additional booster pumps.
The barrel of the mixer is electrically heated and cooled by air blowers. The melt temperature can be influenced by heating or cooling the melt. For this reason, the melt temperature at the mixer outlet, for example, can be kept at the same level as at the inlet.
3. Processing of masterbatches needs to be trouble-free over long periods of time. Today, masterbatches are highly pigment-loaded. This makes the design of the entire system extremely challenging so as to avoid any stagnation areas. In addition to the special coating of the feeding extruder’s screw, the melt path needs to be as short and straight as possible. An easy-to-operate discharge valve allows the feeding extruder to be flushed when one masterbatch is replaced with another. Using a freezing valve, the mixer can be separated from the additive supply in the event that production does not require the addition of masterbatches or additives.
A second positive feature of these systems is the environmentally-friendly introduction of the dyes into the yarn. The experience acquired from the systems installed to date shows that – even for the manufacture of very demanding types of dyed yarns suitable for the automotive industry – additive injection and mixing systems are a convincing solution for direct spinning lines.
Fig.3.
The Oerlikon Barmag range of products covers capacities of between 50 kg/h and 5,000 kg/h for the main polymer flow, with mixers with diameters of between 60 mm and 350 mm and capacities of 3 kg/h to more than 450 kg/h for the masterbatch polymer flow to be injected. If the feeding extruder is equipped with an additional batch metering unit, the capacity of the masterbatch flow can be as low as 1.0 kg/h.
This also makes these systems suitable for supplying smaller lines with just two spinning positions, for example. A further option is a bypass pipe with two 3-way valves to bypass the unit if required. Chip dryers are required for hydrophobic granulates such as PBT- or PET-based masterbatches.
All the equipment is displayed in figure 2. Figure 3 shows a system prior to shipment.
Oerlikon Barmag
Zweigniederlassung der Oerlikon Textile GmbH & Co. KG
Leverkuser Straße 65, P.O. Box 11 02 40, 42862 Remscheid, Germany
Phone: +49 21 91/67-0
Fax: +49 21 91/67-12 04
Oerlikon Barmag
Zweigniederlassung der Oerlikon Textile GmbH & Co. KG
Zwickauer Straße 247, D-09116 Chemnitz, Germany
Phone +49 371 23 88 240
Fax +49 371 85 21 42
Oerlikon Neumag
Zweigniederlassung der Oerlikon Textile GmbH & Co. KG
Christianstraße 168 – 170, D-24536 Neumuenster, Germany
Phone: +49 4321 305-0
Fax: +49 4321 305-212
Business intelligence for the fibre, textiles and apparel industries: technologies, innovations, markets, investments, trade policy, sourcing, strategy...
Find out more