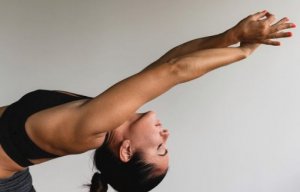
ISCC+ certification for Sensil ByNature
Specialst knitted elastic fabrics producer Elastic Fabrics Europe GmbH has been awarded the coveted Oeko-Tex Standard 1000 for its environmentally friendly production methods. Since December 2008, the German company's plant in Neukirchen, Hessen, has been using proven environmentally friendly production methods to make quality products for many top brand names such as Triumph, Felina, Chantelle, Aubade and Lejaby. After two months of preparation, Elastic was cer
7th August 2009
Knitting Industry
|
Neukirchen
Specialst knitted elastic fabrics producer Elastic Fabrics Europe GmbH has been awarded the coveted Oeko-Tex Standard 1000 for its environmentally friendly production methods.
Since December 2008, the German company's plant in Neukirchen, Hessen, has been using proven environmentally friendly production methods to make quality products for many top brand names such as Triumph, Felina, Chantelle, Aubade and Lejaby. After two months of preparation, Elastic was certified as an environmentally friendly production site in accordance with the criteria set by the Oeko-Tex Standard 1000. Elastic can now also mark its fabrics and lace with the Oeko-Tex Standard 100plus label, meaning the products have been both tested for harmful substances and produced in an environmentally friendly way.
Founded as a family firm in 1958, the company currently led by CEO Falco Weidemeyer has an annual turnover of €22 million. Around one hundred and thirty highly trained staff working with state-of-the-art machines allows the firm to maintain its leading position in the sector, producing approximately 300,000 metres each month in a full spectrum of quality fabrics. As well as its sought-after knitted fabrics for products such as sportswear and lace materials for lingerie, Elastic's product-range also includes technical textiles for medical and automobile applications as well as exhibition displays and other industrial uses.
A high level of quality-consciousness and outstanding readiness to innovate are part of the company ethos at Elastic. Diversified technological equipment serves as the foundation for these characteristics. Circular knitting machines, warp and raschel knitting machines, weftloc, rascheltronic and computer-controlled raschel lace machines are all used. These machines enable Elastic to maintain high levels of output of guaranteed consistent quality while responding very quickly and flexibly to its customers' special needs.
An example of the tailor-made services Elastic can offer is the market launch of Triumph's Pure Origin line of lingerie, a co-operative project featuring organic cotton with 20% elastane content. At the same time, both the raw fabrics that have been produced and the ready-made, finished knits are subjected to comprehensive quality control testing before they are delivered to the top players in the international lingerie, sportswear and swimwear industries in Europe, Asia and USA. Quality assurance measures include continual monitoring of the functional properties of the fabrics on the one hand and checks of additional parameters such as colourfastness, durability, shrinkage, and workmanship on the other hand.
Falco Weidemeyer emphasises, "We aspire to make products with genuine technical and aesthetic added-value. Responsibility for the environment and our surroundings, in other words, ecological and social sustainability play a particularly major role for us as well. That has motivated us to become one of the first in our sector to implement such criteria in accordance with Oeko-Tex Standard 1000 and 100plus.“
Documentation of successfully implemented environmentally-friendly production for consumers and traders is a logical step when sustainable production is viewed as contributing to success in that it sets a company apart from the competition. One of the first steps needed to be taken for certification in accordance with Oeko-Tex Standard 1000 was a detailed analysis of the conditions at Elastic in order to assess all the relative environmental impacts, and the need, if any, to make changes. Some of the issues addressed were, where in the production process, for example, is waste produced? How could patterns be cut to reduce excess to a minimum? Where are local waste recycling facilities and so on?
Once an inventory was taken, the measures were implemented at the firm and an environmental management system was established. An environmental management handbook, with binding guidelines for all parts of the company and staff, was also published and environmental protection officer Klaus Krey was appointed. His responsibility is to co-operate closely with management to ensure compliance with environmental and social criteria at the production facility in Neukirchen.
Klaus Krey summarises the essence of the Oeko-Tex auditing programme: "Certification in accordance with Oeko-Tex Standard 1000 isn't the ultimate goal for us. Instead, it's the place we crossed the starting line when it comes to sustainability and environmental protection.“
The aim is continual improvement of the company's environmental record. "That's why we provide continuing, regular training for all our staff in all the relevant areas," continues Krey, "so that all the employees can apply the principles in the handbook daily as they do their work.“ The on-site audit was carried out by Oeko-Tex experts Bernhard Schlund, Dr. Helmuth Hammerl and Ortrud Weber (Hohenstein Research Institute). Elastic's quality assurance manager, André Jubel, represented elastic, and all the preparations for certification were complete in just two months.
Business intelligence for the fibre, textiles and apparel industries: technologies, innovations, markets, investments, trade policy, sourcing, strategy...
Find out more