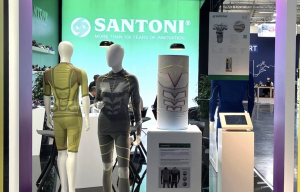
New selective terry options with Santoni SM8-TOP2ST
Karl Mayer’s new ISO Cotton combined with the TM 4-TS EL sets new standards in the production of terry fabrics.
25th October 2021
Knitting Industry
|
Obertshausen, Germany
Cotton terry fabric can be produced efficiently and sustainably using warp-knitting technology, so it’s no surprise that the Karl Mayer production equipment required for this process is in demand. The German company’s TM 4-TS EL terry machine, 186 inches, in gauge E 24, and the new direct warping machine for the production of cotton sectional beams for warp knitting, the ISO Cotton are the perfect combination.
The new, highly efficient solution for warping the natural staple fibre was developed by Karl Mayer in 2020 and is based on the extensive expertise of the world’s market leader in warp preparation for weaving.
The first models of the powerful direct warping machines have already been sold to test customers, with an ISO Cotton leaving the Karl Mayer factory in Changzhou only at the beginning of July 2021.
Direct warping of cotton – a demanding process
As part of a Karl Mayer workshop at ITMA ASIA + CITME 2019 – before the development work began – the question of whether a direct warping machine designed specifically for processing cotton was needed was discussed with the company’s experienced weaving preparation specialists.
The answer was clear. For an optimum warping process, the natural fibre yarn must pass from the creel to the sectional warp beam as directly as possible, without passing through the numerous deflection points that are usually involved in the warping of filament yarns. Otherwise, too much fluff will build up or too much cleaning work will be required.
What’s more, unlike in weaving, the circumferences of the sectional warp beams used for each order must be absolutely identical, as they are processed simultaneously on the TM 4-TS EL and arranged next to each other on a single axis. These two basic requirements meant it was necessary to develop a special machine.
Sophisticated solutions for cotton processing
The new ISO Cotton offers the incredibly short yarn paths, and thus a low-wear yarn journey. The material is led from the eyelet board, via the comb, directly to the main reed and thus to the take-up. An electronically controlled press roller ensures that the master and copy beams have the same circumference. If deviations occur, the contact pressure is adjusted to compensate accordingly. The resulting solution is completely new and highly efficient.
“We can copy the circumference to within 1 mm without any problems,” said product developer Michael Bender following extensive in-house warping tests.
In addition to circumference measurement, the ISO Cotton also comes with a new and innovative yarn tensioner. The new tensioner works with pairs of discs whose partners are pressed together with adjustable force via a magnetic field, and thus regulate the yarn tension based on the type of yarn.
Highest warp quality and productivity
Thanks to its innovative solutions, ISO Cotton produces sectional warp beams of the highest quality. The beams feature extremely homogeneous density, an absolutely cylindrical structure, completely identical circumferences and equal thread lengths. The computer-controlled length measuring system allows a length accuracy of 0.1%. The threads are also arranged precisely and blowing devices on the comb and the main reed keep the contamination level to a minimum.
In addition to this, the ISO Cotton also stands out thanks to its minimal scrap rates. For example, it is fitted with a kick-back device that ensures that the press roller swings away when the machine stops, thus protecting the wrap. Should a yarn break, a computer-controlled brake system enables short, precise braking distances.
In addition to its yarn handling, the ISO Cotton also impresses on account of its productivity – with warping speeds of up to 1000 m/min – and its price. Although it represents an extra purchase, application-specific cutting means investing in the ISO Cotton quickly pays off.
Different warping options
The ISO Cotton is available in two variants. For beginners, there is the ISO Cotton 21/40, which produces sets of 8 to 10 sectional warp beams each, with a maximum diameter of 40 inches. This model operates with a yarn tension of up to 200 N and a maximum press roller force of 300 dkN.
Karl Mayer also has the bigger Iso Cotton 84/40 in its range. The machine supplies the TM 4-TS EL with two sectional warp beams per axis, measuring 2200 mm x 1,000 mm, draws off the yarn with a tension of up to 450 N, and ensures identical circumferences with a maximum contact pressure of 600 dkN.
Combining the TM 4-TS EL and the ISO Cotton is a particularly effective way of ensuring maximum efficiency. For manufacturers who want to make fabrics using the on-trend mix of absorbent cotton on the inside and soft microfilaments on the outside, the use of a DS EC 2 21/30 is also recommended.
Potential factory layouts combine three TM 4-TS EL units with an ISO Cotton 21/40 and a DS EC 2 21/30. When using the larger ISO Cotton 84/40, the two direct warping machines can even supply 12 TM 4-TS EL units.
In addition to the new ISO Cotton, a conversion kit has also been developed so that existing Warpdirect and Bendirect models can be used to produce cotton sectional beams for warp knitting. “By including this option, we hope to appeal to weaving companies that are looking to switch to warp knitting. Whether a retrofit is worthwhile or not must be investigated thoroughly on a case-by-case basis,” says Michael Bender.
Business intelligence for the fibre, textiles and apparel industries: technologies, innovations, markets, investments, trade policy, sourcing, strategy...
Find out more